Zwiększony zysk
Renowacja techniki grzewczej na przykładzie Chemoplast NV
Jest prawdopodobne, że UE i Niemcy mogłyby Cele z Kioto gdyby wszyscy producenci regularnie przyglądali się swoim kosztom energii - i potrafili je sklasyfikować. Co prawda robią to duzi, średnie firmy mniej. Przykład: Niemiecki przedsiębiorca prowadzący działalność gospodarczą w Belgii potrząsnął niedawno głową ze zdziwienia. Wyniki remontu jego kolońskiego domu otworzyły mu oczy na to, co prawdopodobnie przez lata oddawał w Limburgu we Flandrii.
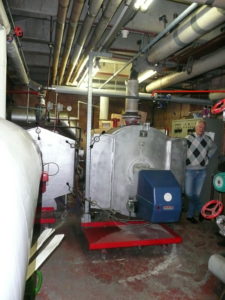
Zdjęcie 1: Powiększony stary system z generatorem pary o mocy ok. 400 kW i kotłem o mocy 1,4 MW. Po prawej właściciel Chemoplast, Werner Sauer.
Każdy, kto obiecuje i sprzedaje wydajność kondensacji, powinien również ją zagwarantować. Innymi słowy, hydraulika powinna być precyzyjnie wyregulowana tak, aby spaliny faktycznie skraplały swoje utajone ciepło. Przechodząc od wartości opałowej do wartości kondensacyjnej, producent systemu zwykle eliminuje poważne błędy sieci, ale często nie wie, jak wykonać inteligentne połączenia hydrauliczne. W rezultacie cenny potencjał zwykle pozostaje nierozpoznany i niewykorzystany.
Wszystko zaczyna się od analizy obecnej sytuacji
Dlatego doświadczone firmy i projektanci nie polegają na tym, co jest wydrukowane w dokumentach dla rozległych kompleksów. Podłączają urządzenia pomiarowe i sprawdzają ciśnienie oraz natężenie przepływu. Podczas renowacji istniejących systemów i tak nie mogą obejść się bez gromadzenia danych, jeśli nie chcą przenosić błędów z przeszłości na modernizację. Błędy z przeszłości zazwyczaj polegają na przewymiarowanych rurach, pompach i armaturze. Kompensowały one słabości technologii sterowania kosztem kilku fenigów za kilowatogodzinę - niezależnie od tego, jak energochłonne było przedsiębiorstwo.
Przez lata przedsiębiorca Werner Sauer nie zastanawiał się zbytnio nad wydajnością systemów wytwarzania energii w swojej firmie produkującej detergenty. Chociaż jego detergenty czyszczą wszystkie pociągi podmiejskie w Wiedniu, pociągi Siemensa na trasie transsyberyjskiej i roboty lakiernicze w przemyśle motoryzacyjnym - które muszą być dokładnie płukane po każdej zmianie koloru - "nie byliśmy tak zainteresowani utrzymaniem czystego powietrza" - przyznaje właściciel Chemoplast NV w Houthalen w Limburgii w Belgii.
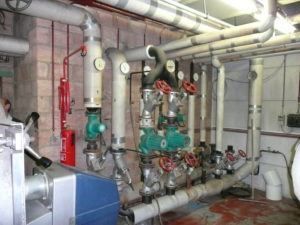
Rysunek 2: Stara dystrybucja ciepła
Fabryka, w tym jej wyposażenie techniczne, pochodzi z lat 60. ubiegłego wieku. Po remoncie swojego prywatnego domu, Rhinelander zdał sobie sprawę z potrzeby całkowitej renowacji energetycznej. Koloński architekt Wilhelm Riphahn, przedstawiciel "Neues Bauen" w tradycji stylu Bauhaus, który wzbogacił panoramę miasta katedralnego w latach 20-tych XX wieku "Bastei" nad Renem, a w latach 50-tych operą, zaprojektował rodzaj wieży mieszkalnej jako budynku mieszkalnego: z częściowo zaokrąglonymi oknami w pojedynczych szybach, które można było zastąpić szkłem izolacyjnym tylko nieskończonym kosztem, z grubą ochroną pomnika dla stosunkowo cienkiej fasady zewnętrznej i z grzejnikami wysokotemperaturowymi zapewniającymi ciepło.
Ukryty czynnik generujący koszty
Hans-Georg Baunach, przyjaciel i doradca właściciela domu oraz twórca armatury "rendeMIX", w pewnym momencie odciął obieg wysokotemperaturowy od łazienek i innych pomieszczeń, które w międzyczasie zostały wyposażone w ogrzewanie podłogowe. Mieszacze wielodrogowe Baunach zoptymalizowały hydraulikę w projekcie Riphahn. Kiedy bilans po pierwszych mroźnych zimach pokazał, że konwersja znacznie zmniejszyła rachunki za gaz ziemny, oszczędności te przypomniały Wernerowi Sauerowi o jego niedociągnięciach w fabryce w Belgii. Chociaż co miesiąc kręcił głową na koszty operacyjne, akceptował je jako coś oczywistego. W zakładzie produkcyjnym z wieloma stanowiskami nie były one rozpoznawalnym czynnikiem kosztotwórczym. Nie brakowało ciepła, ani ciepłej wody. Po co kwestionować technologię.
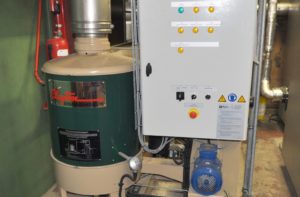
Rysunek 3: Odnowiona wytwornica pary opalana olejem opałowym (zasada ciągłego przepływu) do ogrzewania zbiorników mieszających w produkcji zgodnie z wymaganiami, produkcja pary przy 1 bar 157 kg/h
W swoim odnowionym domu w Kolonii odkrył jednak to, co prawdopodobnie oddawał z roku na rok w Houthalen. Oczywiście podczas analizy obecnej sytuacji we Flandrii pojawił się typowy problem starego budownictwa. Brakowało dokumentów, dokładnych danych i schematów elektrycznych. "Mieliśmy do czynienia z kotłem olejowym, którego moc zbadaliśmy dopiero później. Tabliczka znamionowa rozpadła się. Później okazało się, że było to 1,4 megawata. W dokumentach nie znaleźliśmy również nic na temat olejowej wytwornicy pary. Po ponownych obliczeniach i przemyśleniach okazało się, że dostarczała ona około 400 kW. Wszystko, co powiedziano o zapotrzebowaniu na gorącą wodę do produkcji, brzmiało: "Potrzebujemy ogromnych ilości wody o temperaturze co najmniej 80°C". Co to właściwie oznaczało, pozostało niejasne" - wspomina właściciel fabryki.
Godziny pracy i licznik impulsów
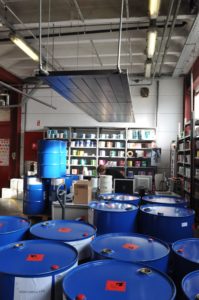
Rysunek 4: Ogrzewane ciepłą wodą promiennikowe panele sufitowe zamiast gorącego powietrza w obszarze roboczym z wymuszoną wentylacją
"Oczywiście wszystko to pochodzi z czasów, gdy energia kosztowała niewiele. W szczególności olej opałowy. Belgia jest krajem naftowym. Holenderski gaz ziemny nie płynie, tylko ścieka przez granicę. Innymi słowy, biorąc pod uwagę tanie dostawy ropy, niewiele zrobiliśmy, aby oszacować indywidualnych konsumentów. Nigdzie nie było liczników". Kiedy poprosił Hansa-Georga Baunacha o przyjazd do Limburga w październiku 2007 r. po remoncie w Kolonii, pierwszą rzeczą, jaką zalecił, było zainstalowanie liczników godzin pracy i impulsów na generatorze pary i kotle. Z jednej strony, wytwornica pary utrzymywała temperaturę roboczą dwuściennych kadzi w produkcji, a z drugiej strony zasilała przepływowy podgrzewacz wody do przygotowywania gorącej wody. Ta gorąca woda z kolei musiała być stale dostępna w dość wysokiej temperaturze, aby spontanicznie dodawać od 300 do 700 litrów wody o wysokiej temperaturze do chemikaliów i proszków w zbiornikach mieszających w nieplanowanych momentach.
Ogrzewany obszar produkcyjny obejmuje 6000 m2Niektóre z nich mają wymuszoną wentylację ze względu na ochronę przeciwwybuchową. Tylko urządzenia przeciwwybuchowe mogą być instalowane w strefach zagrożonych wybuchem. Po stronie ogrzewania, dmuchawy gorącego powietrza były opcją wtedy, jak i są teraz. Ich wymienniki ciepła woda/powietrze były zasilane przez stary i są zasilane przez nowy kocioł olejowy za pośrednictwem pojedynczego przewodu zasilającego i powrotnego, który opuszcza kotłownię o średnicy nominalnej 100 i rozgałęzia się na różne budynki.
Czas pracy palnika - jedna minuta
"Z jednej strony pomiary wykazały, że kocioł nigdy nie osiągnął nawet 50% wykorzystania w żadnym momencie podczas dwóch okresów grzewczych, podczas gdy kocioł parowy pokrywa tylko straty w trybie gotowości z większości paliwa. Z drugiej strony było oczywiste, również ze względu na skargi pracowników, że nie ma sensu ogrzewać przeciągów w tych obszarach roboczych hartowanym powietrzem, jak to miało miejsce w przeszłości. Wentylacja natychmiast odprowadzała ciepło. Stała wentylacja musiała kosztować ogromną kwotę, której nie obliczyliśmy szczegółowo. Zamiast wentylacji zamontowaliśmy więc promiennikowe panele sufitowe bezpośrednio nad niektórymi stanowiskami pracy. Teraz ogrzewamy krytyczne strefy za pomocą promieniowania. Panele te są również zasilane przez wspólny przepływ z kotła olejowego" - mówi Hans-Georg Baunach, opisując jeden z wcześniejszych grzechów związanych z energią i rozwiązanie.
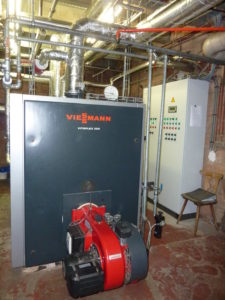
Rysunek 5: Temperatura zasilania do 85 °C z olejowego kotła kondensacyjnego (Viessmann Vitoplex) o mocy 700 kW
Wracając do rzeczywistej analizy, godzin pracy i liczby cykli: przewymiarowanie starego kotła (który później okazał się mieć 1,4 MW) było nie do pomyślenia. Nawet w środku zimy robił długie przerwy, a kiedy już pracował, to od jednej do maksymalnie dziesięciu minut. Mimo to pracownicy na stanowiskach pracy byli dosłownie owiewani gorącym powietrzem.
Zamiast nieefektywnego olejowego systemu grzewczego, olejowy system kondensacyjny o mocy 700 kW (Viessmann) zasila teraz odbiorniki wody grzewczej. Został on wyposażony w dwustopniowy palnik Weishaupt zapewniający wydajną pracę nawet przy częściowym obciążeniu.
Szew spawalniczy jako opatrunek awaryjny
Nadmierne straty były również powodowane przez mniejsze odcinki sieci. Na przykład obieg do kranu z gorącą wodą przy sporadycznie używanej umywalce w laboratorium sto metrów dalej pompował gorącą wodę przez 24 godziny, a niskociśnieniowa wytwornica pary w postaci kolosalnego starego żeliwnego kotła stała bezużytecznie pod parą przez większość czasu, tylko po to, by móc dostarczać sporadycznie potrzebne ciepło w dowolnym momencie. Aż w końcu zaczął pękać. Musiał pozostać w użyciu przez kilka tygodni z awaryjnym opatrunkiem w postaci spawanego szwu, zanim został zastąpiony jednostką mniejszą o połowę.
Dalsze środki w skrócie: konstruktor zakładu Karremans NV z Zonhoven w Belgii przeciął rurę do odległego laboratorium i przykręcił oddzielny elektryczny przepływowy podgrzewacz wody pod umywalką. Aby zaopatrzyć fabrykę w ciepłą wodę, zainstalował stosunkowo skromny podgrzewany płaszczem zasobnik o pojemności 1000 litrów z oddzielnym olejowym kotłem kondensacyjnym, obecnie o mocy około 20 kW (Vaillant).

Rysunek 6: Stacja "rendeMIX". Aby zapoznać się z funkcjami, patrz ramka "Schemat ogrzewania"
Ponieważ produkcja odbywa się tylko dwa razy dziennie, 20 kW ma cztery godziny na naładowanie zasobnika. Jednocześnie moc kotła, która ma być dostarczana do ogrzewania ciepłej wody przez cały rok, jest zmniejszona do ułamka pierwotnej.
Schemat ogrzewania
Na schemacie objaśniono obieg instalacji grzewczej z obiegiem wentylatora i obiegiem grzejników. Olejowy kocioł kondensacyjny Viessmann Vitoplex 200 (700 kW) z dwustopniowym palnikiem Weishaupt musi przede wszystkim utrzymywać pogodową temperaturę zasilania co najmniej 45 °C do 85 °C. °C dla ogrzewania ciepłym powietrzem (LU). Projekt opiera się na rozkładzie 85/45 °C. W rzeczywistości jednak wskaźnik odpowiedzi prawdopodobnie wyniesie około 50 °C. Kocioł składa się z kotła o wartości opałowej i umieszczonego za nim wymiennika ciepła utajonego. Jego przepływ obsługuje główny obieg bezpośrednio (sterowany palnikiem) za pomocą rury NW 100.
Filozofią obwodu rendeMIX jest budowanie wysokich gradientów temperatury. Jednym z błędów przeszłości było łączenie zimnych i gorących powrotów i zwracanie ich do kotła razem, zgodnie z myśleniem: Jeśli wystarczająco zaizolujesz ich rury, ciepło nie będzie tracone, więc kocioł nie będzie musiał tak dużo przepychać. Jest to prawdą w ograniczonym zakresie, ale ze względu na brak różnic temperatur, niestety nie jest już możliwe odzyskanie ciepła resztkowego z cieplejszego czynnika za pomocą zimniejszego czynnika, aby ewentualnie wyrównać ciepło za pomocą samej temperatury mieszania. Dopiero od czasu wprowadzenia technologii kotłów kondensacyjnych i kondensacji, a także akceptacji różnych poziomów temperatury, technologia grzewcza nie gromadzi energii powrotnej w jednym naczyniu, ale rozdziela ją na różne naczynia anergii i egzergii.
Po stronie zaworu najbardziej eleganckim przełącznikiem jest prawdopodobnie metoda "rendeMIX". W obiegu grzejnikowym (koło) na schemacie przełączania, dwa rozdzielacze mieszające 250 3×2 VL 5 w punkcie 7 pobierają wodę powrotną z wentylatora z 45 oC i przesłać strumień powrotny z chłodnicy o temperaturze 35°C przez punkt 2 do wymiennika ciepła utajonego RL2. Przepływ 60 °C wymieszać "rendeMIX" z 45-siatkowego powrotu wentylatora plus zastrzyk 85-siatkowego przepływu (przez punkt 1).
Wymiennik ciepła utajonego (za RL2) wypycha zyski ze skraplacza do przewodu powrotnego RL1. Zdjęcie nie pokazuje tego bezpośrednio, ale układ hydrauliczny wygląda następująco: strumień powrotny RL2 przepływa przez wymiennik ciepła utajonego do strumienia powrotnego RL1, a następnie z powrotem do temperatury zasilania 85°C przez kocioł olejowy. °C do podniesienia.
Przed zmieszaniem z RL2, RL1 ma temperaturę od 45 do 50 stopni Celsjusza. oC, zgodnie z ustawieniem termostatów powrotnych (zawór RTB) wentylatorów ciepłego powietrza. Jak już wspomniano w tekście głównym, zawór RTB blokuje przepływ powrotny z wentylatora powyżej 45 do 50°C. Wynikający z tego wzrost różnicy ciśnień zapewnia, że objętość wody obiegowej w obiegu wentylatora jest dławiona za pomocą sterowanej pompy o wysokiej wydajności - przy stałej delcie T.
Dolny rCOL 3×8 - 2 jest w zasadzie tylko rozdzielaczem. Zamontowane są na nim dwa typy DN25 3×2 VL 5. Trzy razy dwa oznacza: trzy połączenia przychodzące (2 - 7 - 1) i dwa połączenia wychodzące (6 - 5). Dodatkowa cyfra 5 oznacza jedynie pompę cyrkulacyjną, która może być podłączona kołnierzowo bezpośrednio do przepływu (5).
Po prawej stronie, trzeci szary prostokąt oznaczony jako sBox DN25 2×2 VL 3wskazuje niesterowany obieg grzewczy do podgrzewania ciepłej wody użytkowej (rezerwa). W razie potrzeby może to być również realizowane przez kocioł o mocy 700 kW. Zespół zawiera pompę obiegową z hamulcem grawitacyjnym, termometry i funkcję zaworu odcinającego, ale doprowadza swój przepływ powrotny do środkowej komory rozdzielacza, dzięki czemu jest on połączony z przepływem powrotnym nagrzewnicy powietrza 50 kW i pozostaje oddzielony od przepływu powrotnego grzejnika 30 kW.
Podgrzewacz ciepłej wody o pojemności 1000 litrów (rys. 2) jest ogrzewany albo przez określony olejowy kocioł kondensacyjny Vaillant (icoVIT) o mocy 19 kW, albo alternatywnie przez kocioł Viessmann o mocy 700 kW, który zasila również obieg wentylatora. "Alternatywa" w tym kontekście opiera się na obecnej sytuacji operacyjnej. Podczas gdy główny kocioł wytwarza ciepło dla obiegu wentylatora, może on również ładować zbiornik magazynowy. Planowanie uwzględniło również ogranicznik temperatury powrotu w tym schemacie, aby zapewnić zarówno działanie kondensacji w kotle Vaillant, jak i stabilizację hydrauliki w głównym obiegu - jeśli generator ciepła Viessmann obsługuje cylinder - przy wspomnianych 45 do 50 °C.
Nowa wytwornica pary zasilana olejem opałowym nie ma już nic wspólnego z podgrzewaniem wody. Zasila ona jedynie zbiorniki mieszające podczas pracy i w ten sposób dostosowuje swoje godziny pracy do rzeczywistego zapotrzebowania na parę, wykorzystując zasadę niskowodnego, a tym samym energooszczędnego przepływowego podgrzewacza wody (typ Clayton EO-10, moc 100 kW, ciśnienie robocze regulowane do 7 barów, produkcja pary przy 1 barze 157 kg/h), co również minimalizuje straty w trybie gotowości.
Krótko mówiąc, technologia hydrauliczna i zasilająca dla trzech obiegów ogrzewania, gorącej wody i pary lub czterech z elektrycznym przepływowym podgrzewaczem wody w laboratorium bez ochrony przeciwwybuchowej. Już przebudowany plan generalny zapowiadał znaczne zmniejszenie zużycia energii.
Optymalizacja za pomocą kolektorów mieszających
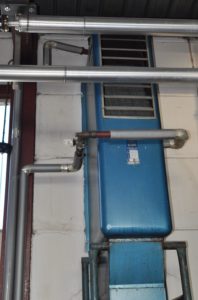
Rysunek 7: Istniejące wentylatory nie zostały wymienione, ale zostały przystosowane do kondensacji z zaworami termostatycznymi jako ogranicznikami temperatury powrotu.
Ponadto, udoskonalenie systemu ogrzewania w zakresie inżynierii sterowania powinno również przynieść oszczędności. Długi tytuł tego działania brzmi: "Optymalizacja systemu grzewczego w Chemoplast NV - wydajna praca zmniejszonego systemu kotła kondensacyjnego poprzez konwersję na trójkomorowy rozdzielacz z wykorzystaniem powrotu dla dwóch kontrolowanych obiegów grzejników z "rendeMIX" i S-Box do ładowania zbiornika ciepłej wody". Za tym wszystkim stoi specjalny system hydrauliczny firmy HG Baunach GmbH & Co. KG oparty na wieloportowym rozdzielaczu mieszającym "rendeMIX". Umożliwiają one szeregowe połączenie obwodów wysoko- i niskotemperaturowych, zamieniając powrót obwodu wysokotemperaturowego w przepływ obwodu niskotemperaturowego, przy czym wewnętrzne i zewnętrzne sekcje wyrównawcze instalacji "rendeMIX" prawidłowo równoważą poszczególne objętości wody.
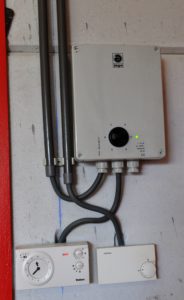
Rysunek 8: ... i z przetwornicami częstotliwości do sterowania prędkością wentylatora
Proces ten sprawdził się już kilka tysięcy razy w budownictwie mieszkaniowym, umożliwiając połączenie grzejników (wysokotemperaturowych) z ogrzewaniem podłogowym (niskotemperaturowym). Po pierwsze, zapewnia to duży rozrzut temperatur, a tym samym co najmniej o połowę zmniejsza objętość wody w obiegu. Po drugie, chłodna woda powrotna, która często ma temperaturę znacznie poniżej 30°C. oC w kondensacyjnym wymienniku ciepła kotła, spaliny są schładzane do temperatury znacznie poniżej punktu rosy, dzięki czemu ciepło utajone nie jest tracone. Kocioł kondensacyjny może spełnić swoje zadanie polegające na wykorzystaniu ciepła kondensacji do celów grzewczych tylko wtedy, gdy temperatura powrotu jest odpowiednio niska.
Dwa złącza powrotne
W Chemoplast NV w Europark, we Flandrii, sterowany pogodowo obieg wentylatora jest obiegiem wysokotemperaturowym. Ściśle rzecz biorąc, olejowy kocioł kondensacyjny składa się tutaj z dwóch komponentów, kotła o wartości opałowej i oddzielnego wymiennika ciepła utajonego w kanale spalin. Firma HG Baunach GmbH & Co. KG wybrała tę kombinację, aby móc pracować z dwoma przyłączami powrotnymi, jednym na kotle, a drugim na skraplaczu. Zaletę tych dwóch przyłączy powrotnych można wyjaśnić w następujący sposób:
Przede wszystkim należy zauważyć, że wentylatory w halach fabrycznych - nie zostały one wymienione, ale ich prędkość została ograniczona - były zasilane ogromną ilością wody do 85 litrów przez rurę w NW 100. oC. Ta sterowana pogodowo temperatura musi być w stanie osiągnąć ten poziom, aby wygenerować wystarczającą ilość ciepłego powietrza. Ponadto firma Karremans zainstalowała zawór termostatyczny jako ogranicznik temperatury powrotu bezpośrednio za każdym z około 30 wentylatorów. Jego termopara zamyka zawór, jeśli temperatura powrotu wzrośnie powyżej 45-50°C z powodu niewystarczającego poboru ciepła. oC wzrasta. Związane z tym dławienie wysyła sygnał do sterowanej pompy cyrkulacyjnej poprzez zwiększoną różnicę ciśnień, aby odpowiednio dostosować natężenie przepływu, tak aby pozostałe wentylatory pozostały nienaruszone.
Obwód ten zaczyna się i kończy w kotle kalorycznym. Przepływ powrotny z wyżej wymienionymi 45 do 50 oC nie pozwala na wykorzystanie kondensacyjne, ponieważ punkt rosy oleju opałowego EL wynosi 48 oC. Ponadto kondensacja nie może mieć miejsca w kotle o wartości opałowej ze względu na jego konstrukcję, ponieważ ta część kotła nie jest do tego przeznaczona i dlatego ma zalecane zwiększenie przepływu powrotnego ze względów bezpieczeństwa.
Chemoplast NV
W latach 70. belgijski rząd zamknął kopalnie węgla w Limburgii. Aby to zrekompensować, kraj promował industrializację w regionie. Oczywiście podaż nie mogła zaspokoić popytu na pracę. Z kolei rynek pracy w Niemczech w tym czasie charakteryzował się odwrotną sytuacją. Republika Federalna budowała się, cud gospodarczy kwitł i wszędzie brakowało siły roboczej. Niemiecki przedsiębiorca z Bergisch-Gladbach, który od 1936 r. produkował pasty do polerowania samochodów i inne produkty do czyszczenia zewnętrznego i wewnętrznego pojazdów, przeniósł swój zakład produkcyjny do Houthalen. Było tam wystarczająco dużo siły roboczej, poziom płac był odpowiedni, a dla dostaw w całych Niemczech i Europie nie miało znaczenia, czy ciężarówki dostarczały towary z Kolonii lub Bensbergu do Francji lub Portugalii, czy też z Limburga w Belgii. Administracja i operacje pozostały w Niemczech.
Kiedy niemieccy kierowcy samochodów przestali myć swoje ulubione dziecko, karoserię samochodu, starannie ręcznie za pomocą skóry i suchej szmatki, a myjnie samochodowe zastąpiły produkty do mycia ręcznego, Chemoplast NV rozszerzył swoją ofertę o produkty czyszczące dla przemysłu, kolei i firm przewozowych. Prawie wszystkie pociągi w Holandii, w tym pociągi podmiejskie, korzystają z produktów Houthalen. Wiedeńskie pociągi podmiejskie i metra również zyskują świeży blask dzięki produktom "Starcare" z Limburga, podobnie jak lokomotywy Siemensa Kolei Transsyberyjskiej i rosyjskiej kolei dużych prędkości z Petersburga do Moskwy.
W 2012 roku Chemoplast NV nabył wiedzę, receptury i licencje firmy, której klientami są producenci samochodów. Zarządzanie jakością obejmuje dokładne czyszczenie robotów lakierniczych po każdej zmianie koloru. Odbywa się to przy użyciu specjalnego rozpuszczalnika w różnych kombinacjach. W wyniku tej ekspansji niemiecko-belgijska firma przewiduje wzrost obrotów o 30 do 40 procent w nadchodzących latach. Firma jest również w trakcie zdobywania coraz większej pozycji jako dostawca OEM dla producentów środków czyszczących, którzy chcą utrzymać swoje moce produkcyjne na podstawowym poziomie.
Gwarantowana wartość opałowa
85 do 90 procent dostarczanego ciepła jest wymagane przez wentylatory, 10 do 15 procent przez grzejniki w pomieszczeniach biurowych oraz w pomieszczeniach sanitarnych i szatniach. Rozrzut projektowy 60/40 jest wystarczający dla tych generatorów ciepła oC. To połączenie nie oznacza nic innego niż to, że przez większość okresu grzewczego przepływ powrotny jest o kilka lub wiele stopni poniżej limitu 40°C. oC jest przesunięty. W związku z tym do skraplacza dopływa tylko czynnik powrotny z chłodnicy. Obniża to temperaturę spalin średnio do 33-35 oC. Wymiennik ciepła utajonego jest zatem w stanie wydobyć dużą część z prawie 10% energii resztkowej ze spalin, która bez niego wydostałaby się przez komin.
Jednak opisana strategia powrotu z wykorzystaniem wartości opałowej działa tylko z mieszalnikami "rendeMIX", zarówno jako sprzęgło między dwoma obiegami grzewczymi, jak i jako rozdzielacz przepływu. Hydraulika systemu grzewczego w Chemoplast NV jest taka, że częściowa objętość strumienia powrotnego o wyższej temperaturze z obiegu wentylatora zasila obieg chłodnicy o niższej temperaturze. Jeśli wymaga to temperatury zasilania 60°C w głębi zimy, rendeMIX podnosi temperaturę źródła od 45 do 50°C poprzez zmieszanie z gorącą wodą kotłową z obiegu wentylatora. Jednak przez większość sezonu grzewczego pomieszczenia ogrzewane grzejnikami powinny być w stanie zadowolić się wodą z wentylatora o temperaturze od 45 do 50°C, którą w razie potrzeby można obniżyć, dodając własną wodę powrotną.
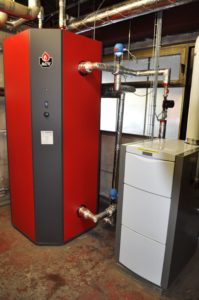
Rysunek 9: Olejowy kocioł kondensacyjny o mocy 19 kW (Vaillant icoVIT) do całorocznego podgrzewania ciepłej wody użytkowej
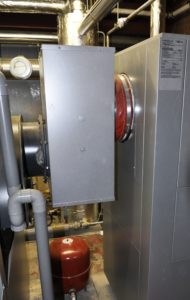
Rys. 10: Zewnętrzny wymiennik ciepła utajonego za kotłem olejowym (po prawej, Viessmann Vitotrans) umożliwia podłączenie oddzielnego powrotu ogrzewania, a tym samym wykorzystanie kondensacji przy wysokich temperaturach zasilania (objaśnienie w tekście). Srebrnoszara skrzynka spalin pomiędzy wymiennikiem a kotłem po prostu kompensuje różne wysokości wylotu kotła i wlotu wymiennika ciepła
Całe spaliny opuszczają system kotła olejowego poprzez zamontowany kołnierzowo skraplacz. Jeśli chodzi o technologię zasilania, działa to jako generator ciepła dla grzejników - w wyniku czego sam przyrost wartości opałowej jest wystarczający do pokrycia dużej części zapotrzebowania na ogrzewanie pomieszczeń socjalnych i biurowych.
Remont rozpoczął się 6 lat temu
W 2007 roku Werner Sauer doszedł do wniosku, że trzeba coś zrobić. W listopadzie rozpoczął rejestrowanie danych dotyczących obu generatorów ciepła, a następnie latem 2008 r. podjął pierwsze działania hydrauliczne, takie jak instalacja promiennikowych paneli sufitowych, modernizacja ograniczników temperatury powrotu i instalacja sterowanej pompy o wysokiej wydajności. W 2009 r. ocena danych pomiarowych ujawniła ogromne przewymiarowanie kotła i wytwornicy pary, a latem 2010 r. zakończono prace związane z przebudową sieci hydraulicznej, instalując regulatory prędkości nagrzewnic powietrza. Same te działania nie tylko doprowadziły do zmniejszenia rocznego zapotrzebowania na olej opałowy ze średnio około 60 000 litrów do 50 000 litrów oleju opałowego, czyli około 15%, ale także zwiększyły deltę T obwodu wentylatora z początkowych 2K do przyzwoitych 20K. Według Hansa-Georga Baunacha dopiero teraz stworzono warunki wstępne do dopracowania i realizacji planów konwersji na kocioł kondensacyjny oparty na zapotrzebowaniu i kondensacyjny system dystrybucji ciepła. Sygnał startowy został wysłany wiosną 2011 roku, gdy stary generator pary przeciekał: operacja awaryjna wymiany kotła, w tym dystrybucja ciepła, przygotowanie ciepłej wody i wytwarzanie pary, została przeprowadzona w okresie grzewczym, ale kompletny system sterowania został uruchomiony dopiero wczesnym latem 2012 roku. W oparciu o odstępy czasowe między napełnieniami zbiornika, można było przewidzieć dalszy "zysk" w wysokości od 20 do 25 procent po zaledwie kilku miesiącach, tj. dalsze zmniejszenie zużycia oleju opałowego ze średnio 50 000 do 40 000 litrów rocznie.
Dziś 40 000 zamiast 60 000 litrów oleju opałowego
Zakres ten prawdopodobnie nie będzie jeszcze maksymalny, ponieważ nadal istnieje potencjał optymalizacji, szczególnie w zakresie ustawień systemu sterowania. "Zakładam, że ostatecznie nie tylko zaoszczędzimy ponad jedną trzecią oleju, ale także znacznie zmniejszymy zużycie energii elektrycznej, ponieważ sterowana pompa o wysokiej wydajności może w pełni rozwinąć swój efekt tylko dzięki instalacji ogranicznika temperatury powrotu", wyjaśnia Hans-Georg Baunach.
Zawory termostatyczne jako ograniczniki temperatury powrotu, w połączeniu z pompą sterowaną różnicą ciśnień, zapewniają równoważenie termiczno-hydrauliczne: Jeśli zawór dławi przepływ z powodu zbyt wysokiej temperatury powrotu, temperatura powrotu pozostaje stała, nawet jeśli wentylatory nagrzewnic powietrza są wyłączone za pomocą elektrycznych termostatów pokojowych. Zmniejsza to jednak moc cieplną podczas pracy wentylatora, co prowadzi do "zimnych przeciągów", jeśli prędkość wentylatora pozostaje wysoka. Jednakże, o ile nadal można zapewnić wymaganą moc cieplną, zmniejszenie prędkości wentylatora ma następujące zalety:
- Wyższa temperatura wylotu powietrza
- Mniejsza prędkość powietrza, a tym samym mniejsze zanieczyszczenie pyłem
- Mniejsza emisja hałasu
- Bardziej równomierne wykorzystanie powierzchni grzewczych.
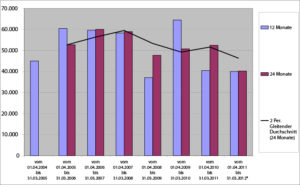
Rysunek 11: W odniesieniu do roku bazowego 2007 (lata od 1 kwietnia danego roku do 31 marca następnego roku), roku przed rozpoczęciem prac renowacyjnych, renowacja hydrauliczna w latach 2008-2010 doprowadziła już do zmniejszenia zużycia oleju opałowego z 60 000 litrów do 50 000 litrów. Późniejsza wymiana starego systemu na nowoczesny olejowy kocioł kondensacyjny (uruchomiony w grudniu 2012 r.) pozwoliła zaoszczędzić kolejne 10 000 litrów oleju opałowego. Konsultant Hans-Georg Baunach i konstruktor systemu Karremans "nie uważają tego za koniec historii" (Baunach). Przewidują jeszcze większy wzrost wydajności pod koniec tego okresu grzewczego, pierwszego, w którym ogrzewanie będzie w całości dostarczane za pomocą nowego systemu, w tym sterowania.
Szachy niechlujnej hydrauliki
Zwłaszcza ostatni punkt nie powinien być lekceważony pod względem wydajności systemu: Im bardziej równomiernie całe ciepło przepływa przez wąskie gardło wszystkich powierzchni grzewczych, tym niższa jest niezbędna delta T między wodą a powietrzem. Ma to szczególnie silny wpływ na temperaturę powrotu, a tym samym na efektywność wykorzystania kotła kondensacyjnego. Decyzja o tym, czy kocioł przejdzie w tryb kondensacji, czy nie, jest zwykle podejmowana po stronie systemu.
Hans-Georg Baunach podsumowuje: "Pod względem technologii grzewczej wiele zakładów przemysłowych jest prawdopodobnie nieużytkami. Spójrzmy na to w ten sposób, każde zaoszczędzone 100 litrów oleju opałowego zmniejsza obciążenie atmosfery o około 250 kg dwutlenku węgla. Wystarczy wyobrazić sobie te liczby. Gdyby ustawodawca rygorystycznie regulował lub promował stare zasoby w tym obszarze, Niemcy i UE mogłyby z łatwością osiągnąć wszystkie cele z Kioto. Jest rzeczą oczywistą, że my, branża grzewcza, nie możemy ryzykować naszej reputacji. Nie możemy pozwolić, aby kotły kondensacyjne działały głównie w trybie wartości opałowej. My, producenci i dostawcy komponentów, oferujemy wszystkie techniczne możliwości optymalizacji hydrauliki w połączeniu z planowaniem".
Zmierzone zużycie energii w budynku
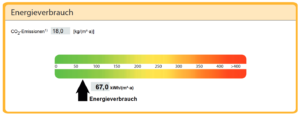
Rys. 12: Przebieg energetyczny pokazuje: przy ogrzewanej powierzchni 6000 m², rocznym zużyciu oleju opałowego na poziomie 40 000 litrów przy zużyciu energii 67 kWh/m²-a) i emisji CO2 na poziomie 18 kg/m²-a praktycznie odpowiada standardowi domu niskoenergetycznego - dla budynku z lat 60-tych z wymuszoną wentylacją w obszarze roboczym chronionym przed wybuchem!
Chemoplast NV Houthalen (Belgia)
Wielkość inwestycji: 240 000 EUR
Oszczędność kosztów: 12 000 euro
Przepływy pieniężne: 5%
HG Baunach GmbH & Co. KG
E-mail: info@baunach.net
Strona główna: www.baunach.net