Heat used several times instead of simply being burnt
Heating modernisation from the hydraulic side: Gradual return utilisation in the heat distribution and two-zone charging and discharging for buffer tank
The main approach for the energy optimisation of the heating system in the branch of the SHK specialist wholesaler Richter + Frenzel in Schweinfurt was in the system hydraulics. There were heat surpluses in the existing system that could still be put to good use elsewhere. However, the question was how the heating water mass flows should get there. The optimisation of the system hydraulics was achieved through the interaction of multi-way mixing valves and a special distributor with an additional return chamber. The available surplus heat can thus be used in stages. At the same time, a more efficient charging strategy was found for the existing buffer storage tank, and the heat generators run continuously in condensing mode.
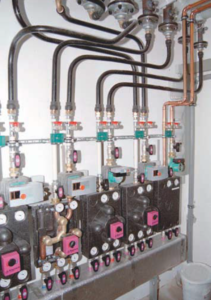
Fig. 1: For the heat distribution of the heating circuits, the multi-way mixing valves from HG Baunach Gmbh & Co. KG together with a new type of three-chamber distributor from Magra are used. The sequence of the distributor outlets depends on the temperature gradient in the return flow in the direction of flow to the boiler.
The combination of high- and low-temperature systems in a heating system is no longer an exception, nor is bivalent heat generation by CHP and condensing boilers. However, the task of ensuring the required system temperatures in the heat distribution and supplying the necessary low return temperatures to the heat generators is somewhat more demanding. Energy optimisation was the primary goal for the modernisation of the heating system in the Schweinfurt branch of Richter + Frenzel, a specialised plumbing, heating and air-conditioning wholesaler. Although the gas boiler was also replaced with a new condensing boiler, the modernisation measures concentrated mainly on the system hydraulics. Since the re-commissioning at the beginning of November 2006, the CHP unit has been running continuously, and condensate is continuously flowing out of the condensing boiler. Defined system temperatures prevail throughout the entire plant, and this with minimal control effort.
Focus on condensing and combined heat and power generation
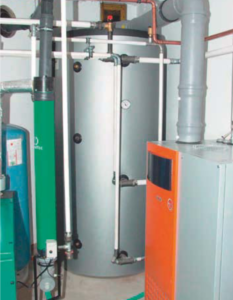
Fig. 2: The basic heat load is covered by a Dachs CHP from Senertec which works on the buffer storage tank (centre back). The back-up heating is provided by a 130 kW gas condensing boiler from Wolf heating technology.
A look back: The Richter + Frenzel branch was built in 1984 with a bathroom showroom, a goods and collection warehouse and an office wing. The heating system has to supply three high-temperature and two low-temperature circuits: The goods and collection warehouse with an area of 900 m² to be heated is heated with VL/RL 75/50 °C via air heaters, as are the underfloor convectors in the bathroom showroom and the hot water preparation in the bathroom oasis, which is carried out via a plate heat exchanger. The underfloor heating in the 600 m² bathroom exhibition and the underfloor heating for 200 m² of office space were designed as low-temperature systems (40/30 °C). A Dachs CHP unit from Senertec with an output of 15 kWth was later retrofitted to raise the return flow of the existing gas boiler. However, at 210 kW, this was oversized. In the course of the recently completed modernisation, it was replaced by a gas condensing boiler from Wolf Heiztechnik of the type MGK with 130 kW, which, thanks to its large modulation range, takes over the reheating and thus reinforces the combined heat and power system as required. With its compact dimensions (W x H x D = 1350 x 1300 x 600 mm), the wall-mounted medium boiler, which was only introduced as a novelty at the IFH 2006, fits through any standard door and could therefore be easily installed in the existing boiler room. The heat produced by the CHP is stored in a 1000-litre buffer tank. The electrical energy produced in the process (approx. 5 kWel) supplies the building's outdoor lighting as well as all consumers in standby mode.
Return use in the direction of the low temperature ranges
The planning task was now, on the one hand, to maximise the running times of the existing small CHP unit and, on the other hand, to ensure that the new gas condensing boiler actually uses the calorific value from the exhaust gas. For this purpose, the principle of return utilisation should be implemented on the heat distribution side: If the temperature from the return of a heating circuit is sufficient to supply another heating circuit with a lower temperature level, this available heating heat should first be used for this purpose before accessing the flow. For the modernisation planning, the performance data and mass flows of the existing system were first recorded. The resulting system calculation showed that there was still a large surplus of heating heat from the return flow of the high-temperature circuits, which could not be used effectively in the low-temperature circuits. In addition, the return temperatures were too high for both the CHP unit and the planned condensing boiler. "Under these circumstances, it was not possible to achieve efficient spreading in the buffer storage to make maximum use of the buffer volume. Likewise, it was not possible to achieve low return temperatures and thus effective utilisation of the condensing value with the existing hydraulics - the mixing of the returns from the high-temperature and low-temperature circuits would have resulted in lukewarm heating water," reports Hans-Georg Baunach, who designed the hydraulic optimisation of the system with the multi-way mixing valves he developed and a new type of three-chamber distributor built by Magra.

Fig. 3: Wolfgang Mika, Sales Manager at Richter + Frenzel in Schweinfurt, anticipates considerable savings in energy costs by optimising the plant hydraulics.
Multi-way mixer and three-chamber distributor
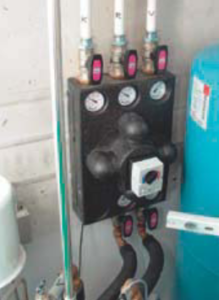
Fig. 4: The rendeMIX between the CHP unit and the buffer storage tank causes the storage tank to be loaded according to the two-zone principle.
For the hydraulics of the existing heating system at Richter + Frenzel in Schweinfurt, two functional principles had to be realised:
- Return utilisation in two stages: The excess heat from the heating circuits with high system temperatures (75/50 °C) should be used for the low-temperature heating circuits (40/30 °C) in such a way that the return flow is fed directly to the respective NT heating circuit via a multi-way mixing valve and via the distributor or collector. For example, the return temperature of the air heaters in the hall and the underfloor convectors in the bathroom exhibition is sufficient to supply the underfloor heating systems in the exhibition and in the offices on the supply side. The returns from these low-temperature circuits were to be fed separately into the lower part of the buffer storage tank. This was to prevent them from mixing with the unused surplus from the returns of the high-temperature circuits.
- Defined temperature spread and low return temperatures: In the existing buffer tank, which according to Hans-Georg Baunach's calculations is rather tightly dimensioned at 1000 l, the highest possible spread should be achieved. In this way, as large a buffer volume as possible should always be available with a useful temperature for the high-temperature heating circuits. The previously mentioned return utilisation ensures low return temperatures in order to obtain the longest possible running times for the CHP unit.
In order to mix and divert the heating water flows according to heat demand and supply, the multi-way mixing valves "rendeMIX" from HG Baunach GmbH & Co. KG were used. The mixers are designed as compact installation blocks with insulation shells, into which shut-off ball valves and thermometers are already integrated at the factory. The main difference between the multi-way mixer "rendeMIX 3×2 VL 5" developed by HG Baunach and conventional three- and four-way mixers is that it has three connections to the manifold:
- Two supply inputs for hot and warm water,
- a return outlet for cold water.
The hot water inlet is connected to the flow chamber of the manifold, the hot water inlet to the middle manifold chamber. The middle chamber is fed downstream with the still warm return from the high-temperature circuits, which corresponds to the principle of return utilisation. The return flows from the low-temperature circuits, however, are fed into a separate, third return chamber. This means that the warm return surplus reaches the buffer separately and without mixing, which corresponds to the principle of two-zone discharge. The three-chamber distributor is part of the HG Baunach range and is manufactured by Magra.
The three chambers of the heating manifold communicate with two zones of the buffer tank:
- The flow manifold receives heating water from the upper temperature level, which is reheated via the intermediate condensing boiler if required.
- Although the middle distribution chamber primarily acts as a return, it also works in the opposite direction and is connected to the buffer tank at half height. When the buffer is fully charged, the available heating water temperature from the middle level can thus be used. Withdrawal from the middle storage zone has the advantage that a sufficient reserve can be maintained in the upper zone. The multi-way mixers of the high-temperature circuits are connected to the middle distribution rail with one flow and one return connection each. Depending on the buffer temperature and heating demand, these circuits thus either receive heating water from the storage tank, or the heating circuits feed back into the underfloor heating circuits or into the buffer with "unconsumed" return temperature.
- Only the low-temperature returns of the underfloor heating systems of the exhibition and office wing flow into the third distribution chamber. This second stage of return utilisation goes to the lower buffer storage level, thus supporting the intended spreading and also ensuring the utilisation of the condensing value.
CHP runs around the clock
The return flow from the third distribution chamber also flows through a flue gas heat exchanger, which was retrofitted to the CHP unit in the course of the plant modernisation. This increases the heat yield of the burnt gas and thus the overall efficiency of the system. The condensing boiler only feeds directly into the flow leading to the manifold after the buffer storage tank, so that only the CHP unit heats the contents of the storage tank. With a modulation range of 19 to 100 % or 24 to 126 kW (in condensing mode), the condensing boiler fully meets its task of reheating. This also fulfils the planning specification of optimised condensing use, as R + F sales manager Wolfgang Mika confirmed to IKZ-HAUSTECHNIK during an on-site visit: "The fact that the condensing boiler is actually running in the condensing range can be seen from the fact that the condensate lifting unit has pumped out several times within half an hour." In the 40/30 °C range, the condensing boiler achieves a standard efficiency of 108 %.
Two-zone principle optimises heat supply and energy utilisation
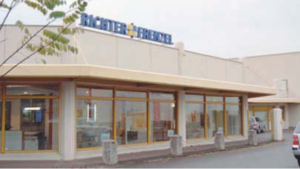
Fig. 5: The heating system at the Richter + Frenzel SHK wholesaler's branch in Schweinfurt was optimised in terms of energy. The main focus was on the system hydraulics.
After the modernisation, Hans-Georg Baunach describes the system as "calorific value-compliant". In terms of control technology, the energy-optimised system appears uncomplicated. The actuators for the mixers are controlled in a simple manner using conventional weather-compensated controls from the Wolf boiler accessories (230 V three-point signal). The connections to the air heaters in the hall areas were fitted with thermostatic valves and remote sensors that control the flow rate based on the air temperature and fan operation. RTL valves were installed on the return side for the underfloor convectors in the bathroom exhibition in order to limit the return temperature upwards to a value that makes sense for the underfloor heating systems. The control system for the CHP was additionally extended with a relay circuit in order to significantly extend the cycle rates when the heating load is low and to fully utilise the buffer volume. For this purpose, there are two thermostat switches at different heights on the buffer tank, which ensure a strong stratification build-up. Another rendeMIX multi-way mixer is used as a link between the CHP unit and the buffer storage. With an integrated fixed-value controller, it acts as a return flow booster for the CHP. This connects the three buffer feed points with the Dachs CHP unit and thus ensures stratified loading. Both in the boiler circuit and between the buffer and the distributor, the "two-zone principle" was thus applied with the mixing valves from HG Baunach. "This ensures that the spread in the buffer is always kept as high as possible. Only when the upper zone is fully charged is the lower part included in the charging process. This means that useful temperature is available more quickly at the top, and the lower zone remains cold for longer. This principle is particularly advantageous for the use of solar heat," explains Baunach. In a test set-up installed in the Arnsberg Chamber of Crafts, it was possible to determine through measurements that a buffer storage tank can release up to 35 % more heat energy if it is discharged according to the "two-zone principle". "After the modernisation, there is a defined temperature spread in our heating system, and at the same time there is a sufficient supply of standby heat. The combined heat and power plant has not stopped for a single minute since it was put back into operation, and both heat generators are constantly operating in the condensation range. With the optimisation of the system hydraulics, it was possible to achieve optimal utilisation of the condensing value and an efficient heat supply," summarises R+F sales manager Wolfgang Mika.
Functional principle of the multi-way mixer
The actuator of the rendeMIX connects only two of its three inputs to the single output, so that either hot water is mixed with warm water or warm water with cold water. In this way, as much available hot water as possible is used and only a little hot or cold is mixed in. This makes maximum use of the temperature available in the heating water network and reduces the return temperature to the heat generator. The actuator can be controlled by any weather-compensated controller (230 V, three-point signal) from the boiler accessories. Alternatively, an actuator with integrated fixed-value controller is available.
In the Heating hydraulics flows enormous Savings potential
Experience one year after hydraulic optimisation: Consumption values prove high energy cost reduction
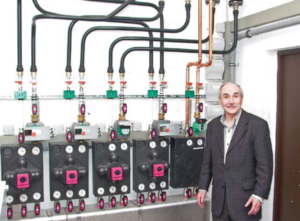
Fig. 6: "The CHP unit has been running without interruption since the hydraulic optimisation of the system," reports Norbert Rösner from the technical sales office at Richter + Frenzel in Schweinfurt. An additional savings effect was achieved by reducing the pump power consumption.
A year ago, in issue 5/2007, we reported on the energy optimisation of the heating system in the Schweinfurt branch of the SHK wholesaler Richter + Frenzel. The resulting energy savings can be quantified in four-digit euro amounts after one year of operation, as an evaluation of the consumption data has shown. According to information from the plant operator and the manufacturer HG Baunach, who played a major role in the hydraulic optimisation, the investment has paid for itself by about a quarter after one year.
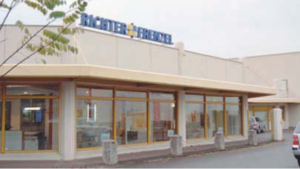
Fig. 7: The heating system in the Schweinfurt branch of the SHK wholesaler Richter + Frenzel was optimised at the end of 2006. For example, high return temperatures are used for the low-temperature circuits such as the underfloor heating in the bathroom exhibition.
For more than twelve months from the time of commissioning after the energy modernisation, the consumption values for gas and electricity in the Schweinfurt branch of the SHK wholesaler Richter + Frenzel were watched with excitement. The reason for this was the optimisation of the heating hydraulics, which had been completed towards the end of 2006. On the one hand, by using the return flow, it was to be achieved that the heat surpluses from the high-temperature circuits (air heaters, underfloor convectors) could be used for the underfloor heating systems in the showrooms and offices. Due to the high return temperatures, the high-temperature circuits (70/50 °C) still offered sufficient heat energy to supply the low-temperature heating circuits (40/30 °C). For the modernisation planning, the performance data and mass flows of the existing system were first recorded. A system calculation showed that there were large heat surpluses from the high-temperature circuits. Accordingly, the return temperatures for the heat generators were too high.
Return divided into two stages
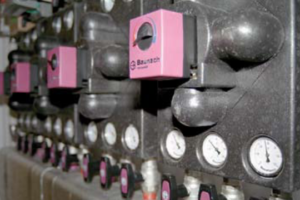
Fig. 8: The multi-way mixing valves rendeMIX from HG Baunach distribute the heating heat to the high and low temperature heating circuits. Return utilisation is in the direction of the lower temperature ranges. Together with the three-chamber distributor from Magra, low return temperatures are provided for CHP and condensing boilers.
The dual-fuel heat generation system consists of a small CHP unit from Senertec and a condensing medium boiler type MGK from Wolf Heiztechnik. For this duo, low return temperatures are a prerequisite for energy-efficient operation in order to achieve long running times for the CHP and continuous utilisation of the condensing value in the 130 kW medium boiler. "With the existing hydraulics, it was not possible to achieve low return temperatures and thus effective utilisation of the calorific value. Mixing the returns from the high- and low-temperature circuits would have resulted in lukewarm heating water," explains Hans-Georg Baunach, who had provided advisory support for the modernisation planning. Also, the prevailing operating conditions did not allow for efficient spreading in the existing buffer tank. The question, however, was how to implement the principle of return utilisation. This task was solved by a complete reconstruction of the heating water distribution with the multi-way mixing valves "rendeMIX" developed by HG Baunach and a special Magra distributor with an additional return chamber (detailed object report in IKZ-HAUSTECHNIK 5/2007, page 186 ff., "Heat is used several times instead of simply being heated").
Determination of energy cost savings based on comparison of the operating years 2007 / 2005
Explanations:
1 The energy optimisation of the system was completed at the end of 2006; 2007 was therefore the first year of operation after the modernisation. The calendar year 2005 was used for the cost comparison, since during the heating period the years 2005 and 2007 had more similar weather conditions than 2006 and 2007.
2 The reduction in gas consumption was achieved by
a) hydraulic balancing of the entire heating system (part of the heat was previously unused)
b) Replacement of the single-stage peak-load boiler with a modulating gas condensing boiler.
3 – 6The increased CHP running times and the resulting increase in CHP electricity production were achieved through the following measures:
I. Optimised buffer storage management through
a) Hydraulic balancing
b) Return flow utilisation through the use of multi-way mixing manifolds and three-chamber manifolds
c) Two-zone charging and discharging of the buffer tank by using a multi-way mixing manifold
II. integration of the peak load boiler in such a way that it feeds directly into the distribution network on the upstream side and not into the buffer storage tank
7 Gas consumption for heating = total gas consumption - CHP gas consumption for electricity production
8 Gas consumption boiler = gas consumption heating - CHP gas consumption for heat production
9 The increased CHP running times to cover the basic heating load reduced the running times of the gas condensing boiler used as the peak load boiler.
10 – 12 The increased CHP electricity production reduced the costs for electricity purchases.
13 – 16 The calculation is based on the energy prices of 2007.
17 Through the hydraulic optimisation of the entire system, the operating costs for gas and electricity could be reduced by 5,613.67 euros per year
Less gas consumption, but more electricity production
The fact that attention was paid to the electricity meter as well as the gas consumption is related to the installed small CHP unit, which covers both the basic heat load and produces electricity: If sufficiently low return temperatures are available, longer CHP unit running times and thus higher electricity production are achieved. The consumption values for gas and electricity, the operating times of the CHP and (peak-load) boiler, and the CHP electricity produced show the effects of the energy optimisation. Wolfgang Mika, sales manager at the Richter + Frenzel branch, puts the savings for the consumption year 2007 at a total of around 5,600 euros. "Since the recommissioning after the modernisation in November 2006, the CHP has been running continuously and the condensing boiler continuously discharges condensate. Defined system temperatures prevail in the entire system, and this with a minimum of technical control effort," says Wolfgang Mika about the result of the hydraulic optimisation. From the recorded comparative data for energy consumption and operating time (table), it can be seen how the energy utilisation in the plant system could be increased and thus the costs reduced. "The measures implemented to reduce energy costs had focused purely on the system hydraulics, with the exception of the replaced peak-load boiler. These included the hydraulic balancing of the system, the realisation of the return utilisation as well as the two-zone loading and unloading of the buffer storage tank. The combined heat and power plant now provides more than half of the heat production due to continuous operation; in addition, more electricity is generated in the process. The utilisation of the return flow and the efficient buffer management provide optimal operating conditions for the operation of the CHP unit and the condensing boiler," Hans-Georg Baunach summarises.