Increased profit
Renovation of heating technology using the example of Chemoplast NV
It is likely that the EU and Germany could Kyoto targets if all manufacturers regularly looked at their energy costs - and were able to classify them. Admittedly, the big ones do it, the medium-sized companies less so. Example: A German entrepreneur with a business in Belgium recently shook his head in surprise. The results of the renovation of his Cologne home had opened his eyes to what he had probably been giving away for years in Limburg, Flanders.
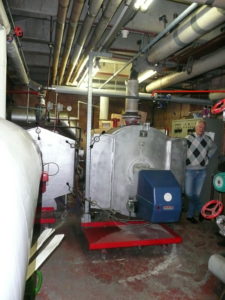
Photo 1: Oversized old plant with approx. 400 kW steam generator and 1.4 MW boiler. On the right, Chemoplast owner Werner Sauer.
Anyone who promises and sells condensing efficiency should also guarantee it. In other words, the hydraulics should be finely adjusted so that the flue gas actually condenses out its latent heat. By switching from calorific value to condensing value, the system manufacturer usually eliminates gross network faults, but often fails to recognise how to make intelligent hydraulic connections. As a result, valuable potential usually remains unrecognised and unused.
At the beginning there is the analysis of the current situation
Experienced companies and planners therefore do not rely on what is printed in the documents for extensive complexes. They connect measuring devices and check pressure and flow. In the renovation of the existing building, they cannot do without this data collection anyway, if they do not want to carry over the mistakes of the past into the retrofit. The mistakes of the past usually consist of oversized pipes, pumps and fittings. These compensated cheaply for the control weaknesses at times of a few pfennigs per kilowatt hour - no matter how energy-intensive the company may have been.
For years, entrepreneur Werner Sauer had also not given much thought to the efficiency of the energy generation systems in his detergent business. Although his detergents clean all the suburban trains of the Vienna public transport company, the Siemens trains on the Trans-Siberian route or the painting robots of the automotive industry - which have to be thoroughly rinsed after every colour change - "we didn't have much of a problem with keeping the air clean, as one would say today with climate awareness", admits the owner of Chemoplast NV in Houthalen in Limburg, Belgium.
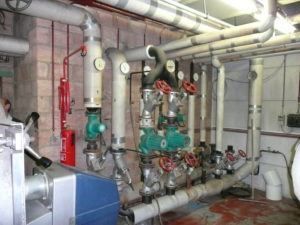
Figure 2: Old heat distribution
The factory, including its technical building equipment, dates back to the 1960s. The need for an all-round energetic renovation became apparent to the Rhinelander after the renovation of his private house. The Cologne architect Wilhelm Riphahn, representative of the "New Building" in the tradition of the Bauhaus style, who enriched the panorama of the cathedral city in the 1920s with the "Bastei" on the Rhine and in the 1950s with the opera house, had drawn a kind of residential tower as a home: with partially rounded windows in single glazing, which could only be replaced with insulating glass at infinite expense, with thick monument protection for the relatively thin-skinned exterior façade and with high-temperature radiators to provide heat.
The hidden cost driver
At some point, Hans-Georg Baunach, friend and advisor to the owner of the house and developer of the "rendeMIX" mixers, cut off the high-temperature circuit from the bathrooms, which in the meantime had been equipped with underfloor heating, and other partial areas. Baunach's multi-way mixers optimised the hydraulics in the Riphahn design. When the balance sheet after the first cold winters showed that the conversion had noticeably relieved the natural gas bill, these savings pointed Werner Sauer to his failings at the factory in Belgium. He had shaken his head over the operating costs there every month, but had taken them for granted. In a production plant with many positions, they were not recognisably a cost driver. There had been no shortage of heat, not of hot water. Why question the technology.
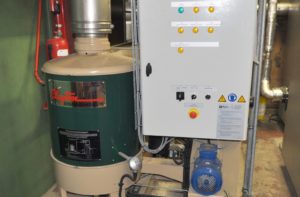
Fig. 3: Renewed fuel oil-fired steam generator (continuous flow principle) for heating the mixing vessels in production as required, steam production at 1 bar 157 kg/h
In his renovated Cologne house, however, he discovered what he was probably giving away from year to year in Houthalen. Of course, the as-is analysis in Flanders revealed the typical problem with old buildings. There was a lack of documents, of exact figures, of circuit diagrams. "We were confronted with an oil-fired boiler, the output of which we only researched afterwards. The nameplate had disintegrated. Later it turned out to be 1.4 megawatts. We also found nothing in the documents about the oil-fired steam generator. After some calculation and reflection, it delivered an estimated 400 kW. As for the hot water required for production, we were only told, 'We need huge quantities of at least 80°C'. What that meant in concrete terms remained vague," the factory owner looks back.
Operating hours and pulse counter
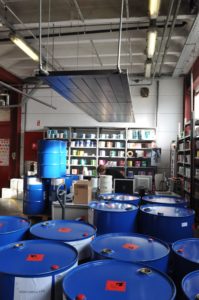
Fig. 4: Hot water heated radiant ceiling panels instead of hot air in the forced-ventilated work area
"Now, of course, all this comes from a time when energy cost little. Specifically, heating oil. Belgium is an oil country. Dutch natural gas doesn't flow, it just trickles across the border. In other words, given the cheap oil supply, we did little to estimate the individual consumers. There were no meters anywhere." When he asked Hans-Georg Baunach to come to Limburg after the refurbishment in Cologne in October 2007, the very first thing he recommended was to install operating hour and pulse meters on the steam generator and the boiler. On the one hand, the steam generator kept the double-walled vats in production at operating temperature and, on the other hand, it served the continuous flow heater for hot water preparation. This hot water, in turn, had to be constantly available at a fairly high temperature in order to spontaneously add a high-temperature 300 to 700 litres to the chemicals and powders in the stirred tanks at unscheduled times.
The heated production area comprises 6,000 m2Some of them are forcibly ventilated for explosion protection reasons. Only explosion-proof equipment may be installed in hazardous areas. On the heating side, hot-air blowers were the obvious choice, then as now. Their water/air heat exchangers were fed by the old and the new oil boilers via a single line of flow and return, which leaves the boiler room in nominal width 100 and branches out widely over the various buildings.
Burner running time one single minute
"On the one hand, we established through the measurements that the heating boiler did not reach even 50% utilisation at any time during two heating periods, while the steam boiler only covers its standby losses with the majority of its fuel. On the other hand, it was obvious, also through complaints from the employees, that it makes no sense at all to heat draughty parts of these work areas with tempered air as in the past. The ventilation carried the heat away immediately. The permanent re-circulation had to cost an immense amount, without our having calculated it in detail. Instead of ventilation, we therefore had radiant ceiling panels installed directly above some workplaces. This way we now heat the critical zones via radiation. These panels are also supplied by the common flow of the oil boiler," says Hans-Georg Baunach, describing one of the earlier energy sins and the remedy.
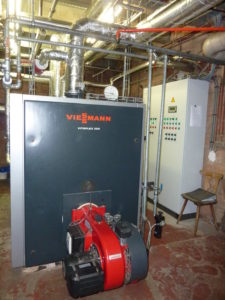
Figure 5: Up to 85 °C flow temperature from the oil condensing boiler (Viessmann Vitoplex) with 700 kW output
Back to the actual analysis, the operating hours and the number of cycles: The oversizing of the old boiler (as it turned out later, 1.4 MW) was beyond imagination. Even in the thickest winter, it took long breaks and when it did run, it ran for between one and ten minutes at the most. Nevertheless, the staff at the workplaces literally showered in warm air.
Instead of the inefficient oil heating value system, a 700 kW oil condensing system (Viessmann) now supplies the heating water consumers. In order to work efficiently even in partial load operation, it was equipped with a two-stage Weishaupt burner.
Welded seam as emergency dressing
Superfluous losses were also caused by smaller network sections. The circulation to the hot water tap at the sporadically used washbasin in the laboratory a hundred metres away pumped hot water for 24 hours, and the low-pressure steam generator in the form of a colossal old cast-iron boiler stood uselessly under steam most of the time, only to be able to supply sporadically used heat at any time. Until it finally showed cracks. It had to remain in service for a few weeks with an emergency bandage in the form of a weld before a unit less than half its size replaced it.
Further measures in brief: plant builder Karremans NV from Zonhoven, Belgium, cut the pipe to the distant laboratory and screwed a separate electric instantaneous water heater under the sink. For the factory's hot water supply, he set up a relatively modest jacket-heated 1,000-litre storage tank with a separate oil condensing boiler of now only around 20 kW (Vaillant).

Figure 6: "rendeMIX" station. Function see box "Scheme heating
Since production only taps twice a day, the 20 kW have four hours to recharge the storage tank. At the same time, the boiler output to be provided all year round for water heating has thus dropped to a fraction of the original.
Scheme heating
The diagram explains the circuitry of the heating system with the fan circuit and the radiator circuit. The Viessmann Vitoplex 200 oil condensing boiler (700 kW) with a two-stage Weishaupt burner must first and foremost maintain the weather-compensated flow temperature from at least 45 °C up to 85 °C for the warm air heating (LU). The design is based on a spread 85/45 °C. In fact, however, the return rate should be about 50 °C. The boiler consists of a calorific value boiler and a downstream latent heat exchanger. Its flow serves the main circuit directly (burner-controlled) with a NW 100 pipe.
The philosophy of the rendeMIX circuit is to build up high temperature gradients. One of the mistakes of the past was to combine cold and hot returns and return them to the boiler together, according to the thinking: If you insulate their pipes sufficiently, no heat will be lost, so the boiler won't have to push as much. This is true to a limited extent, but due to the lack of temperature differences, it is unfortunately no longer possible to recover residual heat from a warmer medium with the help of a colder medium in order to possibly even heat with the mixed temperature alone. It is only since the introduction of condensing boiler technology and condensation, as well as the acceptance of different temperature levels, that heating technology no longer collects returning energy in a single pot, but separates it into different anergy and exergy pots.
On the valve side, the most elegant switch for this is probably the "rendeMIX" method. In the radiator circuit (wheel) of the switching diagram, the two mixing distributors 250 3×2 VL 5 in point 7 take the fan return water from 45 oC and send the radiator return of 35°C via point 2 into the RL2 latent heat exchanger. The flow of 60 °C mix the "rendeMIX" from the 45-grd fan return plus a shot of 85-grd supply (via point 1).
The latent heat exchanger (behind RL2) pushes the condensation gains into the return line RL1. The picture does not show this directly, but the hydraulics look like this: the return RL2 flows via the latent heat exchanger into the return RL1 and then flows back via the oil boiler to the supply temperature of 85 °C. The return RL1 is then connected to the oil boiler. °C to be raised.
Before mixing with RL2, RL1 has the temperature of 45 to 50 oC, according to the setting of the return thermostats (RTB valve) of the warm air fans. As already mentioned in the main text, the RTB valve locks the return flow from the fan above 45 to 50 °C. The resulting increase in differential pressure causes the circulation water to be throttled with the help of the controlled high-efficiency pump. The resulting increase in differential pressure ensures that the circulating water volume in the fan circuit is throttled with the help of the controlled high-efficiency pump - at a constant Delta-T.
The lower rCOL 3×8 - 2 is basically just a distributor. The two types are mounted on it DN25 3×2 VL 5. Three times two means: three incoming (2 - 7- 1) and two outgoing (6 - 5) connections. The additional number 5 only gives an indication of the circulating pump that can be flanged directly to the flow (5).
On the right, the third grey rectangle with the designation sBox DN25 2×2 VL 3indicates the uncontrolled heating circuit for domestic hot water heating (reserve). If required, this can also be provided by the 700 kW boiler. The assembly includes the circulation pump with gravity brake, thermometers and the shut-off valve function, but feeds its return flow into the centre chamber of the manifold so that it is combined with the 50 kW air heater return flow and remains separate from the 30 kW radiator return flow.
The water heater with a capacity of 1,000 litres (Fig. 2) is heated either by the specified oil condensing boiler from Vaillant (icoVIT) with an output of 19 kW or alternatively by the 700 kW Viessmann boiler, which also supplies the fan circuit. "Alternative" in this context is based on the current operating situation. While the main boiler produces the heat for the ventilation circuit, it can also load the storage tank. The planning also integrated a return temperature limiter into this scheme to ensure both condensation operation in the Vaillant boiler and to stabilise the hydraulics in the main circuit - if the Viessmann heat generator serves the storage tank - at the 45 to 50 °C mentioned.
The new fuel oil-fired steam generator no longer has anything to do with hot water preparation. It only supplies the mixing tanks during operation and thus adapts its operating hours to the steam demand actually required, according to the low-water and thus energy-saving continuous-flow heater principle (type Clayton EO-10, output 100 kW, operating pressure adjustable up to 7 bar, steam production at 1 bar 157 kg/h), which also minimises standby losses.
This is a brief description of the hydraulic and supply-related renovation of the three circuits heating, hot water and steam, and four circuits with the electric instantaneous water heater in the non-explosion-proof laboratory. The redesigned master plan already promised a considerable reduction in consumption.
Optimisation with mixing manifolds
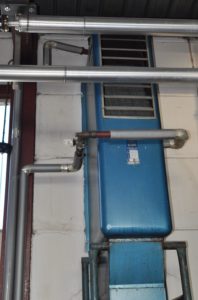
Figure 7: The existing fans were not replaced, but were made suitable for condensing boilers with thermostatic valves as return temperature limiters.
Furthermore, a control engineering refinement of the heating scheme should additionally translate into savings. The long title of this measure is: "Optimisation of the heating system of Chemoplast NV - Efficient operation of the downsized condensing boiler system by converting to a three-chamber distributor with return utilisation for two controlled radiator circuits with 'rendeMIX' as well as S-Box for loading the hot water tank". Behind this is ultimately the special hydraulic scheme of the company HG Baunach GmbH & Co. KG based on the "rendeMIX" multi-way mixing manifold. These allow high and low-temperature circuits to be connected in series, thus turning the return of a high-temperature circuit into the flow of a low-temperature circuit, with inner and outer balancing sections of the "rendeMIX" installation correctly balancing the individual water volumes.
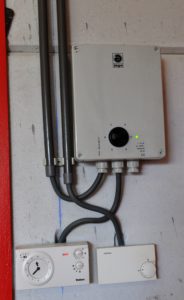
Fig. 8: ... and with frequency converters for speed control of the fans
The method has already proven itself several thousand times in residential construction by allowing radiators (high temperature) to be coupled with underfloor heating (low temperature). Firstly, this benefits a large temperature spread and thus usually at least a halving of the water volume to be circulated. Secondly, the return water, which is now cool, often condenses to well below 30°C. oC in the condensing heat exchanger of the boiler condenses the flue gases well below the dew point so that the latent heat is not lost. Only at a correspondingly low return temperature can the condensing boiler fulfil its task of making the condensation heat usable for heating purposes.
Two return connections
At Chemoplast NV in the Europark in Flanders, the weather-controlled fan circuit is the high-temperature circuit. Strictly speaking, the oil condensing boiler here consists of two components, a calorific value boiler and a separate latent heat exchanger in the flue gas duct. HG Baunach GmbH & Co. KG chose this combination in order to be able to operate with two return connections, one at the boiler, the other at the condenser. The advantage of these two return connections can be explained as follows:
First of all, it should be said that to the fans in the factory halls - they were not replaced, but their fans were limited in speed - an immense volume of water of up to 85% was pumped through a pipe in NW 100. oC flow temperature circulates. This weather-controlled temperature must be able to reach this level for sufficient warm air production. Furthermore, the Karremans heating company installed a thermostatic valve as a return temperature limiter directly behind each of the approximately 30 fans. Its thermocouple closes the valve if the return temperature rises above 45 to 50 °C due to insufficient heat removal. oC climbs. The associated throttling sends a signal to the controlled circulation pump via the increased differential pressure to adjust the flow rate accordingly so that the other fans remain unaffected.
This circuit starts and ends in the calorific value boiler. The return with the aforementioned 45 to 50 oC does not permit the use of calorific value, since the dew point of EL fuel oil is 48 oC. In addition, condensation must not take place in the calorific value boiler because this part of the boiler is not designed for this purpose and therefore has the return increase prescribed for safety reasons.
Chemoplast NV
In the 1970s, the Belgian government closed the coal mines in Limburg. To compensate, the country promoted industrialisation in the region. Of course, the supply could not cover the demand for jobs. The labour market in Germany, on the other hand, was characterised by the opposite situation at the time. The Federal Republic was building up, the economic miracle was flourishing and everywhere there was a shortage of workers. A German entrepreneur from Bergisch-Gladbach, who had been producing car polishes and other products for cleaning the outside and inside of vehicles since 1936, therefore relocated his production plant to Houthalen. There was enough manpower, the wage level was right and for deliveries throughout Germany and Europe it made no difference whether the trucks delivered from Cologne or Bensberg to France or Portugal or from Limburg in Belgium. Administration and operations remained in Germany.
When the German car driver no longer washed his favourite child, the car body, carefully by hand with leather and a dry cloth, and washing machines replaced hand washing products, Chemoplast NV expanded its product range to include cleaning agents for industry, railways and haulage companies. Almost all trains in Holland, including suburban trains, use products from Houthalen. Vienna's suburban trains and undergrounds also get their fresh shine with "Starcare" products from Limburg, the Siemens locomotives of the Trans-Siberian Railway or the Russian high-speed train from St. Petersburg to Moscow.
In 2012, Chemoplast NV bought the know-how, recipes and licences of a company that has car manufacturers as its customers. There, quality management includes carefully cleaning the painting robots after each colour change. This is done with the help of a special solvent from various combinations. Due to this expansion, the German-Belgian company expects a 30 to 40 percent increase in turnover in the coming years. The company is also in the process of establishing itself more and more as an OEM supplier for cleaning agent manufacturers who want to keep their capacities at a basic level.
Calorific value guaranteed
85 to 90 percent of the supply heat is required by the fans, 10 to 15 percent by the radiators in the office areas and in the sanitary and changing rooms. A design spread of 60/40 is sufficient for these heat sources. oC. This pairing means nothing other than that in the majority of the heating period the return is a few or many degrees below the 40 oC moves. Only the radiator return therefore enters the condenser. It lowers the exhaust gas temperature on average to 33 to 35 oC. The latent heat exchanger is thus able to extract from the flue gas a large part of the almost 10 percent residual energy that would escape through the chimney without it.
However, the described return strategy with calorific value utilisation only works with the "rendeMIX" mixers, both as a coupling between the two heating circuits and as a flow divider. The hydraulics of the heating system at Chemoplast NV are such that a partial volume of the higher-temperature return flow of the fan circuit supplies the lower-temperature radiator circuit. If the latter requires a flow temperature of 60 °C in the depths of winter, the rendeMIX raises the 45 to 50 °C source temperature by mixing in hot boiler water from the flow of the fan circuit. In the majority of the heating season, however, the radiator-heated rooms should be able to get by with the 45 to 50 °C fan water, which can be lowered by adding the room's own return water if necessary.
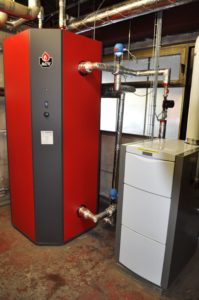
Fig. 9: 19 kW oil condensing boiler (Vaillant icoVIT) for year-round water heating
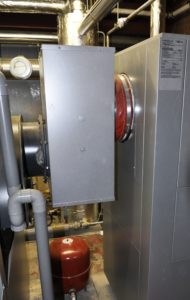
Fig. 10: The external latent heat exchanger behind the oil boiler (far right, Viessmann Vitotrans) allows the connection of a separate heating return and thus utilisation of the condensing value at high flow temperatures (see text for explanation). The silver-grey flue gas box between the exchanger and the boiler merely compensates for the different heights of the boiler outlet and the heat exchanger inlet.
The entire flue gas leaves the oil boiler system via the flange-mounted condenser. In terms of supply, this acts as a heat generator for the radiators - in fact with the result that the condensing value gain alone is sufficient to cover a large part of the heating requirements of the social rooms and the offices.
Redevelopment started 6 years ago
In 2007, Werner Sauer came to the conclusion that something had to be done. In November, he began recording data on both heat generators, followed by the first hydraulic measures in summer 2008, such as the installation of radiant ceiling panels, the retrofitting of return temperature limiters and the installation of a regulated high-efficiency pump. In 2009, the evaluation of the measured data revealed the enormous oversizing of the boiler and steam generator and in the following summer of 2010, the conversion work in the hydraulic network was completed with the installation of speed controllers for air heaters. These measures alone had not only already led to a reduction in the annual heating oil requirement from an average of around 60,000 litres to 50,000 litres of heating oil, or around 15%, but also caused the delta T of the fan circuit to rise from an initial 2K to a respectable 20K. Only now, in Hans-Georg Baunach's opinion, was the prerequisite for refining and realising the plans to convert to a demand-based condensing boiler and a condensing heat distribution system. The starting signal was given in spring 2011 when the old steam generator sprung a leak: the emergency operation to replace the boiler, including heat distribution, hot water preparation and steam generation, was carried out during the heating period, but the complete control system only went into operation in early summer 2012. Based on the time intervals between tank fillings, a further "yield" of 20 to 25 per cent could be predicted after just a few months, i.e. a further reduction in heating oil consumption from an average of 50,000 to 40,000 litres per year.
Today 40,000 instead of 60,000 l heating oil
This range is unlikely to be the maximum yet, as there is still potential for optimisation, particularly in the setting of the control system. "I assume that we will ultimately not only save more than a third of the oil, but that electricity consumption will also be significantly reduced because the controlled high-efficiency pump can only fully develop its effect through the installation of the return temperature limiter," explains Hans-Georg Baunach.
The thermostatic valves as return temperature limiters, in conjunction with the differential pressure-controlled pump, ensure thermal-hydraulic balancing: If the valve throttles the flow due to excessive return temperatures, the return temperature remains constant even if the fans of the air heaters are switched off via electric room thermostats. However, this reduces the heat output during fan operation, which leads to "cold draughts" if the fan speed remains high. However, as long as the required heat output can still be provided, reducing the fan speed has the following advantages:
- Higher air outlet temperature
- Less air speed, thus also less dust pollution
- Less noise emission
- More even utilisation of the heating surfaces.
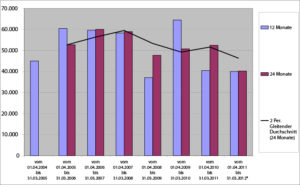
Figure 11: Based on the base year 2007 (years from 01.04. of the respective year to 31.03. of the following year), the year before the renovation work began, the hydraulic renovation in the years 2008 to 2010 already led to a reduction in heating oil consumption from 60,000 litres to 50,000 litres. The subsequent replacement of the old system with a modern oil condensing boiler (commissioned in December 2012) saved another 10,000 litres of heating oil. Consultant Hans-Georg Baunach and plant engineer Karremans "don't see this as the end of the line" (Baunach). They expect an even higher increase in efficiency at the end of this heating season, the first in which the new system, including the control system, will be used for heating.
Chess of the messy hydraulics
The last point in particular should not be underestimated for system efficiency: The more evenly the total heat flows over the bottleneck of the totality of all heating surfaces, the lower the delta-T between water and air necessary for this. This has a particularly strong influence on the return temperature and thus on the efficiency of the condensing boiler. Whether the boiler will enter condensing mode is therefore mostly decided on the system side.
Hans-Georg Baunach sums up: "In terms of heating technology, many industrial plants are probably a fallow field. Look at it this way, every 100 litres of heating oil saved relieves the atmosphere of around 250 kg of carbon dioxide. You just have to bear these figures in mind. If the legislator would rigorously regulate or even promote the old stock in this area, Germany and the EU could easily achieve all Kyoto targets. Of course, we, the heating industry, must not gamble away our reputation. Condensing boilers must not be allowed to operate predominantly in calorific value mode. We, the manufacturers and component suppliers, together with the planning department, offer all the technical possibilities to put the hydraulics in order.
Measured energy consumption of the building
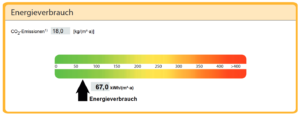
Fig. 12: The energy passport shows: with a heated area of 6,000 m², an annual heating oil consumption of 40,000 l with an energy consumption of 67 kWh/m²-a) and a CO2 emission of 18 kg/m²-a practically corresponds to a low-energy house standard - in a building from the 1960s with forced ventilation in the explosion-protected work area!
Chemoplast NV Houthalen (Belgium)
Investment volume: € 240,000
Cost saving: 12.000,-€
CashFlow: 5%
HG Baunach GmbH & Co. KG
E-mail: info@baunach.net
Homepage: www.baunach.net