The better log firing system
More user comfort with multi-way mixers - oil tank to stratified storage tank
Sustainability of the triple kind: Michael Schmitz, owner of the Company Sanitär M. SchmitzRemagen, cut up a superfluous oil tank, welded it back together elsewhere in the boiler room and coupled it to the log boiler for its new function as a buffer storage tank. Firstly, he saved valuable resources. Furthermore, he installed two multi-way mixing devices between the buffer and the heat generator, which allow the tank to be operated as a pressureless stratified storage tank. Secondly, this saves the operators energy, and thirdly, the two-zone loading and unloading offers them a high degree of charging comfort. They no longer have to go to the boiler room every day.

Fig. 1: With hardwood combustion, the kilowatt hour of heat costs about 3.7 cents on average. Oil as a fuel costs at least 50 per cent more. Michael Schmitz from the company Sanitär M. Schmitz, Bonn, therefore recommended this modern biomass heating system to his customers.
The three-family house in Alfter near Bonn with 400 m2 The living space is shared by three owners. When the community of three took over the building from the 1950s, it still corresponded to the state of the art in construction and heating technology at the time - that means poor insulation and an oil-fired high-temperature boiler. In a first step, the new owners therefore packed the building with 14-centimetre-thick polystyrene insulation, also insulated the floor slab and re-roofed it with a 12-centimetre-thick PUR underlay.
In the air raid shelter
It was agreed to renovate the core of the dwelling to make it more energy efficient. This meant nothing other than replacing the oil boiler with an ecological version. The property had previously belonged to a senior federal employee. He or the state had an air-raid shelter built into the basement. In addition to the other storage rooms. The bunker, however, has been misused by the residents for more current purposes since prehistoric times, so there was plenty of space for a log store.
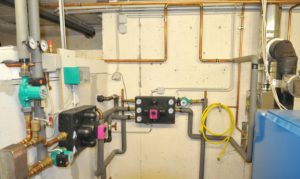
Fig. 2: Multi-way mixer (black) for loading and unloading the stratified buffer (left). The plate heat exchanger (far left) separates the open storage tank from the heating system. The standard circulation pumps were later replaced by efficiency pumps. (All photos were taken shortly after the conversion. The insulation of the pipes is still to come.
Because heating engineer Michael Schmitz recommended exactly that, namely a wood carburettor boiler with a large filling chamber for long combustion times and thus a relatively convenient feed that could be shared by the three residential parties. The "Logano S 151" from Buderus with 25 kW heating output met the requirements exactly. According to the brochure, it is characterised by a good efficiency of 86 percent and low-emission burner technology with flue gas recirculation.
However, the convenient charging with half-metre logs only really becomes noticeable with sufficient heating water buffer volume. 1,000 or 2,000 litres are not enough to bridge a weekend holiday. Michael Schmitz calculated 5,000 litres, which would allow the house to be left alone for a whole week during the transitional period. With a usable delta T of 50 K - between 90 and 40 °C - almost 300 kilowatt hours are available. This guarantees the basic temperature in the living rooms during the holiday week. Provided that the control technology is stingy with every calorie.
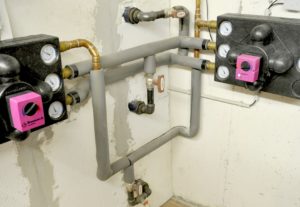
Fig. 3: Loading and unloading of the 5,000-litre buffer via the two rendeMIX multi-way mixers. For details, see box "Circuit diagram".
Oil tank as unpressurised buffer tank
The old oil tank provided the 5,000 litres. The plumbers dismantled it using a cutting torch, cleaned it, reassembled it in the boiler room, insulated it with external insulation and separated the buffer - since it is operated openly and thus absorbs oxygen - from the heating circuits with a corrosion-inhibiting plate heat exchanger. However, the heat exchanger primarily has another task: It intercepts the static pressure in the 10 m high building in front of the storage tank. The at least 1 bar would probably have dangerously bulged the tank.
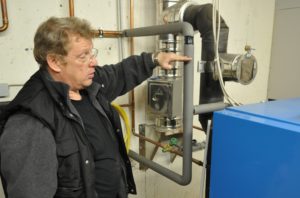
Fig. 4: As a lyre arch, this safety loop continued at the back of the wall (see picture below left). It dips into the tank. The boiler water can expand to about hand height Michael Schmitz. The lyra arch is to prevent back-siphoning.
That sounds like a lot of effort. According to Schmitz, however, this conversion did not cost as much as a buffer battery would have, especially since the tank was not to remain in the house but was to be disposed of. The dismantling costs would have been incurred in any case. Schmitz calculated that welding and insulating the tank together would cost "at least 2,000 euros less than installing a new 5,000-litre buffer. And that would have consisted of several tanks. Connecting them so that the water could stratify would have been a problem. We insulated the sheet metal with the insulation bricks left over from the façade insulation. From that point of view, we didn't even have to spend anything on thermal protection."
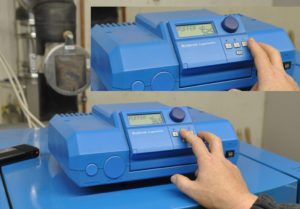
Fig. 5: The 5,000-litre buffer is constructed as a stratified storage tank. The loading and unloading is distributed over three zones. At the time the picture was taken in mid-November 2009, the temperature near the floor (cold) was about 25 °C, in the lower warm zone 36.5 °C and in the upper warm zone 52.5 °C.
The owners left the existing high-temperature cast-iron radiators in the rooms. Due to the insulation of the house, however, the heating system runs in low-temperature mode, at a maximum of 70/50 °C instead of the former 90/70 °C. The heating surface is more than sufficient for heating the rooms. The heating surface of the generously dimensioned cast iron fins is more than sufficient to transfer heat to the rooms.
High temperatures prescribed
The buffer tank, on the other hand, needed special hydraulics due to the recently possible economical flow temperatures. The system does not want to give away any temperatures, i.e. it does not want to have to permanently mix hot boiler water down to heating water that may be 35 or 45 degrees depending on the weather. In addition, it must ensure a high boiler water return temperature for reasons of rotting risk: The boiler circuit temperature of maximum 95 °C must not drop below 65 °C return. The aforementioned temperatures are part of the warranty conditions and "must be ensured by a suitable circuit and boiler circuit control", requires the "Logano S 151 wood carburettor boiler planning aid".
Circuit diagram Weidenstraße 7, Alfter
In the Alfter property, two technologies are combined, namely the two-zone principle for loading and unloading via the two rendeMIX units as well as a system separation between the heating circuits and the storage tank (heat exchanger ST on the far right). The decoupling had to be because the former heating oil tank cannot be loaded with the additional static system pressure of approx. 1 bar. The multi-way mixer assembly on the left, the one on the "Logano" solid fuel boiler, provides the two-zone charging, the one on the right towards the radiators or separating exchanger provides the two-zone discharging. The two zones in the buffer are located between the upper (85 °C) and the middle (45 °C) connection and between the middle and the lower connection (30 °C). Outside the full load period, this 5-m3-buffer is the actual heat generator in relation to the radiators and in relation to the control. The wood boiler then only supplies a relatively constant high temperature of 85 °C for a few hours in daily, two-day or three-day cycles. The basic idea is now to mix away as little as possible of the high-quality 85 °C to a lower temperature for the heating circuits during partial load operation. Irreversible mixing away, i.e. no longer reversible. 5,000 litres of 50-grain water have a higher heat content than 1,000 litres of 85-grain water, but in the first case the boiler would still have to reheat if the flow requires 65 °C. In the second case it could perhaps spend a day heating the boiler. In the second case, it could perhaps remain switched off for a day longer, depending on the necessary partial load. This means that a zone loading and unloading of the storage tank via a multi-way mixer together with the corresponding connection configuration circumvents the weakness of the conventional three-way mixer. If the outside temperatures only require a spread of, for example, 40/35 °C, only the former oil tank does the heating work: the right-hand rendeMIX picks up, for example, 45 °C (centre of the storage tank) and tempers it via the flow control to the heat exchanger to the exact radiator flow temperature. The 85 °C initially remains untouched. If the mean temperature falls below the set flow temperature, the control automatically switches to the upper draw-off based on the temperature measurements. When the "Logano" finally starts up, it merely reheats hot water from the middle connection to the value set on the fixed value controller and pushes it into the flats. This ramp-up is done quickly because of the relatively high initial temperature, so that the remaining logs in the combustion chamber serve to fill the storage tank completely again. The control system also decides independently how to ensure the 60 °C for the boiler return. If the middle zone has built up to 70 °C, for example, it uses the middle and lower connections. The rendeMIX only ever mixes hot with warm or warm with cold. This sounds like a complicated installation, but it is not. The multi-way mixer only needs one more line between the loading and unloading station. Otherwise, the control system remains conventional: a three-point controller with a flow or return sensor, with a weather sensor for unloading and a fixed-value controller for loading. This is sufficient to keep the stratification stable and not to give away any of the stored useful heat factor. The company HG Baunach GmbH & Co. KG, Hückelhoven, developer of the rendeMIX patent, is of course on hand to help with the planning. It creates the installation scheme. Success is thus guaranteed: maximum utilisation of the stored temperatures in favour of an extremely stretched loading cycle. Left: rendeMIX 2×3 RR 5 FWR = 2 connections to the heat source (wood boiler), 3 connections to the heat sink (heating circuits, storage tank), RR right-rotating (connections), 5 with pump flange, FWR fixed-value controller for setting the setpoint temperature boiler return integrated in the actuator. Right: rendeMIX 3×2 RR 5-sys = 3 connections to the heat source, 2 connections to the heat sink, sys = optimum flow control for low return temperatures before system separation. What is the difference between the type for system separation (with the suffix sys, right-hand assembly) and the usual rendeMIX? Let's take the storage temperatures of 85 and 45 °C, which the assembly mixes to the flow of 70 °C at full load. At, say, partial load 25 % on the other hand - in the radiator circuit this would be 33 °C flow and 28 °C return - the "sys" does not reduce the 45 °C supplied by the storage tank to 33 °C with the help of the return, but it directs the 45 °C directly into the heat exchanger. However, it reduces the quantity and thus the heat output. While the normal rendeMIX basically works like two three-way mixers in one housing, i.e. it mixes hot with warm and warm with cold, the "sys" version corresponds to a three-way mixer plus a two-way valve with the tasks of mixing and throttling. The energetic advantage, as indicated, comes into play primarily in partial load operation, when the buffer takes over the role of the heat generator. What does this advantage look like? Let's stay with the example of partial load 25 %. The storage temperature of 45 °C is sufficient as the heat source, related to the spread on the secondary side of 33/28 °C. The storage temperature is cooled in the exchanger. The 45 °C cool down to 30 °C in the exchanger. Delta T is therefore 15 K on the primary side. This means that because of the large delta T and thus the large heat utilisation, the mixer has to take 60 litres of 45-gram storage water from the buffer for one kilowatt hour of heating output, which it returns at a "cold" 30 °C. This is exactly the amount of water that would have to be taken from the buffer. The "sys" model would throttle the primary-side circulation to exactly these specific 60 litres (60 x 15 K = 900 kcal = approx. 1 kWh). The theoretical alternative: the return of the secondary flow and 28 °C return - the "sys" does not reduce the 45 °C supplied by the storage tank to 33 °C with the help of the return, but it directs the 45 °C directly into the heat exchanger. However, it reduces the quantity and thus the heat output. While the normal rendeMIX basically works like two three-way mixers in one housing, i.e. it mixes hot with warm and warm with cold, the "sys" version corresponds to a three-way mixer plus a two-way valve with the tasks of mixing and throttling. The energetic advantage, as indicated, comes into play primarily in part-load operation, when the buffer takes over the role of the heat generator. What does this advantage look like? Let's stay with the example of partial load 25 %. The storage temperature of 45 °C is sufficient as the heat source, related to the spread on the secondary side of 33/28 °C. The storage temperature is cooled in the exchanger. The 45 °C cool down to 30 °C in the exchanger. Delta T is therefore 15 K on the primary side. This means that because of the large delta T and thus the large heat utilisation, the mixer has to take 60 l of 45-gram storage water from the buffer for one kilowatt hour of heating output, which it returns at a "cold" 30 °C. The heat exchanger would have to be cooled to exactly these 60 l on the primary side. The "sys" model would throttle the primary-side circulation to exactly these specific 60 l (60 x 15 K = 900 kcal = approx. 1 kWh). The theoretical alternative: The return flow of the secondary circuit (radiators) of 28 °C lowers the primary temperature (from the storage tank) of 45 °C to the same flow of 33 °C in a mixer and, now itself heated to 35 °C, flows back to the storage tank. With this architecture, the delta T is only 10 K. Thus, for 1 kWh of heating output, the control system has to draw 50 percent more 45-grd water, namely 90 l. The result: although warmer return water flows to the storage tank, the overall stratification drops for the same heat content. The extra calories in the bottom zone are now missing in the high-temperature zone. One could have heated with the loss volume at the top, but not with the sediment at the bottom. In other words, the second rendeMIX, the one on the discharge side of the tank, gives the residents of the house at Weidenstraße 7, Alfter, an even longer period of time
to not have to worry about their wood boiler.
In Realo, the "Logano" therefore first circulates the water in its registers up to at least 65 °C. Only above this limit temperature does it push heat into the buffer or into the radiators. But how do you turn a high-temperature boiler into a low-temperature heating system? Precisely via the buffer described and via two multi-way mixers of the "rendeMIX" type from HG Baunach GmbH Co KG, Hückelhoven. These make it possible to economise on the hot water supplied by the boiler. However, Schmitz first had to equip his storage tank accordingly: namely with perforated immersion pipes that specifically charge and discharge the corresponding temperature zones of the storage tank and thus prevent thermal mixing.
Waste heat for water heating
18,000 euros were later added to the bill for the conversion. This price includes the complete modernisation measures, including the log boiler, tank conversion and new copper piping. The price does not include the domestic hot water heat pump and the ventilation system for controlled ventilation of the rooms in each flat.
Heat pump and air duct system form one unit. As is well known, the waste product of controlled domestic ventilation is energy-rich heated exhaust air. Either it flows outdoors without further use or it preheats the supply air via a heat exchanger. Or - as in the case of the building described - it serves as an energy source for the domestic hot water heat pump. In this constellation, the heat pump as a compact model replaces the traditional domestic hot water tank and the heat recovery system:

Fig. 6: The air-water heat pump for domestic hot water heating (type WPL 5030 EW) draws its energy from the exhaust air streams of the controlled flat ventilation.
The supply air flows decentrally into the individual rooms; a fan unit extracts it from the kitchen and bathroom via an exhaust duct system and feeds it to the heat pump. The cooled exhaust air escapes to the outside. If there is a very high demand for hot water, a 1.5 kW electric heater is switched on. The water volume inside the storage tank is 300 l, the heating time is given by the manufacturer at a waste heat temperature of 20 °C, a relative humidity of 40 per cent and about 200 m3/h volume flow rate with about 10 hours for a storage temperature of 55 °C. This results in 4.1 kWh for a complete filling with a stated power consumption of 410 watts.
What does "efficient heat storage" mean?
What could the optimal heat storage in the former oil tank look like? First of all, a stable stratification must be achieved, because only this guarantees a high usability of the stored heat. Example party and bottles: The usefulness of the undrunk beer can be measured by its distribution among the bottles. Leftover quarter- and half-full bottles are usually tipped out. It is wiser to first pour out all the bottles that have been opened and then put the full bottles away later. The same applies to the heat in the container. It is all the more valuable the more concentrated it is stored in the buffer.
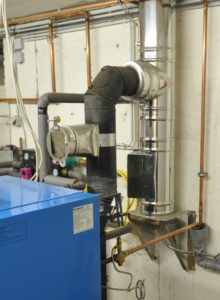
Fig. 7: The "Logano S 151" solid fuel boiler is located in the former air-raid shelter. Since there was no chimney, the plant engineers had to install a stainless steel chimney. In the foreground, the thermal discharge safety device in case of boiler overheating.
So instead of distributing it evenly and at medium temperature over the entire storage tank content, hot and consequently cold zones should be set up as sharply as possible. If, on the other hand - as with the usual single-zone discharge - a three-way mixer constantly mixes the hot water of the upper connection with the cold return flow of the system, not only does the hot supply shrink unnecessarily quickly; only a little cold water reaches the return flow to the buffer. If the cold zone is missing, the buffer cannot store any environmental low-temperature heat, for example.
The two-zone discharge, on the other hand, first takes the hot water from the middle connection and taps the cold system return. This leaves the hot water cushion at the top untouched and more cold water flows back to the lowest buffer connection. If the supply from the middle connection is below the desired flow temperature, it is sufficient to raise the temperature to target with a few litres of hot water from the top connection and send the entire return into the buffer. In both cases, the water stays hot longer at the top and gets cold faster at the bottom.
Besides unloading, loading is also decisive
Let's now look at the necessary return temperature increase (RLA) of a wood boiler. Buderus prescribes a minimum temperature of 60 °C. The boiler first raises its internal boiler circuit to this return level. Only above 60 °C does it open the flow to the consumers. In combination with the buffer storage tank, a circuit that mixes the hot water of the boiler flow with the cold water of the lower buffer connection for RLA would be tantamount to wasting energy. The "Logano" would only be able to push a small amount of hot water into the buffer, as it would have to consume the majority of it at the RLA.
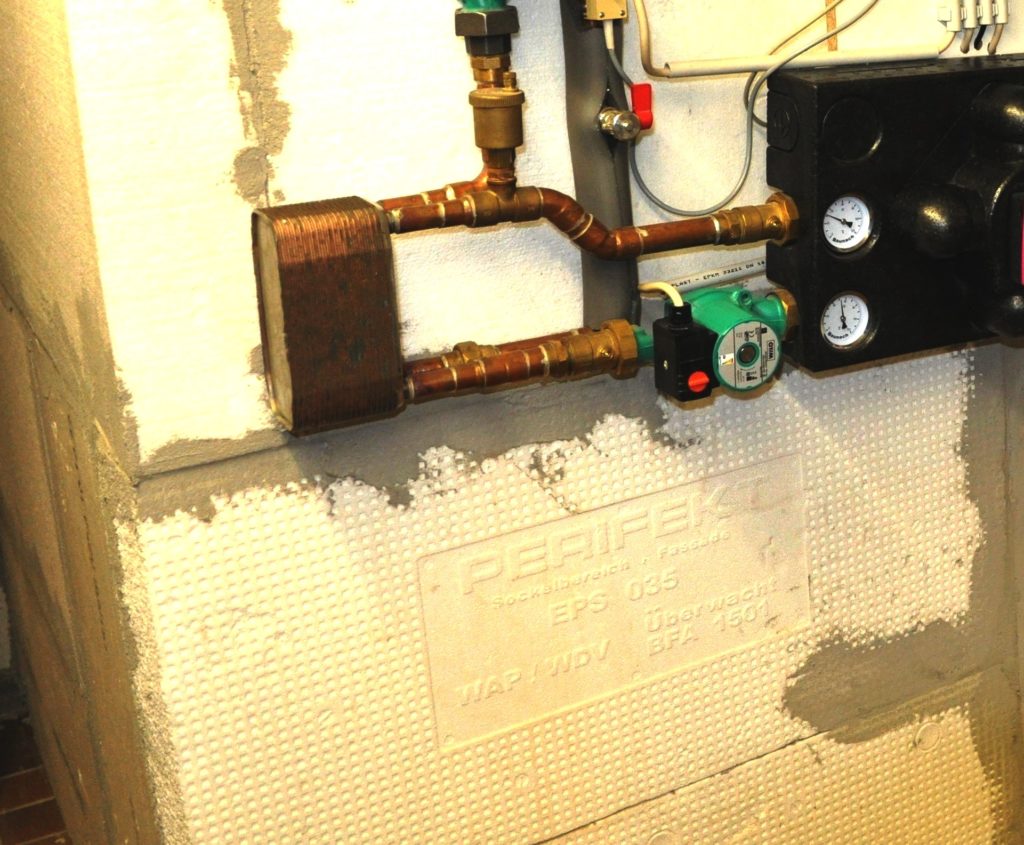
Fig. 8: The polystyrene bricks were left over from the insulation of the house. They are now used to insulate the former oil steel tank. Perifekt 035" are polystyrene elements for insulating exterior surfaces, known in common parlance as perimeter insulation boards (perimeter = enclosure).
The two-zone control, on the other hand, uses the hot boiler flow plus hot water from the centre connection for the RLA in moderation as long as this is below the desired boiler return temperature. As a result, more hot water reaches the upper buffer zone. If the temperature of the centre connection exceeds the desired boiler return temperature, a partial quantity of hot water from the centre connection plus a partial quantity of cold water from the lower connection will keep the return at the required 60 °C to the exact degree. The hot water from the boiler flow remains untouched. The "rMIX 2×3" with two connections to the heat source and three connections for heat extraction directs it completely into the uppermost buffer zone. With parallel two-zone discharging and two-zone loading, the buffer even becomes hotter at the top and colder at the bottom at the same time, which automatically leads to the ideal gradual stratification.
Loading and unloading principle
For single-zone discharge, the control mixes a quarter of 90-gram buffer water with three quarters of 30-gram return water for a 45/30 °C spread. A quarter of the 30-gram return flows back into the storage tank. Despite only 45 °C flow, the hot supply is tapped at the top of the buffer. The stratification in the buffer weakens to 60/45/30. The absorption of low-temperature heat is made more difficult.
With dual-zone discharge, the water at the top of the buffer stays hotter for up to 30 % longer. Zoning is maintained. It facilitates the absorption of low-temperature heat.
With single-zone loading with return flow boost. Relatively little hot water reaches the buffer only very late. The charging process is prolonged. The absorption of low-temperature heat is made more difficult.
With two-zone loading with return lift, the loading time for hot water is shortened. The 30-degree zone stays cold longer. The absorption of low-temperature heat is facilitated.
The rendeMIX fittings ensure ideal stepped stratification and thus optimise the use of the buffer water heat.
High comfort as proof of storage efficiency
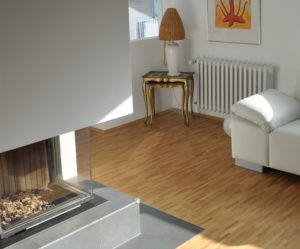
Fig. 9: In the transitional period, the boiler may remain switched off. Each of the three residential units still has an open fireplace, which is sufficient to heat the rooms when outside temperatures are moderate.
What storage efficiency means for the operator can be summed up in a few words: Instead of having to add smaller amounts of wood more frequently during the transitional period - i.e. during partial load operation - he can limit himself to waiting calmly until the buffer is completely empty and then add a full load of wood correspondingly less frequently. Again, only good stratification is decisive for this, because the boiler must be fired when the required flow temperature is no longer available at the upper connection of the buffer.
However, as mentioned, this says nothing in principle about how much (possibly no longer usable) heat is still underneath. Only with good stratification together with stratified discharge does the buffer empty completely - the absolute prerequisite for being able to store a maximum amount of heat again. A continuously stable hot zone is also the guarantee for an equally well-developed cold zone. This pays off especially in systems with solar backup heating. Because too high a temperature in the lower buffer zone is a hurdle that the sun can hardly overcome in winter to store a moderate temperature level.
Logs also cost
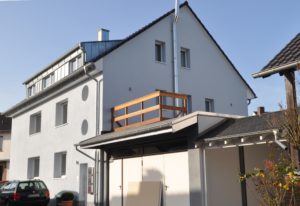
Fig. 10: In the three-family house in Alfter, the approximately 400 square metres of living space are distributed over three residential units.
Schmitz implemented the "layered" loading and unloading in the Alfter property. Without a rendeMIX multi-way mixer, the Buderus "Logamatic" would always have to mix hot boiler or storage water with cold return water for precise flow temperature control. The heating system would not be able to access a medium temperature supply during milder weather conditions. Inevitably, the heat generator would have to cycle more frequently. On the one hand, cycling burdens user comfort. Operators have to fill the boiler with a small amount of wood several times, ignite it and burn it, instead of filling the combustion chamber once and then leaving it alone for a whole day. From a physical point of view, cycling burdens the heat generator itself as well as efficiency and the environment: losses increase in the start-up phase.
How the regulation works in detail in the object is described in the adjacent box with the heading "Schaltschema Weidenstraße 7, Alfter". By the way: The current wood prices (average February 2010) are about 80 € per cubic metre and thus about 3.8 cents per kWh. For comparison: With heating oil as well as with natural gas, one would have at least 55 percent more energy costs with 6 cents per 1 kWh at the same time.
Bernd Genath