Skihalle Neuss - Many thousands of euros saved
Baunach Solution approaches for a typical refurbishment case
Patchwork is probably an appropriate term for a large number of technical building equipment systems in Germany.
Conversions and expansion measures, especially in the service and commercial sector, force a few more pipes and actuators to be added to the installation diagram. The already hydraulic labyrinth becomes even more confusing with the additions and the resistances in the network grow. The usual quick fix when something no longer gets warm is to increase the boiler output. Typical example: Neuss ski hall.
In many cases, however, there are actually enough energy reserves hidden in the installation to supply a planned extension, for example. And not only that. The disarray in the hydraulics as a result of the various measures or the lack of balancing permanently causes superfluous, expensive transport losses. Eliminating these in order to do good not only for the budget but also for the environment has been a well-known demand in the climate debate for years. For residential and non-residential buildings, KfW requires hydraulic balancing as a funding condition, but hardly anyone looks into the more complex system construction for service and commercial buildings. Most companies do not even know what they are giving away.
Thinking about energy TÜV
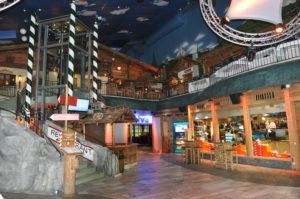
Picture 1: The trigger - the cold foyer.
This means that hundreds and even more megawatt hours are uselessly wasted in this area every day throughout Germany. Perhaps the public administration should think about a kind of energy MOT that at least draws up renovation roadmaps. Licensed planning offices could carry out this task. This would certainly help to get a bit closer to the federal government's CO2 targets. In Neuss, they are working in this direction, namely in the ski hall area, to bring the supply, demand and consumption of heat, cold, electricity and gas into balance. Those involved have worked out a two-stage concept. Stage 1 concentrates on low-investment measures, on correct hydraulic adjustment. Just a few interventions were enough to reduce the energy bill by several thousand euros a year.
Stage 2 will entail some investments, but these will also pay for themselves within a relatively short period of time. Admittedly, at first glance an "exotic" indoor ski slope does not necessarily sound like a blueprint for renovating the myriad of inefficient heating and air conditioning systems in this country. In fact, however, it is a typical case, because the original planning only referred, so to speak, to the first construction phase of what is now a spacious area with lecture rooms, with a hotel, with fun football, with a climbing park and more. To draw an analogy with the commercial sector: as elsewhere, new halls were added. And this is also true in general: in the course of the eighteen years of existence of the amusement park, which annually brings winter into summer for about 1 million visitors, among other things, planners and installation companies changed. Thus, despite documentation, know-how was lost.
The complaint
Let's stay with stage 1 first. About two years ago, the house technicians of the artificial ski slope had to call the company Haaß Sanitär Heizung Haustechnik from Mönchengladbach. The boiler system was unable to sufficiently temper the gate air curtain in the entrance area. The warm air curtain requires an output of about 20 to 25 kW to screen the foyer from the outside air. The Haaß company, which was not involved in the previous new building, asked itself why an 800 kW heat generation system, consisting of two 400 kW condensing boilers (Viessmann), each with a two-stage burner, could not manage this? The two-stage cascade is also supported by a 250 kW boiler, which was originally only used to supply the hotel (heating and hot water). In the meantime, however, the hot water supply had been switched over to the large boilers so that the 250 kW unit could be switched off completely in summer when it was not needed to heat the newly added hotel. The restructuring of the network in the meantime included even more changes in the installation and equipment. "But unfortunately, none of the previous companies dealt with readjusting the heating water transport accordingly. With the result that the exchanger of the air curtain system at the end of one of the strings no longer received enough hot water.
The situation
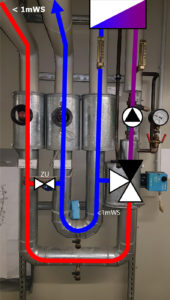
Figure 1: Supply to one of the three air handling units. The main pump drags most of the flow water directly into the return via the open bypass and raises it
The installation scheme found with a main pump, mixer and heating circuit pump is called "Admixing circuit with main pump and pressureless manifold: Multiple heating groups". In the Neuss ski hall, the "pressureless" manifold is replaced by a manifold limited to 1 m water column - a pre-pressure (differential pressure control of the electronically controlled circulating pump at the smallest setpoint) that does not disturb the control characteristic of the three-way mixers too much.
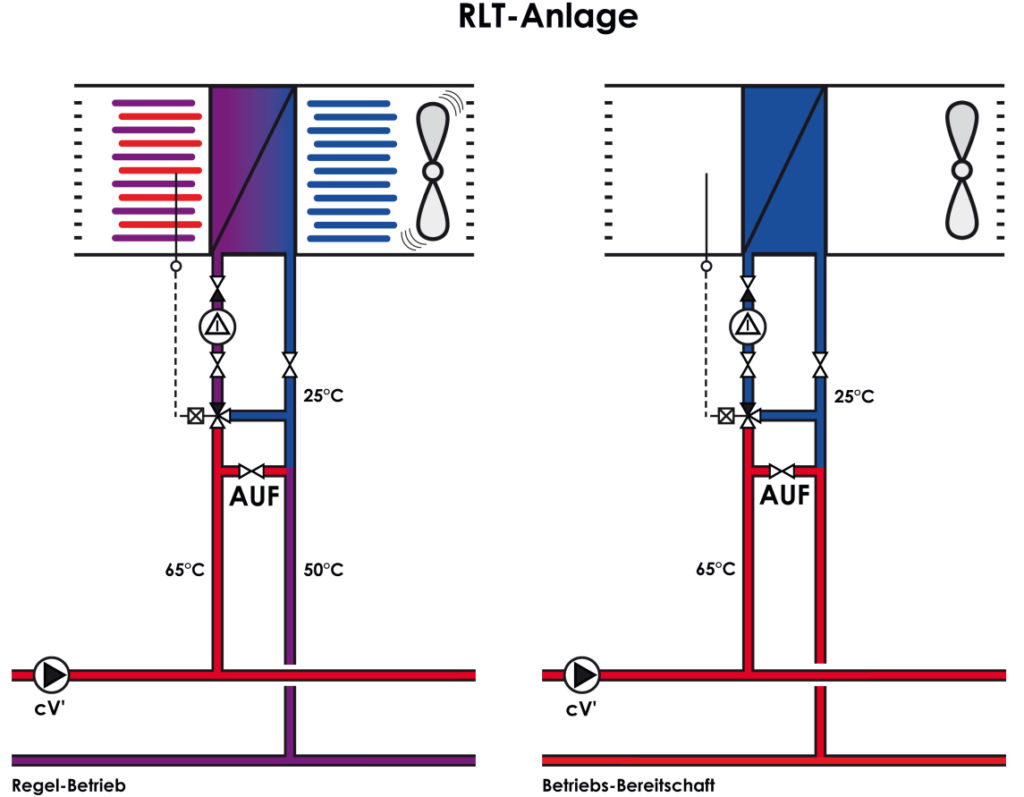
Fig. 2: When the bypass is open, heating water circulates permanently even when the air handling unit is not in operation.
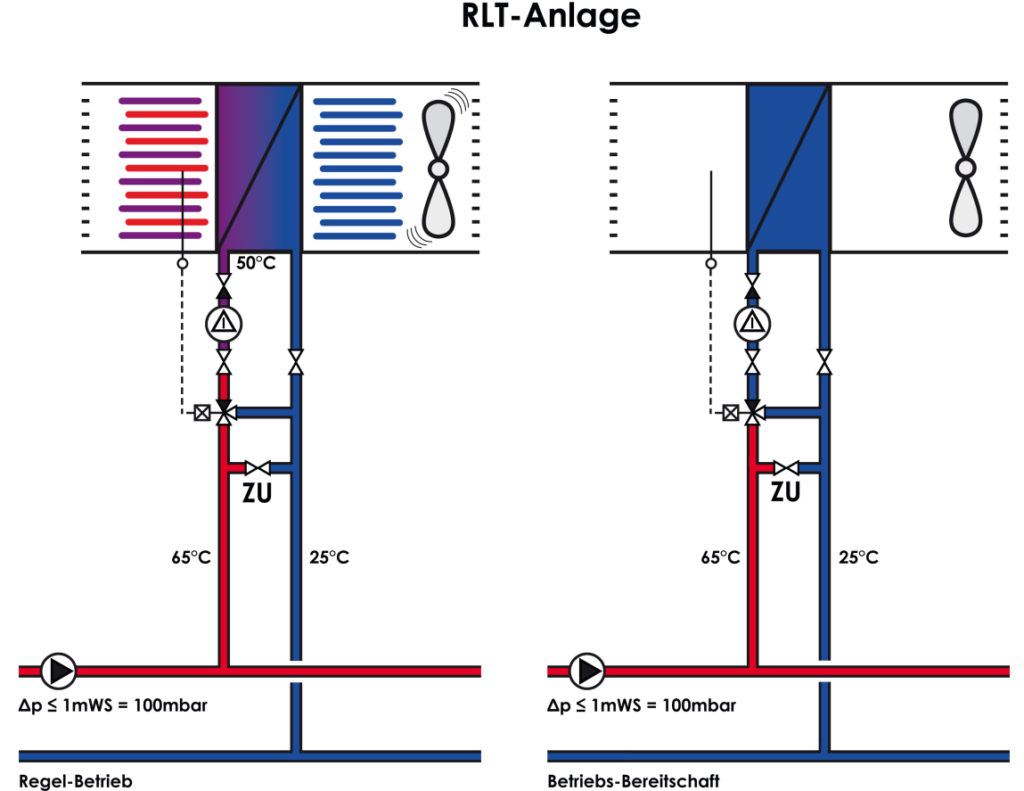
Figure 3: Closed bypass.
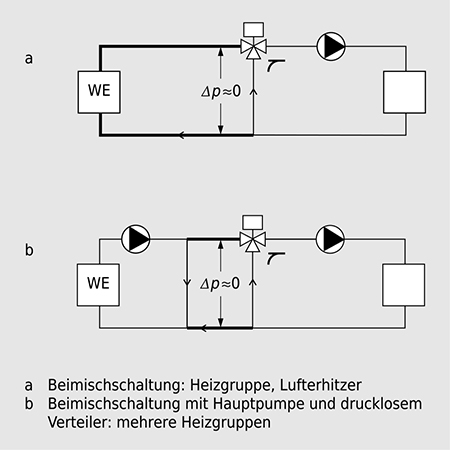
Figure 4: The decisive statement in the ETH Zurich publication is that in the case of a mixing circuit, there must be virtually no upstream pressure at the mixer. Source: Source: www.vdf-online.ch/post/32-hydraulische-schal-tungen
"The foyer cooled down," says plant engineer Georg Haaß, describing the condition he found. He passed the problem on to the company HG Baunach in neighbouring Hückelhoven. Company boss Hans-Georg Baunach, who studied electrical engineering at the RWTH Aachen, had already assisted the craftsman's company with some tricky renovation jobs in the past. His company specialises in hydraulic measures, both in the form of advice and with its own products for network balancing: almost twenty years ago, it had developed Baunach's rendeMIX fitting and launched it on the market. This is a multi-way mixer which, with its internal bypass section, is capable of balancing different mass flows and thus directing the return of a high-temperature circuit as a flow into a low-temperature circuit. In many single-family houses there are radiators in the children's rooms and bedrooms upstairs, while under the screed in the living room on the ground floor there are coils of underfloor heating. Both systems work with different water volumes, so they are usually designed as independent circuits, each with its own pump, and in the case of wall-mounted units usually in conjunction with a hydraulic separator. However, this investment is only one of the disadvantages of the parallel connection.
The trick with the return temperature
The second is the weakening of energy efficiency due to the high return temperature of over 40 °C from the high-temperature circuit. This boycotts the condensing principle. Designs of this type do not fulfil their promise to condense the latent heat in the flue gas. They thus give away 10 to 15 percent of the yield that a return temperature of 25 or 30 °C gains. Poor condensation also leads to deposits and corrosion on the condensing heat exchanger, resulting in high maintenance costs and premature failure. The Rendemix fitting, on the other hand, networks the radiators and the floor coils into a single circuit, with the boiler pump taking over the supply to the radiators. Since it only directs the cool low-temperature return into the condensing heat exchanger, it guarantees the promised savings effect. The latest innovation from Baunach bears the not entirely meaningful designation return temperature limiter or RTB valve. This sounds like a relatively static component.
In fact, however, it is a dynamically reacting thermostatic valve for the return installation that permanently regulates the flow to a preset water temperature: If the return is too hot, it narrows the cross-section because obviously the radiators do not need the current flow rate due to too high temperatures in the rooms. If the return temperature drops above the set spread, more heating water must circulate - the sensor-controlled RTB increases the valve opening. A defined minimum circulation ensures that blockages due to the ambient temperature do not occur. The fitting automatically takes care of the hydraulic balancing and has the blessing of KfW. In the case of modernisation measures, the KfW stipulates as a condition for subsidies that the flow be adapted to the demand within the framework of hydraulic balancing. For hydraulics specialist Hans-Georg Baunach, an incorrect pump or valve setting was obvious in the Neuss ski hall. It was inconceivable to him that there should be no more heat for the warm air curtain in the available around 1,000 kW, even if the water had to meander through some winding pipework by then.
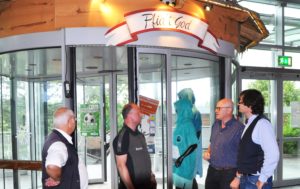
Figure 2: Discussion under the air curtain system: Siegfried Gehler, Haaß Haustechnik (from left); Armin Schrills, Haustechnik Skihalle Neuss; Georg Haaß, Haaß Haustechnik; Hans-Georg Baunach, HG Baunach GmbH & Co. KG (from right).
Increasing the boiler output was the first solution discussed. The only bottleneck was the DN 80 natural gas pipeline, which is fully loaded with the boilers already installed. However, the technical department of the ski hall was sceptical about an additional or new, larger heat generator. The few kilowatts for the foyer could not actually stretch the cascade beyond its limit.
Water circulation without heat transport
The experts ran the strands where feasible. The central installations are distributed over several technical rooms. The main distributor is in one of them and the DN 65 main pump is in the other. It supplies three air conditioning systems: in the ski hall, in the catering area and in the kitchen, all three with their own mixer and pump and upstream bypass valve with the settings 1 to 10. The engineers noticed a relatively low spread. "This indicated a hydraulic waste, that the main pump circulates water masses that do not transport heat - 60/55 °C on a cold day, that was not acceptable," Hans-Georg Baunach looks back. Admittedly, he also lacked a spontaneous explanation for this. Until the hydraulics specialist, more on a trial basis than recognising it, turned off the bypass valves in front of the three mixers for the three air-handling units a few rooms away and at the same time set the main pump to the lowest possible constant differential pressure (1 m WS). Only to be surprised to find that the bypasses between the supply and return lines were completely open. "Unfortunately, this hydraulic waste is almost regularly hidden in larger, cluttered installations. How do you expect to discover them? As long as everything gets warm, no one complains. Here in Neuss, they only called us because the foyer was cooling down and not because of a consumption that made them wonder." The "repair" cost the investment of a single morning's work.
Of course, the complication lay in the basic problem of many heaters, the hydraulics. The following was not true or no longer true: the bypass dates from the time of the circulating pumps with constant output that were installed in the past. It had to reduce the upstream pressure at the mixers in order to bring the pressure difference and the characteristic curve into line. It was state of the art 20 years ago. Today's centrifugal pumps with differential pressure-dependent performance, however, make it superfluous. In the case of the Neuss ski hall, it led to the main pump supplying 4 or 5 m3/h of heating water, the circulating pumps of the three AHU systems taking their heat requirement from this and the large remainder of 3 or 4 m3/h going directly back into the return without transporting heat, raising its temperature to high and thus flowing back to the boiler.
20,000 euros for a morning
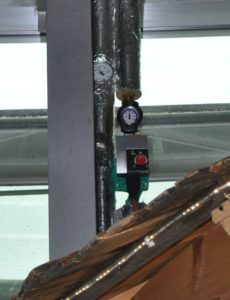
Figure 3: The new pump brings up the volume.
The gate air curtain system at the end of the network, which did not have its own suction pump, had to make do with what still got through to it. This amounted to only a fraction of the required 20 kW. Neither the volume nor the temperature was sufficient. Because of the circulating water masses, the boiler could not manage a flow temperature higher than about 60 °C. Its output disappeared mainly in the water. Its output disappeared mainly in the acceleration of the water mass Q circulating pointlessly through the bypasses, while the heat exchangers of the hot-air curtain wanted to be controlled at 70 °C. Haaß and Baunach therefore closed the equalising sections and reduced the differential pressure at the main pump from 5 m WS to quasi-pressureless (1 m WS). They thus transferred the air-handling units' volume flow control to their own mixer pumps.
As expected, the spread climbed from 60/55 °C to 70/45 °C after a short time. With this first effect, the TGA fulfilled one of the conditions for a functioning warm air curtain. However, there was still a lack of volume due to the reduced upstream pressure. The building technicians therefore screwed an additional suction pump into the heating pipe to the ski hall entrance. Since then, the air curtain system has been working without any complaints. But that doesn't even cover the most important aspects of stage 1. Keyword hydraulic waste - five months after the intervention, the technical department reported: "The curtain shields the entrance area from the outside air without any impairment. But now, in retrospect, this is almost just a side effect. According to our data collection, we save natural gas with the new Hydraulik 20 %". This reduction should add up to 20,000 to 25,000 euros for a purchase of 2.7 million kWh per year and 4 ct/kWh: With the adjustment, Baunach and Haaß had not only covered the heat demand of the warm air curtain, they had also sustainably optimised the network operation overall.
With a few flicks of the wrist. Admittedly, the figures are not weather-adjusted, but they apply to identical periods in the years of comparison. They are also in line with the results of an extensive project a few years ago involving the Wolfenbüttel University of Applied Sciences and the Research Group for Practical Vocational Training at the University of Bremen, which merely put the hydraulics in order in around 100 residential buildings and compared consumption before/after: there, too, heating costs fell by an average of 20 %.
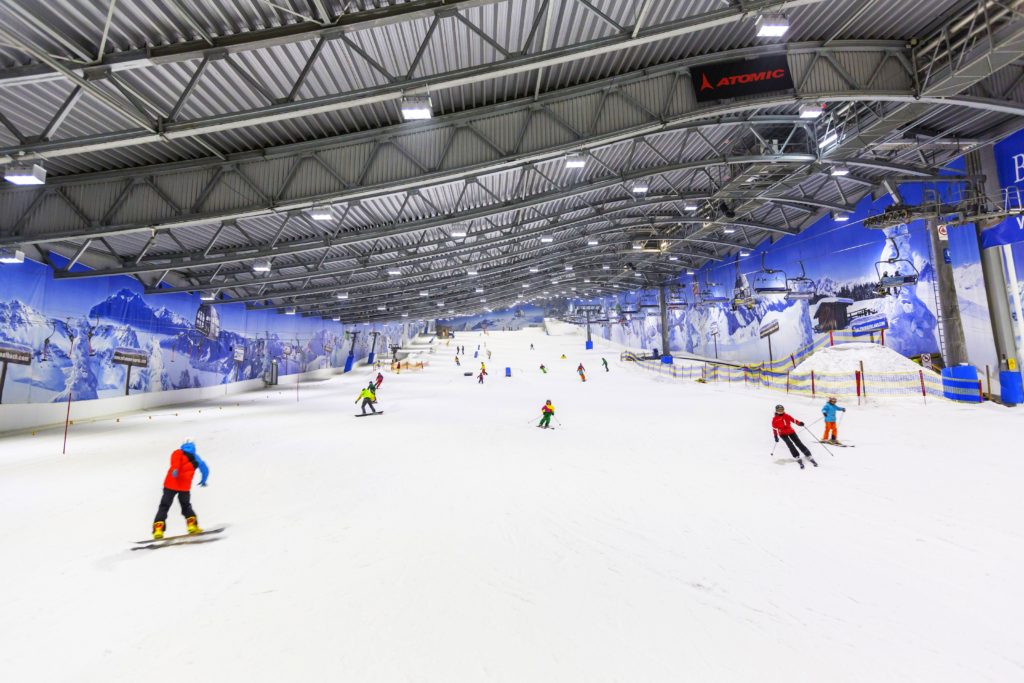
Figure 4: The snow cover offers itself as a cold reservoir
Restoration stage 2
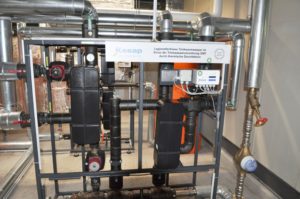
Figure 5: Hot water preparation.
In the Neuss plant, however, there is another enormous savings potential beyond the (switched off) losses of the hydraulics. This is where Etanomics Service GmbH comes into play. This second part of the description of the conditions in the Neuss ski hall contains, as renovation stage 2, the actual suggestion for planners, plant constructors and, above all, for the operators of larger objects, not to close their minds to a service called "composite test" for new buildings as well as for modernisation and renovation. In principle, this is nothing more than the monitoring of commissioning through the eyes of the client, i.e. through the eyes of the building owner or a far-sighted planning office.
This is how Etanomics proceeds...
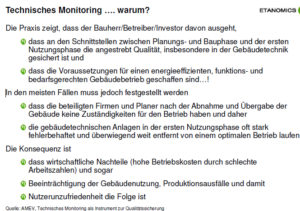
Why monitoring?
Thomas Maintz explains: "Let's take a sample object. It is a new construction project for the production of optical equipment under cleanroom conditions. What does the specialist engineer do? He works through the service phases according to HOAI, with cost estimation, with specifications, with MSR tendering, and in principle has to think through all the functions. But as a rule he often doesn't know exactly what energy will be needed later: Manufacturing measuring instruments under clean-room conditions - how much heat and cold will be needed? The design is not based on more than a theoretical estimate. So we offer a supplement to the HOAI. We look at similar production sites, record the media flows there, superimpose them with the planning and correct them if necessary due to possible deviations.
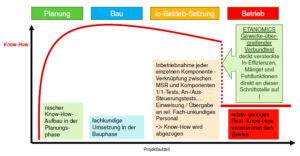
Advantage composite test
In the phase before and during commissioning, some things can still be changed. Later, everything becomes very expensive. We create such balances with our analyses and with our compound test we check the correct implementation of the planning." Thomas Maintz shakes his head when he talks about his experience with CHPs. "Who thinks about determining the bivalence point, when the second heat generator, the boiler, should start up. Who sizes the storage tanks correctly so that stratification remains undisturbed at all operating points?
This February, we had to deal with CHPs that either did not run or were permanently cycling. Our work includes investigating such hydraulic problems or eliminating them from the outset. This includes, as a small but not insignificant detail, that the inlet velocity in the stratified storage tanks must not exceed 0.1 m/sec. A higher velocity breaks up the stratification. If the water mixes, the capacity of the storage tank is halved or reduced even further. This means that the volume flow must be throttled accordingly. Otherwise the CHP gets nothing to do. We look at every implausibility in the operation of heat and cold generators as soon as their clarification is expected to bring efficiency benefits and energy cost reductions."
The only difference is that these eyes concentrate on conditions and processes that the planning did not have in mind or that were not yet known as influencing factors during the design.
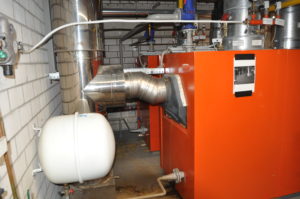
Figure 6: Space for condensation heat exchanger would be available.
Not to leave this sentence so nebulous: Who the energy supplier will be later on is not necessarily known in the planning phase. Nor do we know what the energy supply and demand will look like in real terms over the course of the day. One will orientate oneself on a usual load curve, but not on the possibly deviating conditions of a specific object. For example, a regional energy supplier that primarily serves office and administrative customers might demand a high tariff during the day and atypically a low tariff in the evening hours. Consequently, the I&C and the installation technology should fill the storage tanks in the evening, i.e. shift that part of the load profiles that can be shifted to times after office hours here. This does not save energy - the point on which the planning had placed emphasis - but it does save money, which interests the client's business people even more.
Time as a product
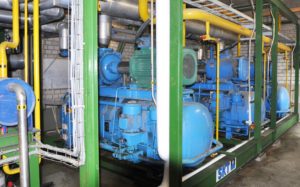
Figure 7: 450 kW cooling from the refrigeration compressors.
Baunach had already consulted the experts at Etanomics in previous projects. Their know-how is based on experience with a large number of major projects. "When we are called in, we usually always find something that can be optimised. First and foremost, we focus on operations that cost little, that is, that do not require a technical investment. The first step is what we call an 'energy compass'. Among other things, we ask the client to provide us with data (load profiles) that are easily made available by the energy supplier, and we convert them into a load profile analysis. From the results of this analysis, we derive recommended measures, but also questions that await answers. Then we invite the parties involved to a workshop at the plant operator's, discuss the individual complexes and summarise the result into a prioritised to-do list of the tenor. "First you should take those measures that do not require any significant investment, then those that require conversions," is how Thomas Maintz, one of the consulting engineers at Etanomics Service GmbH, describes the "energy compass" model (see box "This is how Etanomics proceeds ...").
The Neuss complex, like many other properties, is very electricity-intensive. For the energy experts, the focus in such cases is therefore on saving electricity (costs). In order to create the necessary transparency, they install measurement technology for an appropriate period of time, record the load profiles of the machines and consumers and determine the extent to which load shifts are possible on the basis of the load profiles on site. In the indoor ski slope, it is necessary to look at the individual refrigeration compressors individually in order to determine the power peak and against the backdrop of the concession for "atypical network use", thus recording the running times and switch-on points with the intention of working out a schedule that, for example, reduces parallel operation to a minimum. An energy and load management system. The almost 0.5 m thick layer of snow acts as a huge cold reservoir. Balancing the control cycles and equalising the individual operating times certainly conceals an immense peak reduction potential. Etanomics does not want to give a rough estimate of the amount. It would only be possible to say more after a workshop with staff from the technical and administrative departments, because the exact operating procedures and their priorities would have to be known - and this workshop is part of the second package of the "Energy Compass". But it should be more than 10,000 euros.
Parallel case DTTZ Düsseldorf
When, after several supplementary measures in the German Table Tennis Centre DTTZ in Düsseldorf, a new ventilation and air conditioning system was finally added in the TGA, the additional 120 kW charged seemed to exceed the power reserve of the existing boiler system. As a first emergency solution, a larger storage tank instead of the installed 1,500-litre tank could have flattened the peak output and thus covered at least part of the increase, but there was no space for this in the already overcrowded technical room.
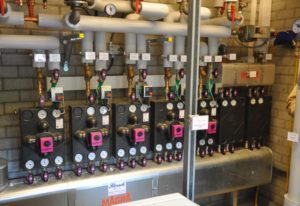
rendeMIX mixer in the DTTZ
For the time being, the heat generator had no choice but to distribute a deficiency. Hans-Georg Baunach and the planning office IAS Halbrügge therefore looked at the hydraulics and discovered a potential that reduced the consumption and the demanded output by 30 % and thus made an increase in the boiler plant unnecessary. Firstly, with the help of the Rendemix mixers, they took the return flow of the radiant panels in the hall with a temperature of more than 45 °C directly to the flow of different low-temperature circuits. Secondly, with the support of this type of mixer, they retrofitted the storage tank with two-zone charging and discharging - thus doubling its capacity. "With dual-zone charging and discharging, we first extract the hot water from the middle for a large number of the consumers before accessing and cooling the valuable hot water from the upper buffer zone. This means that the strands of the high-temperature circuit also make their return flow available to the middle connections as a flow. The usable capacity of the buffer has exactly doubled as a result," Hans-Georg Baunach explains the success of the measure.
Load management recommended
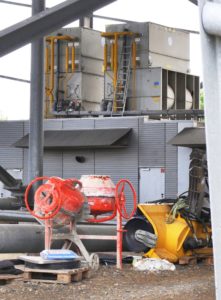
Figure 8: Waste heat disposal via cooling towers.
Load management bears fruit in two ways. First, it breaks the peak and thus the provision fees for the ordered load of electricity and gas (see box "Expensive peaks and times"). Secondly - and here the cold-storing snow layer could be decisive - the analysis or the adapted energy management, as just mentioned, opens up the possibility of claiming a reduced grid usage charge under certain circumstances. This is the case if it is possible not only to reduce the peak, but also to take part of the consumption out of the high-load period and shift it to off-peak periods. The grid charge for providing and transporting electricity accounts for about 25 % of electricity costs.
However, according to § 19 of the Electricity Grid Charges Ordinance (StromNEV), certain end consumers are entitled to receive lower individual grid usage charges from the local grid operator. For example, in the case of "atypical grid use". This exists if the peak load at high load times in the low-voltage range is at least 30 % and in the medium-voltage range 20 % below the peak load at off-peak times. Thus: 1,000 kW usually, but only 700 or 800 kW at high-load times. The corresponding time windows are to be published by the grid operator for his supply area. Google the term "atypical grid use" and the company name of the grid operator. The privileged use is justified by the fact that these customers cushion the provision of electricity due to their special consumption behaviour and thus make an individual contribution to reducing or avoiding grid costs. Westnetz GmbH is the network operator of the Neuss ski hall. The grid usage fee is approx. 80 euros/kW and year. If it is possible to get by with 20 % less electricity at certain times than at maximum consumption at off-peak times, several €1,000 can be saved.
Expensive times and peaks
Where in the electricity tariff is the grid charge/provision costs hidden? As you know, the electricity price of the energy supplier is made up of a share for the actual amount of electricity purchased (energy price) and a flat rate (basic price). The basic price again consists of several items. In addition to state-determined taxes and administrative costs, the "performance price" is a variable component. This demand charge includes the grid utilisation fees. These, in turn, depend on the annual peak demand, i.e. the absolute consumption peak, as well as the voltage (low voltage, medium voltage). Who records the peak? The metering point operator, if the business consumes more than 100,000 kilowatt hours (kWh) of electricity per year. From this value onwards, he measures the electricity consumption every 15 minutes via a remotely readable electricity meter (recording power measurement, or RLM for short). The individual measured values result in the load profile, i.e. the customer's consumption behaviour over time.
The one quarter of an hour a year with the highest electricity consumption therefore determines the grid fee. If you get by with a maximum of 800 kW for 8,759 hours a year, but unfortunately have a single demand of 870 kW for 20 minutes in the 8,760th hour, you will pay 80,000 euros for the 800 kW in 8,759 hours and 40 minutes, assuming 100 euros/kW supply - plus 7,000 euros for 20 minutes of 70 kW. Plus the additional perhaps five euros consumption costs for the 20 minutes. In Neuss, the utility Westnetz GmbH charges around 80 euros/kW grid fee. An unintentional outlier of plus 100 kW in a single quarter of an hour on the average 1,200 kW provided per year thus already costs the ski hall 8,000 euros. It is worth taking a closer look and thinking about load management or at least load shedding.
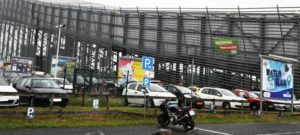
Figure 9: The elevated steel construction flows into a concrete slab with subfreeze protection at floor level. The boiler's heating water is responsible for this. The better alternative here is waste heat utilisation.
Wasted waste heat in the Neuss ski hall
However, the far greater untapped treasure is hidden in a separate room made of sheet steel under the ski slope structure. Energy expert Maintz puts the diagram from the Neuss ski hall on the table. On the electricity side, their three 150 kW chillers plus the other small and large consumers in the area permanently draw an average of 750 kW. On the gas side, consumption fluctuated between a maximum of just under 1,000 kW in February 2016 and a minimum of 100 kW in July 2016. "The relatively constant load curve for electricity with occasional strong fluctuations during the course of the day can be explained by the permanent demand of the refrigeration compressors for the snow layer. Apart from slightly higher consumption at high outside temperatures, this is hardly affected by the weather. The fluctuations in heating gas consumption are of course explained by the influence of the weather. But what is striking is why there is a relatively high gas consumption at all, when the refrigeration compressors with their 450 kW of electrical power provide around 1,000 kW of waste heat. What happens with this waste heat? Nothing!
The compressors throw away huge amounts of (waste) heat by heating the outside air via two evaporative cooling plants. Yet a local heating pipeline could transport the heating energy to a large number of low-temperature consumers and probably save 80 per cent gas consumption." And he continues: "But even if we only used part of the waste heat to heat water via fresh water stations for kitchens and sanitary facilities instead of via boilers and storage tanks, the annual bill still includes 2,700 MWh of natural gas for heating and hot water. If we assume 15 % for showers and taps, ergo 400,000 kWh or 16,000 to 20,000 euros, a partial conversion should have paid for itself after a few years. Or possibly a condensing heat exchanger behind the boilers - as I said, we are talking about 2.7 million kWh of natural gas and 800 to 1,000 kW of waste heat. Some of that will certainly be worthwhile." Local heating networks only cost money at first glance. Considerable subsidies can be found through Bafa or KfW if a coherent concept is created.
The better solution
But the experts believe even more in the economic viability of the big solution: converting the entire distribution system to use return flow, integrating a heat feed from the refrigeration plant and imposing load management on the whole thing. That has to pay off. In this way, a reserve could be created that would be more than sufficient for the planned extensions to the leisure centre. Both Thomas Maintz and Hans-Georg Baunach point out that the Neuss indoor ski centre is not an isolated case. "It is rather typical for a multitude of inefficient facilities of which the operators do not even know how much money they waste senselessly on a daily, monthly and yearly basis".