Aumento de los beneficios
Renovación de la tecnología de calefacción con el ejemplo de Chemoplast NV
Es probable que la UE y Alemania puedan Objetivos de Kioto si todos los fabricantes examinaran periódicamente sus costes energéticos y fueran capaces de clasificarlos. Hay que reconocer que las grandes lo hacen, las medianas empresas menos. Ejemplo: Un empresario alemán con un negocio en Bélgica sacudió recientemente la cabeza sorprendido. Los resultados de la renovación de su casa de Colonia le habían abierto los ojos a lo que probablemente había estado regalando durante años en Limburgo, Flandes.
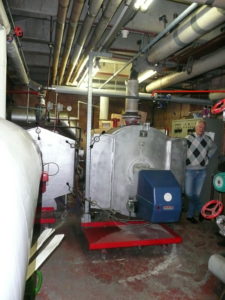
Imagen 1: Sistema antiguo sobredimensionado con un generador de vapor de unos 400 kW y una caldera de 1,4 MW. A la derecha, Werner Sauer, propietario de Chemoplast.
Quien promete y vende eficiencia de condensación también debería garantizarla. En otras palabras, el sistema hidráulico debe ajustarse con precisión para que los gases de combustión condensen realmente su calor latente. Al pasar del valor calorífico al valor de condensación, el fabricante del sistema suele eliminar los fallos graves de la red, pero a menudo no sabe cómo realizar conexiones hidráulicas inteligentes. En consecuencia, se desaprovecha un valioso potencial.
Todo empieza por analizar la situación actual
Por eso, las empresas y los planificadores experimentados no se fían de lo que figura en los documentos de los grandes complejos. Conectan aparatos de medición y comprueban la presión y el caudal. A la hora de reformar sistemas existentes, no pueden prescindir de esta adquisición de datos si no quieren arrastrar a la reforma errores del pasado. Los errores del pasado suelen consistir en tuberías, bombas y accesorios sobredimensionados. Éstos compensaban las deficiencias de la tecnología de control con un coste de unos pocos pfennigs por kilovatio hora, por muy intensiva que fuera la energía de la empresa.
Durante años, el empresario Werner Sauer tampoco había pensado mucho en la eficiencia de los sistemas de generación de energía de su empresa de detergentes. Aunque sus detergentes limpian todos los trenes de cercanías de Viena, los trenes Siemens de la ruta transiberiana y los robots de pintura de la industria automovilística -que deben aclararse a fondo después de cada cambio de color-, "no nos interesaba tanto mantener limpio el aire", admite el propietario de Chemoplast NV en Houthalen, en Limburgo (Bélgica).
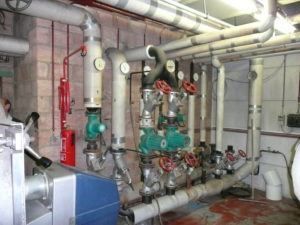
Figura 2: Distribución del calor antiguo
La fábrica, incluidos sus equipos técnicos de construcción, data de los años sesenta. Tras reformar su vivienda particular, el renano se dio cuenta de la necesidad de una renovación energética completa. El arquitecto de Colonia Wilhelm Riphahn, representante del "Neues Bauen" en la tradición del estilo Bauhaus, que enriqueció el panorama de la ciudad catedralicia en los años 20 con el "Bastei" sobre el Rin y en los 50 con el teatro de la ópera, había diseñado una especie de torre residencial con ventanas parcialmente redondeadas de acristalamiento sencillo, que sólo podían sustituirse por vidrio aislante a un coste infinito, con una gruesa protección monumental para la fachada exterior de piel relativamente fina y con radiadores de alta temperatura para proporcionar calor.
El factor de coste oculto
Hans-Georg Baunach, amigo y asesor del propietario de la casa y creador de los mezcladores "rendeMIX", cortó en algún momento el circuito de alta temperatura de los baños y otras zonas que entretanto habían sido equipadas con calefacción por suelo radiante. Los mezcladores multivía de Baunach optimizaron el sistema hidráulico en el diseño de Riphahn. Cuando el balance después de los primeros inviernos fríos mostró que la conversión había reducido notablemente la factura de gas natural, este ahorro recordó a Werner Sauer sus deficiencias en la fábrica de Bélgica. Aunque todos los meses había sacudido la cabeza ante los costes de funcionamiento, los había aceptado como algo natural. En una planta de producción con muchos puestos, no eran un factor de coste reconocible. No faltaba calefacción, ni agua caliente. Para qué cuestionar la tecnología.
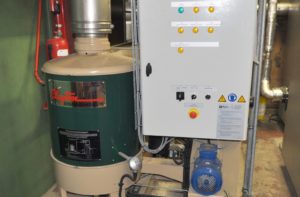
Figura 3: Generador de vapor alimentado con fuel-oil renovado (principio de flujo continuo) para calentar los tanques de mezcla en producción según las necesidades, producción de vapor a 1 bar 157 kg/h
En su casa renovada de Colonia, sin embargo, descubrió lo que probablemente estaba regalando de año en año en Houthalen. Por supuesto, al analizar la situación actual en Flandes surgió el típico problema de los edificios antiguos. Faltaban documentos, cifras exactas y esquemas eléctricos. "Nos encontramos con una caldera de gasóleo, cuya potencia sólo investigamos a posteriori. La placa de características se había desintegrado. Después resultó ser de 1,4 megavatios. Tampoco encontramos nada en los documentos sobre el generador de vapor de gasóleo. Tras recalcular y reflexionar un poco, se estimó que entregaba 400 kW. Todo lo que se decía sobre las necesidades de agua caliente para la producción era: "Necesitamos grandes cantidades de al menos 80 °C". Lo que eso significaba en realidad seguía siendo impreciso", recuerda el dueño de la fábrica.
Horas de funcionamiento y contador de impulsos
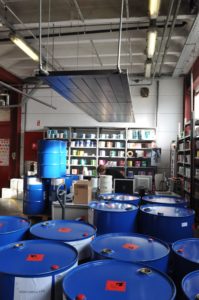
Figura 4: Paneles radiantes de techo calentados por agua caliente en lugar de aire caliente en la zona de trabajo con ventilación forzada.
"Ahora, por supuesto, todo esto viene de una época en la que la energía costaba poco. Concretamente, el gasóleo de calefacción. Bélgica es un país petrolero. El gas natural holandés no fluye, sólo cruza la frontera. En otras palabras, ante el suministro barato de petróleo, hacíamos poco por calcular a los consumidores individuales. No había contadores en ninguna parte". Cuando pidió a Hans-Georg Baunach que viniera a Limburgo en octubre de 2007 tras la reforma de Colonia, lo primero que le recomendó fue instalar contadores de horas de funcionamiento y de impulsos en el generador de vapor y la caldera. Por un lado, el generador de vapor mantenía las cubas de doble pared de producción a temperatura de funcionamiento y, por otro, alimentaba el calentador instantáneo de agua para la preparación de agua caliente. Esta agua caliente, a su vez, tenía que estar constantemente disponible a una temperatura bastante elevada para poder añadir espontáneamente entre 300 y 700 litros de agua a alta temperatura a los productos químicos y polvos de las cubas de mezcla en momentos no programados.
La zona de producción climatizada ocupa 6.000 m2Algunos de ellos son de ventilación forzada por razones de protección contra explosiones. En las zonas peligrosas sólo pueden instalarse aparatos a prueba de explosiones. En cuanto a la calefacción, los sopladores de aire caliente eran una opción entonces como lo son ahora. Sus intercambiadores de calor agua/aire se alimentaban de la antigua y se alimentan de la nueva caldera de gasóleo a través de un único conducto de ida y retorno, que sale de la sala de calderas de diámetro nominal 100 y se ramifica por los distintos edificios.
Tiempo de funcionamiento del quemador un solo minuto
"Por un lado, las mediciones mostraron que la caldera no alcanzó ni siquiera 50% de utilización en ningún momento durante dos periodos de calefacción, mientras que la caldera de vapor sólo cubre sus pérdidas de reserva con la mayor parte de su combustible. Por otro lado, también debido a las quejas de los empleados, era obvio que no tenía ningún sentido calentar las partes con corrientes de aire de estas zonas de trabajo con aire atemperado, como se hacía antes. La ventilación se llevaba el calor inmediatamente. La ventilación permanente tenía que costar una cantidad enorme sin que la hubiéramos calculado en detalle. Por eso, en lugar de ventilación, hicimos instalar paneles radiantes en el techo directamente encima de algunos puestos de trabajo. Ahora calentamos las zonas críticas por radiación. Estos paneles también se alimentan del caudal común de la caldera de gasóleo", explica Hans-Georg Baunach, describiendo uno de los primeros pecados relacionados con la energía y el remedio.
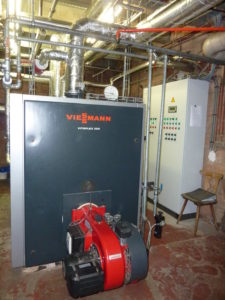
Figura 5: Temperatura de impulsión de hasta 85 °C de la caldera de condensación de gasóleo (Viessmann Vitoplex) con una potencia de 700 kW
Volviendo al análisis real, las horas de funcionamiento y el número de ciclos: el sobredimensionamiento de la vieja caldera (que más tarde resultó ser de 1,4 MW) iba más allá de lo imaginable. Incluso en pleno invierno, hacía largas pausas y, cuando funcionaba, lo hacía entre uno y un máximo de diez minutos. A pesar de ello, el personal de los puestos de trabajo era literalmente bañado en aire caliente.
En lugar del ineficiente sistema de calefacción de gasóleo, un sistema de condensación de gasóleo de 700 kW (Viessmann) abastece ahora a los consumidores de agua de calefacción. Se equipó con un quemador Weishaupt de dos etapas para garantizar un funcionamiento eficiente incluso a carga parcial.
Costura de soldadura como vendaje de emergencia
También se producían pérdidas superfluas en tramos más pequeños de la red. Por ejemplo, la circulación hacia el grifo de agua caliente del lavabo esporádicamente utilizado en el laboratorio, a cien metros de distancia, bombeaba agua caliente durante 24 horas, y el generador de vapor de baja presión en forma de una colosal y vieja caldera de hierro fundido permanecía inútilmente bajo vapor durante la mayor parte del tiempo, sólo para poder suministrar el calor esporádicamente necesario en cualquier momento. Hasta que finalmente empezó a mostrar grietas. Tuvo que permanecer en servicio durante unas semanas con un vendaje de emergencia en forma de costura soldada antes de ser sustituida por una unidad de menos de la mitad de tamaño.
Otras medidas en resumen: el fabricante de instalaciones Karremans NV de Zonhoven (Bélgica) cortó la tubería que iba al lejano laboratorio y atornilló un calentador de agua eléctrico instantáneo independiente bajo el lavabo. Para suministrar agua caliente a la fábrica, instaló un cilindro relativamente modesto de 1.000 litros calentado por camisa con una caldera de condensación de gasóleo independiente, que ahora sólo tiene unos 20 kW (Vaillant).

Figura 6: Estación "rendeMIX". Para el funcionamiento, véase el cuadro "Esquema de calefacción".
Como la producción sólo se realiza dos veces al día, los 20 kW disponen de cuatro horas para recargar el acumulador. Al mismo tiempo, la potencia de la caldera que debe suministrarse durante todo el año para el calentamiento de ACS se reduce a una fracción de la original.
Sistema de calefacción
El esquema explica el circuito de la instalación de calefacción con el circuito del ventilador y el circuito del radiador. La caldera de condensación de gasóleo Viessmann Vitoplex 200 (700 kW) con quemador Weishaupt de dos etapas debe mantener en primer lugar la temperatura de ida compensada por las condiciones meteorológicas de al menos 45 °C hasta 85 °C. °C para la calefacción por aire caliente (LU). El diseño se basa en un reparto de 85/45 °C. Sin embargo, es probable que la tasa de respuesta se sitúe en torno al 50 °C. La caldera consta de una caldera de poder calorífico y un intercambiador de calor latente aguas abajo. Su flujo sirve directamente al circuito principal (controlado por el quemador) con una tubería NW 100.
La filosofía del circuito rendeMIX consiste en crear gradientes de temperatura elevados. Uno de los errores del pasado era combinar los retornos frío y caliente y devolverlos juntos a la caldera, según se pensaba: Si aíslas suficientemente sus tuberías, no se perderá calor, por lo que la caldera no tendrá que empujar tanto. Esto es cierto hasta cierto punto, pero debido a la falta de diferencias de temperatura, desgraciadamente ya no es posible recuperar el calor residual de un medio más caliente con la ayuda de un medio más frío para, posiblemente, igualar el calor sólo con la temperatura mezclada. Sólo desde la introducción de la tecnología de condensación y la condensación, así como la aceptación de diferentes niveles de temperatura, la tecnología de calefacción ya no acumula la energía de retorno en un único recipiente, sino que la separa en diferentes recipientes de anergía y exergía.
En el lado de la válvula, el conmutador más elegante para ello es probablemente el método "rendeMIX". En el circuito del radiador (rueda) del diagrama de conmutación, los dos distribuidores mezcladores 250 3×2 VL 5 del punto 7 toman el agua de retorno del ventilador de 45 oC y enviar el flujo de retorno del radiador de 35°C a través del punto 2 al intercambiador de calor latente RL2. El caudal de 60 °C mezclar el "rendeMIX" del retorno del ventilador de 45 rejillas más una toma de flujo de 85 rejillas (a través del punto 1).
El intercambiador de calor latente (aguas abajo de RL2) empuja las ganancias del condensador al conducto de retorno RL1. La imagen no lo muestra directamente, pero el sistema hidráulico es el siguiente: el flujo de retorno RL2 fluye a través del intercambiador de calor latente hacia el flujo de retorno RL1 y, a continuación, vuelve a la temperatura de flujo de 85 °C a través de la caldera de aceite. °C a subir.
Antes de mezclarse con RL2, RL1 tiene una temperatura de 45 a 50 oC, según el ajuste de los termostatos de retorno (válvula RTB) de los ventiladores de aire caliente. Como ya se ha mencionado en el texto principal, la válvula RTB bloquea el caudal de retorno del ventilador por encima de 45 a 50 °C. El aumento resultante de la presión diferencial garantiza que el volumen de agua circulante en el circuito del ventilador se regule con la ayuda de la bomba de alta eficiencia controlada, a un Delta-T constante.
El rCOL inferior 3×8 - 2 es básicamente un distribuidor. En él se montan los dos tipos DN25 3×2 VL 5. Tres por dos significa: tres conexiones de entrada (2 - 7 - 1) y dos de salida (6 - 5). El número adicional 5 indica simplemente la bomba de circulación que se puede embridar directamente al caudal (5).
A la derecha, el tercer rectángulo gris denominado sBox DN25 2×2 VL 3indica el circuito de calefacción no controlado para el calentamiento de agua caliente sanitaria (reserva). En caso necesario, también puede ser suministrado por la caldera de 700 kW. El conjunto incluye la bomba de circulación con freno de gravedad, termómetros y la función de válvula de cierre, pero alimenta su caudal de retorno a la cámara central del colector, de modo que se une al caudal de retorno del aerotermo de 50 kW y permanece separado del caudal de retorno del radiador de 30 kW.
El calentador de agua caliente de 1.000 litros (fig. 2) se calienta o bien con la caldera de condensación de aceite especificada de Vaillant (icoVIT), con una potencia de 19 kW, o bien con la caldera Viessmann de 700 kW, que también alimenta el circuito del ventilador. "Alternativa" en este contexto se basa en la situación de funcionamiento actual. Mientras que la caldera principal produce el calor para el circuito del ventilador, también puede cargar el acumulador. La planificación también integró un limitador de temperatura de retorno en este esquema para garantizar tanto el funcionamiento de condensación en la caldera Vaillant como para estabilizar el sistema hidráulico en el circuito principal -si el generador de calor Viessmann abastece al cilindro- a los 45 a 50 °C mencionados.
El nuevo generador de vapor alimentado con gasóleo de calefacción ya no tiene nada que ver con el calentamiento de agua. Sólo alimenta los tanques de mezcla durante el funcionamiento y adapta así sus horas de funcionamiento a la necesidad real de vapor, utilizando el principio del calentador de agua instantáneo de bajo consumo de agua y, por tanto, de bajo consumo energético (tipo Clayton EO-10, potencia 100 kW, presión de funcionamiento ajustable hasta 7 bar, producción de vapor a 1 bar 157 kg/h), que también minimiza las pérdidas en modo de espera.
En resumen, la tecnología hidráulica y de suministro para los tres circuitos de calefacción, agua caliente y vapor, o cuatro con el calentador de agua eléctrico instantáneo en el laboratorio no a prueba de explosiones. El plan director remodelado ya prometía una reducción considerable del consumo.
Optimización con colectores de mezcla
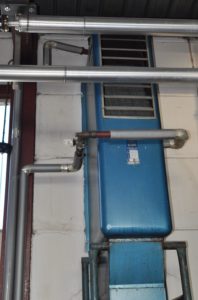
Figura 7: Los ventiladores existentes no se sustituyeron, pero se adaptaron a la condensación con válvulas termostáticas como limitadores de la temperatura de retorno.
Además, el perfeccionamiento de la ingeniería de control del sistema de calefacción también debería generar ahorros. El título largo de esta medida es: "Optimización del sistema de calefacción en Chemoplast NV - funcionamiento eficiente del sistema de caldera de condensación de tamaño reducido mediante la conversión a un colector de tres cámaras con uso de retorno para dos circuitos de radiadores controlados con 'rendeMIX' y S-Box para cargar el depósito de agua caliente". Detrás de esto se encuentra en última instancia el esquema hidráulico especial de HG Baunach GmbH & Co. KG basado en el colector de mezcla multipuerto "rendeMIX". Estos permiten conectar en serie circuitos de alta y baja temperatura, convirtiendo el retorno de un circuito de alta temperatura en el caudal de un circuito de baja temperatura, con las secciones de compensación interna y externa de la instalación "rendeMIX" equilibrando correctamente los volúmenes de agua individuales.
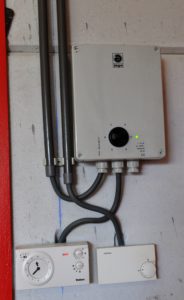
Figura 8: ... y con convertidores de frecuencia para controlar la velocidad del ventilador
El proceso ya ha demostrado su eficacia varios miles de veces en la construcción de viviendas al permitir acoplar radiadores (de alta temperatura) con calefacción por suelo radiante (de baja temperatura). En primer lugar, esto beneficia a una gran dispersión de la temperatura y, por lo tanto, generalmente reduce al menos a la mitad el volumen de agua que debe circular. En segundo lugar, el agua de retorno ahora fría, que suele estar muy por debajo de los 30 oC en el intercambiador de calor de condensación de la caldera, los gases de combustión se enfrían muy por debajo del punto de rocío para que no se pierda el calor latente. La caldera de condensación sólo puede cumplir su función de aprovechar el calor de condensación para calefacción si la temperatura de retorno es correspondientemente baja.
Dos conexiones de retorno
En Chemoplast NV, en Europark (Flandes), el circuito de ventiladores con control climático es el circuito de alta temperatura. En sentido estricto, la caldera de condensación de gasóleo consta aquí de dos componentes, una caldera de poder calorífico y un intercambiador de calor latente separado en el conducto de gases de combustión. HG Baunach GmbH & Co. KG eligió esta combinación para poder funcionar con dos conexiones de retorno, una en la caldera y otra en el condensador. La ventaja de estas dos conexiones de retorno puede explicarse de la siguiente manera:
En primer lugar, hay que señalar que los ventiladores de las naves de la fábrica -no se sustituyeron, sino que se limitó su velocidad- se abastecían de un inmenso volumen de agua de hasta 85 litros a través de una tubería en NW 100. oC de temperatura de circulación. Esta temperatura controlada por el clima debe poder alcanzar este nivel para generar suficiente aire caliente. Además, la empresa de calefacción Karremans instaló una válvula termostática como limitador de la temperatura de retorno directamente detrás de cada uno de los cerca de 30 ventiladores. Su termopar cierra la válvula si la temperatura de retorno supera los 45 o 50 °C debido a una extracción de calor insuficiente. oC aumenta. El estrangulamiento asociado envía una señal a la bomba de circulación controlada a través del aumento de la presión diferencial para ajustar el caudal en consecuencia, de modo que los otros ventiladores no se vean afectados.
Este circuito comienza y termina en la caldera de poder calorífico. El flujo de retorno con el mencionado 45 a 50 oC no permite la utilización de condensación, ya que el punto de rocío del gasóleo de calefacción EL es de 48 oC. Además, la condensación no debe producirse en la caldera de poder calorífico debido a su diseño, ya que esta parte de la caldera no está diseñada para ello y, por lo tanto, tiene el refuerzo de flujo de retorno prescrito por razones de seguridad.
Chemoplast NV
En los años setenta, el gobierno belga cerró las minas de carbón de Limburgo. Para compensarlo, el país fomentó la industrialización de la región. Naturalmente, la oferta no pudo satisfacer la demanda de empleo. En cambio, el mercado laboral de Alemania se caracterizaba entonces por la situación contraria. La República Federal se estaba construyendo, el milagro económico florecía y en todas partes escaseaba la mano de obra. Por ello, un empresario alemán de Bergisch-Gladbach, que desde 1936 fabricaba abrillantadores para coches y otros productos para la limpieza exterior e interior de vehículos, trasladó su planta de producción a Houthalen. Había suficiente mano de obra, el nivel salarial era adecuado y, para las entregas en toda Alemania y Europa, daba igual que los camiones entregasen desde Colonia o Bensberg a Francia o Portugal o desde Limburgo, en Bélgica. La administración y las operaciones permanecen en Alemania.
Cuando el automovilista alemán dejó de lavar cuidadosamente a mano con cuero y un paño seco su hijo predilecto, la carrocería, y los productos de lavado de coches sustituyeron a los productos de lavado a mano, Chemoplast NV amplió su gama de productos para incluir productos de limpieza para la industria, los ferrocarriles y las empresas de transporte. Casi todos los trenes de Holanda, incluidos los de cercanías, utilizan productos de Houthalen. Los trenes de cercanías y metro de Viena también obtienen su brillo fresco con productos "Starcare" de Limburg, al igual que las locomotoras Siemens del ferrocarril transiberiano y el ferrocarril ruso de alta velocidad de San Petersburgo a Moscú.
En 2012, Chemoplast NV adquirió la experiencia, las fórmulas y las licencias de una empresa cuyos clientes son fabricantes de automóviles. La gestión de calidad incluye la limpieza cuidadosa de los robots de pintura después de cada cambio de color. Esto se hace con la ayuda de un disolvente especial compuesto por varias combinaciones. Gracias a esta expansión, la empresa germano-belga prevé un aumento del volumen de negocio de entre el 30% y el 40% en los próximos años. Además, la empresa se está estableciendo cada vez más como proveedor OEM para fabricantes de productos de limpieza que desean mantener sus capacidades a un nivel básico.
Poder calorífico garantizado
Entre el 85% y el 90% del calor de suministro lo necesitan los ventiladores, entre el 10% y el 15% los radiadores de las zonas de oficinas y de las instalaciones sanitarias y vestuarios. Para estos generadores de calor es suficiente una distribución de 60/40. oC. Este emparejamiento no significa otra cosa que en la mayor parte del periodo de calefacción, el flujo de retorno está unos pocos o muchos grados por debajo del límite de 40°C. oC se desplaza. Por lo tanto, sólo el retorno del radiador fluye hacia el condensador. Baja la temperatura de los gases de escape a una media de 33 a 35 oC. Por lo tanto, el intercambiador de calor latente es capaz de extraer una gran parte de la energía residual de casi el 10% de los gases de combustión que se escaparía por la chimenea sin él.
Sin embargo, la estrategia de retorno con aprovechamiento del poder calorífico descrita sólo funciona con los mezcladores "rendeMIX", tanto como acoplamiento entre los dos circuitos de calefacción como en calidad de divisor de flujo. La hidráulica del sistema de calefacción de Chemoplast NV es tal que un volumen parcial del caudal de retorno de mayor temperatura del circuito del ventilador alimenta el circuito de radiadores de menor temperatura. Si esto requiere una temperatura de flujo de 60 °C en pleno invierno, el rendeMIX eleva la temperatura de origen de 45 a 50 °C mezclando el agua caliente de la caldera procedente del flujo del circuito del ventilador. Sin embargo, durante la mayor parte de la temporada de calefacción, las habitaciones calentadas por radiador deberían poder conformarse con el agua del ventilador de 45 a 50 °C, que puede reducirse si es necesario añadiendo su propia agua de retorno.
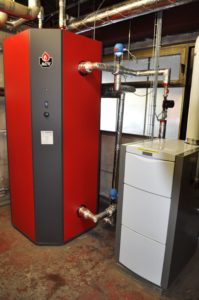
Figura 9: Caldera de condensación de gasóleo de 19 kW (Vaillant icoVIT) para calentar agua caliente todo el año
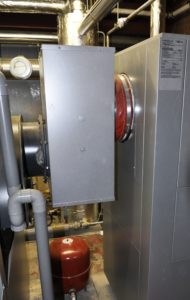
Fig. 10: El intercambiador de calor latente externo situado a continuación de la caldera de gasóleo (extremo derecho, Viessmann Vitotrans) permite la conexión de un retorno de calefacción separado y, por tanto, el aprovechamiento de la condensación a altas temperaturas de impulsión (véase la explicación en el texto). La caja de gases de combustión de color gris plateado situada entre el intercambiador y la caldera se limita a compensar las diferentes alturas de la salida de la caldera y la entrada del intercambiador.
La totalidad de los gases de combustión sale del sistema de caldera de gasóleo a través del condensador con brida. Desde el punto de vista de la tecnología de suministro, actúa como generador de calor para los radiadores, con lo que la ganancia de poder calorífico basta por sí sola para cubrir gran parte de las necesidades de calefacción de las salas sociales y las oficinas.
La reforma comenzó hace 6 años
En 2007, Werner Sauer llegó a la conclusión de que había que hacer algo. En noviembre, empezó a registrar los datos de ambos generadores de calor, a lo que siguieron las primeras medidas hidráulicas en el verano de 2008, como la instalación de paneles radiantes en el techo, el reequipamiento de limitadores de temperatura de retorno y la instalación de una bomba regulada de alta eficiencia. En 2009, la evaluación de los datos medidos puso de manifiesto el enorme sobredimensionamiento de la caldera y el generador de vapor y, en el verano siguiente de 2010, se completaron las obras de reconversión de la red hidráulica con la instalación de reguladores de velocidad para los calentadores de aire. Estas medidas por sí solas no solo ya habían permitido reducir las necesidades anuales de gasóleo de calefacción de una media de unos 60.000 litros a 50.000 litros de gasóleo de calefacción, es decir, unos 15%, sino que también habían aumentado el delta T del circuito del ventilador de los 2K iniciales a unos respetables 20K. Solo ahora, en opinión de Hans-Georg Baunach, era el requisito previo para perfeccionar y hacer realidad los planes de conversión a una caldera de condensación por demanda y a un sistema de distribución de calor por condensación. El pistoletazo de salida se dio en la primavera de 2011, cuando el antiguo generador de vapor sufrió una fuga: la operación de emergencia para sustituir la caldera, incluida la distribución de calor, la preparación de agua caliente y la generación de vapor, se llevó a cabo durante el periodo de calefacción, pero el sistema de control completo no entró en funcionamiento hasta principios del verano de 2012. Basándose en los intervalos de tiempo entre los llenados de los depósitos, se podía predecir un "rendimiento" adicional de entre el 20% y el 25% al cabo de pocos meses, es decir, una nueva reducción del consumo de gasóleo de calefacción de una media de 50.000 a 40.000 litros al año.
Hoy 40.000 en lugar de 60.000 litros de gasóleo de calefacción
Es poco probable que este rango sea aún el máximo, ya que aún hay potencial de optimización, sobre todo en el ajuste del sistema de control. "Supongo que al final no sólo ahorraremos más de un tercio del aceite, sino que también se reducirá considerablemente el consumo eléctrico, ya que la bomba de alto rendimiento controlada sólo puede desarrollar plenamente su efecto mediante la instalación del limitador de temperatura de retorno", explica Hans-Georg Baunach.
Las válvulas termostáticas como limitadoras de la temperatura de retorno, junto con la bomba controlada por presión diferencial, garantizan el equilibrio termohidráulico: si la válvula regula el caudal debido a temperaturas de retorno excesivas, la temperatura de retorno permanece constante incluso si los ventiladores de los calentadores de aire se desconectan mediante termostatos eléctricos de ambiente. Sin embargo, esto reduce la potencia calorífica durante el funcionamiento del ventilador, lo que provoca "corrientes de aire frío" si la velocidad del ventilador sigue siendo alta. Sin embargo, mientras se pueda seguir proporcionando la potencia calorífica necesaria, la reducción de la velocidad del ventilador tiene las siguientes ventajas:
- Mayor temperatura de salida del aire
- Menor velocidad del aire y, por tanto, menor contaminación por polvo
- Menor emisión de ruido
- Utilización más uniforme de las superficies de calefacción.
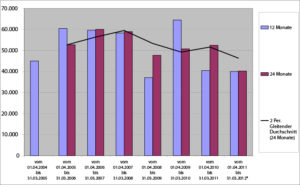
Figura 11: En relación con el año base 2007 (años comprendidos entre el 1 de abril del año respectivo y el 31 de marzo del año siguiente), el año anterior al inicio de las obras de renovación, la renovación hidráulica en los años 2008 a 2010 ya supuso una reducción del consumo de gasóleo de calefacción de 60.000 litros a 50.000 litros. La posterior sustitución del antiguo sistema por una moderna caldera de condensación de gasóleo (puesta en servicio en diciembre de 2012) permitió ahorrar otros 10.000 litros de gasóleo de calefacción. El consultor Hans-Georg Baunach y el constructor de sistemas Karremans "no consideran que este sea el final de la historia" (Baunach). Prevén un aumento aún mayor de la eficiencia al final de este periodo de calefacción, el primero en el que la calefacción se suministrará íntegramente con el nuevo sistema, incluido el control.
Ajedrez hidráulico desordenado
Este último punto en particular no debe subestimarse en términos de eficiencia del sistema: Cuanto más uniformemente fluya todo el calor a través del cuello de botella de todas las superficies de calefacción, menor será el delta T necesario entre el agua y el aire. Esto influye especialmente en la temperatura de retorno y, por tanto, en la eficiencia de la utilización de la caldera de condensación. Por lo tanto, el hecho de que la caldera entre o no en modo de condensación suele decidirse en el lado de la instalación.
Hans-Georg Baunach resume: "En términos de tecnología de calefacción, muchas plantas industriales son probablemente un erial. Mírelo de este modo: cada 100 litros de gasóleo de calefacción ahorrados reducen la carga de la atmósfera en unos 250 kg de dióxido de carbono. Sólo hay que visualizar estas cifras. Si el legislador regulase o fomentase rigurosamente el parque antiguo en este ámbito, Alemania y la UE podrían alcanzar fácilmente todos los objetivos de Kioto. Ni que decir tiene que nosotros, la industria de la calefacción, no debemos jugarnos nuestra reputación. No debemos permitir que las calderas de condensación funcionen predominantemente en modo de poder calorífico. Nosotros, los fabricantes y proveedores de componentes, ofrecemos todas las posibilidades técnicas para optimizar el sistema hidráulico junto con la planificación".
Consumo energético medido del edificio
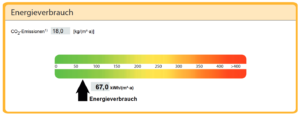
Fig. 12: El pase energético revela: con una superficie calefactada de 6.000 m², un consumo anual de gasóleo de calefacción de 40.000 litros con un consumo energético de 67 kWh/m²-a) y unas emisiones de CO2 de 18 kg/m²-a corresponde prácticamente a un estándar de vivienda de bajo consumo energético - ¡para un edificio de los años 60 con ventilación forzada en la zona de trabajo protegida contra explosiones!
Chemoplast NV Houthalen (Bélgica)
Volumen de inversión: 240.000 euros
Ahorro de costes: 12.000 euros
Flujo de caja: 5%
HG Baunach GmbH & Co. KG
Correo electrónico: info@baunach.net
Página web: www.baunach.net