Not off the peg
Model character: The heating technology at R + F in Kassel
The company's credo: "The future lies in innovative, modern technologies. We have to deal with these and pass on our knowledge to our clients - craftsmen, planners, architects. Of course, we can argue particularly convincingly if we have our own experience, for example with regard to the energy savings of old versus new." Markus Ortlauf, who says this, is technical advisor to the Wholesale house Richter + Frenzel. He had spoken out in favour of an unusual heating installation in the wholesaler's Kassel property.
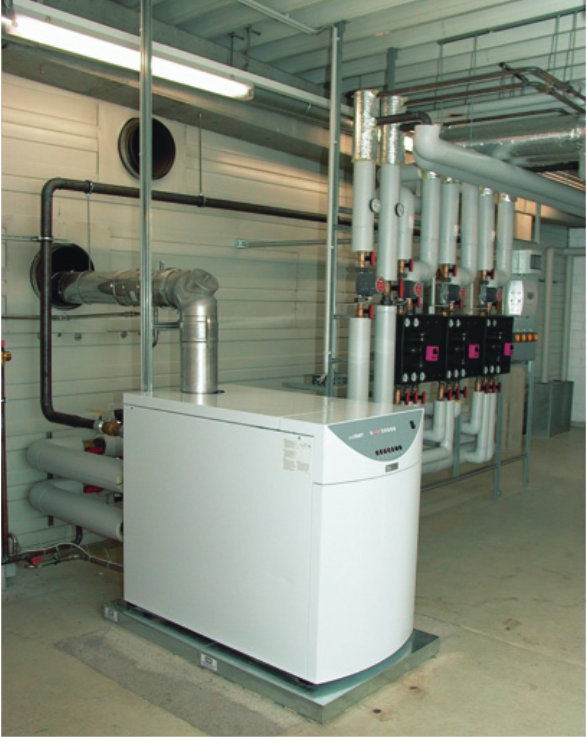
Figure 1: Ecocraft heating system in the technical/training room at R + F in Kassel.
The operating results after a good year have rewarded him and his house for the not entirely risk-free decision. At the heart of the renewed technology is the "Ecocraft" modular boiler from Vaillant. In the meantime, the older atmospheric boilers in the northern Hesse branch of R + F had struggled to achieve acceptable utilisation rates and were to be replaced. However, it could not be standard goods, because in Hesse, the motherland of Viessmann and Buderus, you have to hold a few trump cards in your hand if you want to hold your own as a supplier of heat generators alongside the two powerful competitors. Markus Ortlauf saw one of the trump cards in the "Ecocraft" gas condensing cascade boiler. Cascade means: the unit consists of self-sufficient modules flanged together in parallel, each module with an output of up to 40 kW. The smallest unit consists of two cells, the largest of seven. This provides an output of up to 280 kW, depending on the object. Each individual burner can also be controlled between 12 and 40 kW, which means that the control range is from 12 to 280 kW.
Disturbance without noticeable consequences
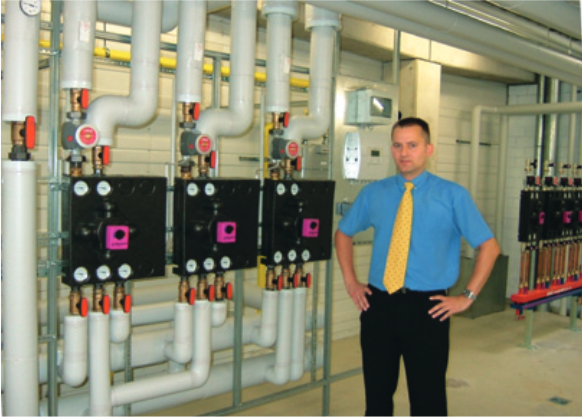
Figure 2: The distribution piped on site with the rendeMIX mixers (to the left of R + F employee Stefan Dornemann and a parallel model installation for training purposes with Magra distributor in the background.
Self-sufficient means: If one of the blocks in the cascade malfunctions, its neighbours work for it. The boiler does not fail. The failure is not noticeable to the outside. The "Ecocraft" is thus similar to a solid diesel, which can also cope with the failure of a cylinder. Ortlauf: "This special feature of the model gives us the chance to play a stronger role with Vaillant in the boiler business. Of course, we also have to communicate this. That's why we immediately expanded the technology room with the 'Ecocraft' into a training centre." As a second trump card, which speaks above all for the planning and consulting competence of the Richter + Frenzel field service, the Kassel branch points to the special circuitry of the three heating circuits of the building complex in combination with the "rendeMIX" system of the company HG Baunach GmbH & Co. KG from Hückelhoven on the German-Dutch border. This switches high-temperature and low-temperature networks in series, i.e. turns the return of one heat distribution system into the flow of the other, thus optimising the energy yield, especially in combination with condensing boilers. About five years ago, this architecture based on a very special multi-way mixer came onto the market as a heart. In the meantime, it has passed its test in numerous references, i.e. it has proven its savings effects: because it guarantees the lowest return temperatures and thus the highest condensation heat gains.
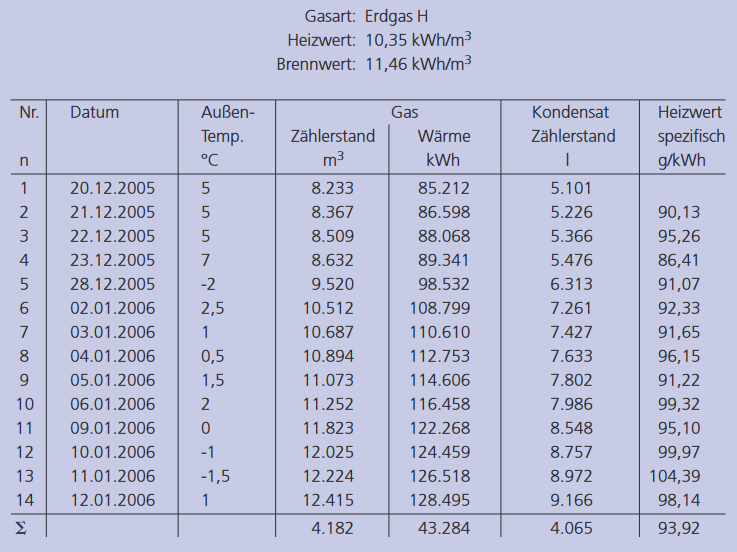
Figure 3: Table of values.
Three circles as one circle
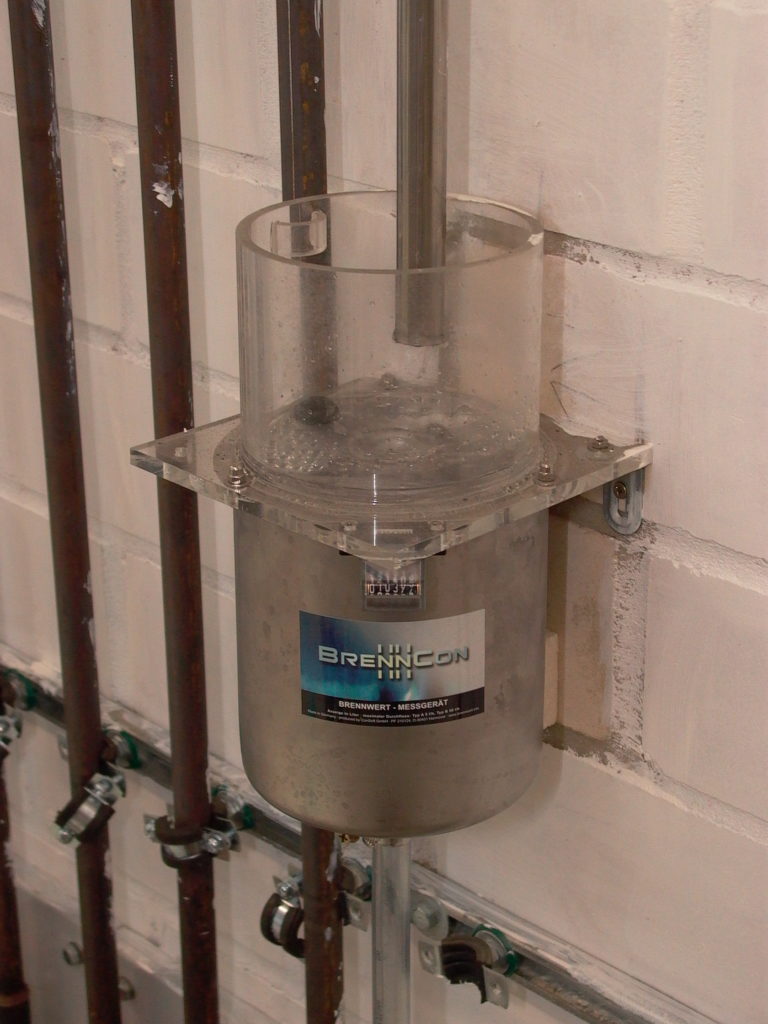
Figure 4: Condensate measuring device BrennCon www.consoft.de.
In Kassel, the "rendeMIX" found a particularly exciting terrain, namely three temperature zones: firstly, the administration complex as a radiator circuit with a flow temperature of about 60 °C, secondly, the exhibition with underfloor heating for a maximum of 40 °C and thirdly, finally, the warehouse with coils in the floor for a flow temperature of up to 30 °C as well. In principle, this third section is only to be kept frost-free. The system scheme is therefore based on the following spreads: Offices 62/42 °C, Exhibition 40/30 °C, Warehouse 30/20 °C. With "rendeMIX", practically the entire complex is heated as a single-circuit design. In the past of the two atmospheric old boilers, three mixers mixed three temperatures for each subarea, and the common return therefore never dropped below 42 °C. The system went into operation at the beginning of the 2005/2006 heating season, and a few weeks later in spring the training courses for craftsmen and planning offices on "Ecocraft" and "rendeMIX" started. The first training courses had to make do with selective results from reality in addition to explaining the functions. How temperature-stable and with which degrees of utilisation the individual volume flows moved through the pipe coils, through the radiators and through the heat exchangers of the "Ecocraft" could only be read from momentary thermometer values and from the balance of a few weeks, but not from the balance of two heating periods as a before-and-after comparison. Such an evaluation is now available. In the two years before "Ecocraft" and "rendeMIX", in the years from July 2003 to June 2004 and in the same period from 2004 to 2005, the heating energy consumption at Richter + Frenzel in Kassel was 506 000 and 499 000 kWh respectively. In time for the winter of 2005/2006, the local heating contractor, Günter Tromp Haustechnik, Kassel, installed the modular Vaillant heat generator and connected the three heating circuits in series with the Baunach fitting. The result: only 356,000 kWh. This value is not weather-adjusted, but read from the gas meter. However, this does little to change the proportionality, as the climate data did not differ greatly in these three years.
Now Magra distributor for rendeMIX
If you take a look at the installation at Richter + Frenzel, you will notice that the piping of the individual mixer groups is still very complex. That was expensive. In the case of Richter + Frenzel, this did not play a major role in the decision because, firstly, they wanted to set up a demonstration plant and, secondly, they were already negotiating with the fittings manufacturer Magra to weld a special distributor for the "rendeMIX". This would later reduce the costs in the commercial business and thus make the special architecture of the series connection more attractive in terms of costs and installation. Magra and Baunach presented the fitting at the Essen SHK in 2006. It combines the "rendeMIX" scheme with the principle of the familiar manifold. What is special about it, however, is that three connections are provided per mixer group and not two, as in the standard version, namely hot flow, hot return, cold return. The manifold allows up to five groups to be connected. To avoid confusion, the individual couplings are clearly marked. The only thing that needs to be taken into account is the order in which the heating circuits are connected to the heat generator with decreasing return temperature. Otherwise, there is no difference to the proven Magra system.
Proven to save 30 per cent
The modern boiler and the heating circuit arrangement thus reduced the natural gas costs by around 30 percent. Roughly speaking, two thirds of this success can be attributed to the heat generator and the third third to the system design. To realise this, HG Baunach GmbH & Co. KG had to do some convincing with the planner and Vaillant. If you look at the three individual spreads and add in some tolerances, the total spread adds up to 40 K. Vaillant initially did not want to impose this difference between flow and return on the heat generator, for fear that a single module might suffer from a lack of water under unfavourable conditions. The Remscheid-based company originally insisted on an overflow, on a hydraulic separator. This is because the Ecocraft belongs to the family of recirculating water heaters, which require minimum flow rates. The technicians solved this problem from the system side. They set up a control hierarchy that is balanced in such a way that individual circuits always guarantee the minimum circulating water flow when the modules are in operation, i.e. they do not regulate down completely. The three temperature levels at Richter + Frenzel make do with a total of 200 kW. The training/technology room therefore has an Ecocraft with five modules (5 x 40 kW). The operators counted the starting frequency and determined an average boiler running time of 2.5 days per start. Now this should not be a particularly surprising value for a modulating heating system that can run down to a few kilowatts. In a severe winter, heat demand and heat output would have to balance each other out and the system would virtually run through, but viewed over an entire heating period, 2.5 days speaks for a very solid system configuration.
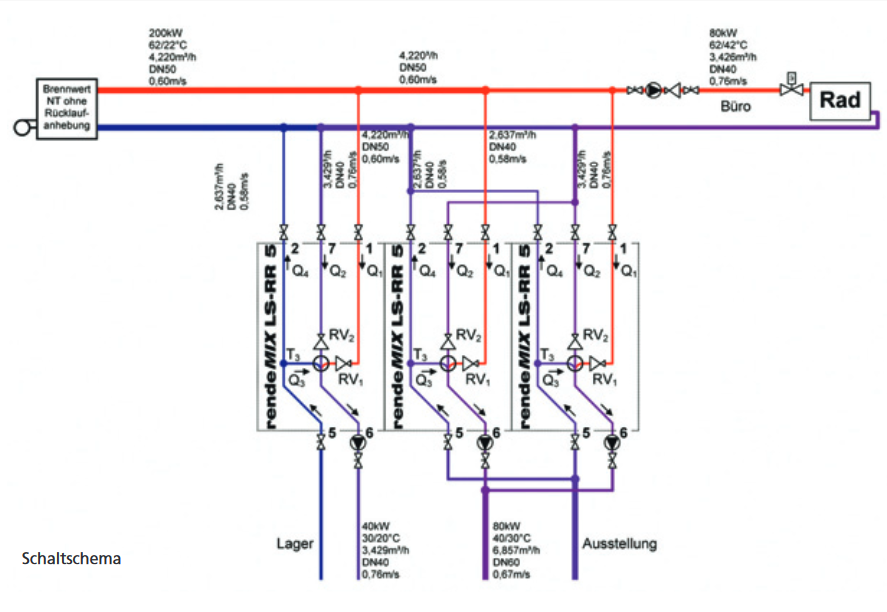
Figure 5: Circuit diagram.
High calorific value utilisation
This is also expressed in the utilisation of the calorific value. Manufacturers promise utilisation rates of 105 percent as a rule. But there is often a considerable gap between theory and practice or between the test bench and the field. This has something to do with return temperatures that are too high. At a value of about 40 °C, one third less condensate is produced compared to the "gain" at 20 °C. The result is a lost five percent. In the end, this amounts to a lost five percent efficiency. In the Richter + Frenzel branch, because of the triple use of the flow down to 20 °C, there should actually be no differences between the planned and measured condensation heat yield. However, the consultants and training managers wanted to be able to rely on verifiable evidence here as well and suggested the installation of a BrennCon measuring device. This will purge the condensation water. In principle, it is a condensate collector of defined content, which empties one tankful at a time into the wastewater network and determines the condensate volume from the addition of the strokes. The recalculation by Richter + Frenzel revealed highly satisfactory results: the gas consumption of 4182 m3 or 43 284 kilowatt hours in the period 20.12.2005 to 12.01.2006 are compared with a specific 94 g/kWh of condensate. From this, Fig. 3 shows an average return temperature of about 33 °C and a thermal efficiency of the boiler in the period under consideration of 104 percent. With a return temperature of 42 °C - as in the past - the "Ecocraft" would have had to make do with around 4 % less efficiency - and would thus have given away a lot.
Some improvements
At least 16,000 kilowatt hours were wasted. In the first weeks of commissioning, the system was still based on older control software that was not tailored to the three-circuit architecture. Vaillant made improvements. Figure 3 also attests to the success: from January onwards, the condensation levelled off at about 98 g/kWh, which means at least another half a percentage point more or 2000 kWh. Another initial shortcoming: an installation error had crept in. This was probably to the detriment of the system's energy efficiency number as defined by the Energy Saving Ordinance. Unfortunately, as it turned out later, one of the outdoor sensors was permanently reporting frost temperatures. The result: even in mild weather, the supply flowed into the radiators at the boiler temperature, which was limited to a maximum of 67 °C. The system still had one return flow. Although the return flow remained at 30 °C, according to DIN 4701 Part 10 "Energetic evaluation of heating and ventilation systems" the heat loss of the heat distribution increases with rising system temperature. However, since the majority of the distribution level in Kassel is located within the thermal envelope of the building, the losses are likely to have had only a minimal effect in euros and cents.