Intelligent mixing solves problems
"The system is worth every euro"
The Schweinfurt SHK Guild moved into a new association building in 2004. The new building in the Hainig industrial estate was to be an "energy-saving centre". On the one hand, they wanted to operate in an exemplary manner in terms of energy, and on the other hand, as many different technologies as possible were to be shown here. Everything was done with initiative and commitment, but there was one thing that annoyed guild manager Josef Bock: the storage tank, which is loaded with thermal energy from the heat pump, the pellet boiler and the solar system, was not stratified optimally. Good advice was expensive.
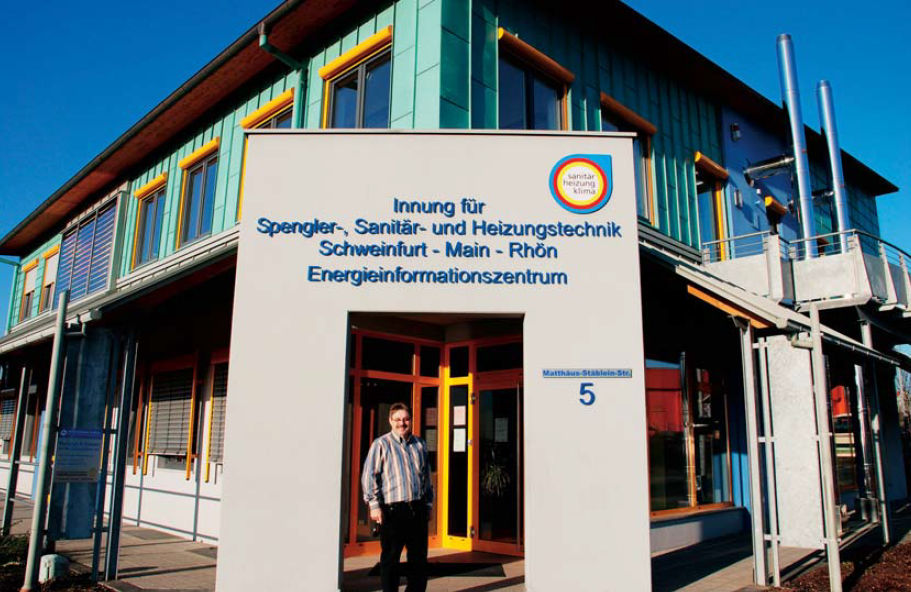
Fig.1: Guild manager Josef Bock in front of the new guild building in Mathäus-Stäblein-Straße. Much of the work was done by the members themselves.
The old location at the local Chamber of Crafts was bursting at the seams: Modern training rooms for the member companies were missing, the examination conditions for the trainees were no longer optimal. The building in the Hainig industrial estate in Schweinfurt not only looks appealing, in the colours blue, green and yellow. It also stands out because of its modern architecture and the dignified furnishings with stainless steel chimneys, copper processing and the solar system on the roof and façade. Inside, there is a hustle and bustle, pupils of different ages seem to have taken over the building. Josef Bock explains: "In addition to adult education, we regularly have school projects here on the topic of "technology in crafts". Eighth-grade pupils do a two-week practical here. The children of today are the apprentices of tomorrow and they in turn are the skilled workers of the day after tomorrow. The sanitation, heating and air-conditioning trade demands a lot from the skilled workers, on the one hand a high level of general knowledge, technical understanding of the theory and, on the other hand, the necessary practice. You can learn to lay a pipe in a week, but you have to know a bit more to install a geothermal heat pump so that it works properly in terms of energy.
In focus: Adult education
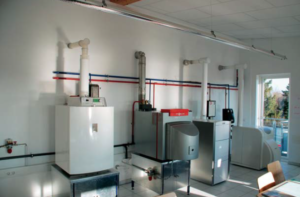
Fig. 2: One of the training rooms where, among other things, the training courses for SHK customer service fitters take place.
For example, the "SHK customer service technician" is trained. Apart from Schweinfurt, this training course is only available in Traunstein. The further training course "electrician" comprises 48 hours of instruction and every specialised company that wants to replace a heating pump, for example, must present this further training. Some companies do not (yet) realise this, but in case of an accident, they are on the safe side, he says. This year, for the first time, the course "Energy Consultant" will be offered. Together with the responsible district office, this further training course is to be expanded successively. A thermography camera has already been purchased. The interest in such recordings is definitely there, a growing number of enquiries confirms this. Josef Bock wants the member companies not to let their opportunities for new business fields slip away lightly.
For everyone: optimal conditions
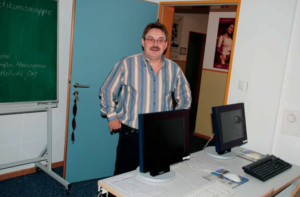
Fig. 3: In this training room, a modern computer workstation is available for each participant.
The house has two training rooms. One of them contains gas heating appliances from various suppliers, so it is used to show the entire range of gas heating technology, and the other is dedicated to oil heating technology. Furthermore, there is a computer cabinet with twelve seats. Here, for example, the course "Energy Consultant" can be held; each seat has its own modern flat screen. The trainer can also use training software from the ZV SHK. In addition, the building has a workshop, offices and a break room that can also be used for specialist presentations - for example on heat pumps, pellet boilers, geothermal energy, etc. - on a larger scale. Up to 1000 visitors are counted here every year. Josef Bock sees his guild as a service provider for the members, which spurs him on again and again to develop and offer new services.
One hall: different users
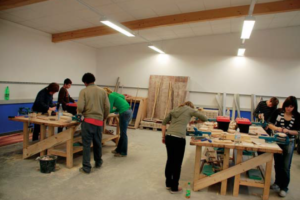
Fig. 4: The newly added hall on the guild's premises now offers exemplary conditions for the journeymen's examinations. During the exam-free period, students learn how to work with different materials in practical courses.
For example, the new hall that was built in 2006. The journeymen's examinations for the new profession of plant mechanic are held there. The examination conditions for the new occupation have changed and become more demanding, including the practical examination conditions. The space conditions in the BTZ at the Chamber of Crafts were no longer optimal and so it was decided to build an extension at the new guild location. Here, 16 apprentices can take their exams at the same time. Further training courses for the tinsmith trade are also regularly offered and held there. In addition, projects take place here with secondary school pupils who learn how to work with different materials and tools. For example, bricks are laid, paving is done or sawing is done. In addition to the practical activities, teamwork is also encouraged in these projects. This year, an entire house - in miniature, of course - is to be built together in the hall. In the second part of the project, the basics of electrical engineering are taught, for example with regard to control technology in heating technology, to show what electricity actually is, and also to point out the dangers of electricity and its possibilities. Woodworking also occupies a large space. The handling of different types of wood, the topic of environmental protection and trying out simple tools, but also theory, keeping to measurements, etc. play a role. At the end, a self-made piece, such as a birdhouse, is taken home.
Exemplary: Helping people to help themselves

Fig. 5: Integration into the façade allows the sun's rays to be optimally captured even in winter.
But that is not all in the Schweinfurt guild house: the so-called "practice class" should not go unmentioned. The practice class, 25 pupils from a secondary school (7 nations), are in the guild for one year. According to Josef Bock, these pupils rarely experience anything positive. Together with the teachers, they are supposed to gain positive experiences and learn positive thinking here, far away from grades and reprimands. Where lies, tricks and untrust prevail in the beginning, reliability, punctuality and trust are to be learned later. Together with the school, tasks are set that link theory and practice. For example, cakes are baked and the pupils realise that they have to be able to read, weigh and calculate. This is to motivate the pupils not to regard mathematics as a tiresome theory, but as an important tool in daily life, thus promoting their will to learn. The best reward for Josef Bock and his comrades-in-arms is when he can subsequently place such pupils in an apprenticeship.
Many heat sources and a buffer tank
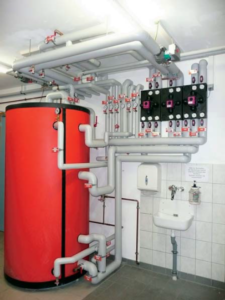
Fig. 6: The memory with the inputs and outputs and the three rendeMIX.
The guild's premises are well utilised, about 80%, Josef Bock estimates. More is hardly possible, because he conducts many of the training courses for adults himself, plus the office work. The building has three floors, the two training rooms are each 85 m2 large, the workshop 120 m2, the break room 120 m2. With the offices, toilets, washrooms and kitchen, there are approx. 700 m2 area to be heated. The entire building is heated by a heat pump with a surface absorber. About 400 metres of piping are laid on the guild's premises. The heat pump has an output of 8.7 kW, which is perfectly sufficient in the transitional period. On colder days, a pellet boiler jumps in. All heating appliances in the building can feed their heat into the system, regardless of whether they are oil or gas boilers or solar systems. All the heat generated anywhere in the house ends up in the 1500-litre buffer tank in the basement. When constructing the new building, it was important for the guild members to be at the "state of the art" and to have as many of the technologies available on the market as possible on site and in action.
Cardinal error: mixing in the reservoir
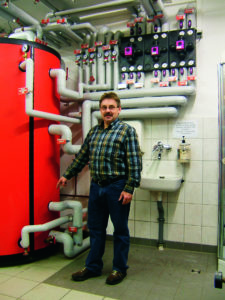
Fig. 7: "We have never had 20° C at this point", Josef Bock points to the cold zone in the buffer tank.
It's obvious to Josef Bock how much the problem must have "bugged" him, because he says: "Shameful actually, we got mixing in the buffer tank." Knowing full well that this system is not "off the shelf" and, due to the diversity of the approx. 18 heat generators, not easily comparable with other systems. The issue here was neither high energy consumption nor cold rooms. The large number of connections and pumps on the storage tank meant that the water in the tank was mixed up. He could also read this directly from the installed temperature sensors. What was really annoying was that training sessions on the gas appliances sometimes had to be cancelled because the storage tank could no longer absorb heat and the appliances went into malfunction. Also, neither could the connected solar system feed its generated heat optimally, nor did the provision of hot water in the kitchen always work quite satisfactorily. Josef Bock had already met Hans-Georg Baunach during the ISH 2005, who then presented his mixing manifold concept rendeMIX to the guild. At that time, interest in the product was still limited. Josef Bock comments: "What he builds is relatively simple, but mentally you have to understand what is actually happening. Once you understand that, you can use positive arguments to convince customers who have similar problems to the ones we had."
Simple solution: Never mix hot with cold
Company owner Hans-Georg Baunach had first looked at the system on site. He explains the problem as follows: "It doesn't just depend on how much heat is contained in the buffer tank, but also on what benefit it provides. If I want to have a bathtub full of 40° C water, then it is of relatively little use to me if the distribution of the same amount of heat in the buffer can only produce two bathtubs with 25° C. But a mixed storage tank is not only too cold to prepare drinking water, so that the boilers have to be fired up. At the same time, it is also too warm to be able to absorb solar heat, for example - a double loss. However, if I have good stratification, then the amount of heat contained in the buffer is concentrated in the smallest possible area with the highest possible temperatures and is ready to release heat, while the remaining volume below it has the lowest possible temperatures for heat absorption. The rendeMIX principle is very simple: never mix hot water with cold water, but instead always either hot water with warm water or warm water with cold water! But it is important to implement this simple principle consistently if you want to achieve success and regenerative efficiency in hydraulics. And that is exactly what we are doing."
One mixer, three processes, many advantages: the rendeMIX
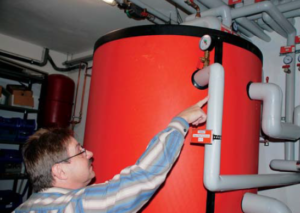
Fig. 7: Josef Bock shows the entrance of the pipe-in-pipe system into the buffer tank.
But where does the rendeMIX multi-way mixer get the warm water from?
- Either from the return flow of a higher-temperature heating circuit - in which case the manufacturer speaks of "return flow utilisation". With this method, high-temperature and low-temperature networks are connected in series. The return of a high-temperature circuit becomes the flow of a low-temperature circuit. By means of an integrated bypass, which acts like a diverter valve, both circuits remain hydraulically decoupled even in the event of flow rate changes. The actuator of the mixer can be controlled with the three-point signal of any normal heating circuit control. This procedure reduces the return temperatures and volume flows, so that condensing boilers can sweat out up to 10% more condensate and buffers can absorb up to 50% more heat.
- Or the warm water comes from the middle of a buffer tank. This then leads to the "two-zone discharge" procedure, in which the lower cold zone of the buffer is first accessed until it no longer provides sufficient temperature. Only then is the hot zone above accessed, whereby the hot water from the upper buffer connection is now mixed with the hot water from the centre of the buffer, so that significantly less hot water is still required than with three-way mixing with cold water from the heating circuit return. At the same time, the full cold water return flows into the buffer. Due to this heat extraction, the buffer remains hot longer at the top and gets cold faster at the bottom. Even with only one heating circuit, the high-temperature heat that can be used for DHW preparation increases by up to one third. If several heating circuits are to be supplied, the two-zone discharge can be combined with the return utilisation, whereby the buffer efficiency can be almost doubled.
-
Fig. 8: Happy about the successful joint project: from left to right Herbert Spiegel (HD Spiegel Innovation), head foreman Berthold Sterzinger (who has since installed a rendeMIX in his own home), Hans-Georg Baunach, HG Baunach GmbH & Co. KG and Joachim Jost (Sonnenkraft GmbH).
Conversely, this two-zone method can also be used to load the buffer tank if the heat generator has to be equipped with a return temperature increase, such as wood boilers and CHP units. In this case, the upper hot zone is loaded first and only then the lower cold zone, whereby the buffer becomes hot faster at the top and remains cold longer at the bottom.
The Schweinfurt Hydraulics Concept
In the case of Schweinfurt, all three methods were used: The boilers in the two training rooms - each equipped with its own pump and non-return valve - and the pellet boiler in the large hall load the buffer via a common rendeMIX 2×3 return lift (RLA) using the two-zone method, which keeps the return temperature constant at around 55° C via a controller integrated in the actuator. This results in higher flow temperatures almost independently of the output with a temperature spread of approx. 70/55° C, which are fed into the buffer at the top. The weather-dependent supply of the high-temperature circuits - radiators on the upper floor and Venkons on the ground floor of the old building - is taken over by a 3mix 2×2, the return flow of which can be used by the low-temperature circuits - underfloor heating on the ground floor of the old building and in two new buildings - before it is fed into the middle buffer connection. Finally, their weather-controlled supply is taken over by a rendeMIX 3×2, which combines the two-zone discharge with the return utilisation. This results in an extremely large volume flow of the coldest possible return water. It was also important to limit the number of connections to the buffer to the necessary minimum: the main heat distribution is only connected via three connections in order to limit the water flow in the buffer to the hydraulic balance between generators and consumers. The wall-mounted condensing boiler, originally installed for heating the building, takes over the weather-compensated control of the mixing circuits and, via a fourth connection, only ensures the domestic hot water capability of the upper decile of the buffer. Connected to these three pipes (hot, warm, cold) in the adjacent room are a solar thermal stratified charging module with a switching valve and a fresh water station from Sonnenkraft. The heat pump is connected in parallel between the uppermost and the lowermost buffer connection and should only be operated when all other heat generators are switched off, as it destroys any stratification with its low ΔT and the large volume flow. It is only in action when no training is being carried out and is switched off one or two days beforehand to allow the buffer to cool down.
On top: the Pipe-in-Pipe system
System Pipe-in-Pipe what is it? With SPP, the circulation pipe is laid in the flow pipe. This routing directly in the hot water pipe saves material costs and, above all, installation time. In a new installation, the internal pipe can be inserted immediately - i.e. before grouting and screwing - and laid together with the flow pipe. In the case of renovation or retrofitting, as in the case of the Schweinfurt guild, an additional insertion aid was used, which makes it much easier to insert the pipe. The heart of the system is a fitting with sleeve. With the fitting, the pipe is led (through and) out; with the sleeve, the pipe is fixed. Even changes of direction are possible. The end of the plastic pipe is guided through the special fitting FSP, which is patented by Spiegel Innovation. Special tools or grouting are not required for this. Due to the so-called one-way system in the borehole, the plastic pipe is held in place and prevented from sliding out. This completes the installation of the circulation pipe. Further reasons why this system should not be missing from any drinking water installation:
- The high energy-saving effect of the interiorcirculation, as in this case, resulted in a reduction of CO2–emissions compared to conventionalcirculation by 1500 kg CO2 per year. In connection with the PPW from HD Spiegel Innovation once again approx. 1000 kg CO2 less, so were together approx. 3 tonnes of CO2 per year saved for this plant! In a One-family house can reduce CO2-output by approx. 1.5 to 2 tonnes per year.lowered.
- Through this system, the regulation W551 (ΔT of 5 K) and further hygienical aspects are easily complied with.
- The construction of this special formavoids cavities and eliminates the need foron seals, which prevents stagnation of water.ser and germination points are prevented. Also with Pipe-in-Pipe heat exchangers or the Circulation sword with layer combinationstore, this goal is optimally achieved.
In future, installers will be particularlyThe focus is on the hygienic design of spittoons.and their connections (stagnationdanger), in order to avoid the risk of of bacteria and legionella. Why Pipe-in-pipe heat exchanger (PPW) for a fresh water module? With connection of a circulation system on a fresh watermodule (feed at the cold water inlet).The following disadvantages result from the use of a single corridor: The possible calcification of the module and Above all, the "feed-back" from the higherhigher circulation temperature in the Cold area of the storage tank and thus the associated destruction of the stratification. With PPW, these disadvantages are pasttiveness. The installation is carried out in the proven Pipe-in-pipe technology, depending on the design of the storage tank, in the "warm zone". With layerThe storage tanks, which are used in the flowheating the water, there is no circulation connection is planned. Instead The circulation is switched off via the cold waterinlet is integrated. As a result destroys the stratification of the reservoir, Solar systems can only supply energy to the Release the storage tank when the temperature is above the circulation temperature. With Help of the moulding from HD Spiegel The circulation line is connected to the supplyin the hot water section of the storage is introduced and thus the opThe use of the system is guaranteed for a long period of time. Several storage manufacturers (Nau, Solarfocus, IFF Kollmannsberger, Fröling) set this circulatory sword already with theirstorage facilities. The company HD Spiegel Innovation continues to focus on innovative Storage manufacturers and dealers who use theinclude this system in their programme.want to do.
Perfect solution: Satisfied customer
"I'm thrilled," is how Josef Bock sums up the result of the joint work. "Down there in the buffer we never had around 20 °C before". The Baunach company planned the system and Josef Bock himself installed everything. "I go into the radiators at a temperature of 0 °C to -5 °C with about 40 to 45° C, come out of the radiators with 32 to max. 35° C, go into the underfloor heating with it, the attached hall, for example, has concrete activation, there is also wall heating in the building and a ventilation system with heat recovery. The return flow from the low-temperature systems then only has a temperature of approx. 19 to 29° C. This means that only cool water enters the building. This means that only cool water reaches the cold zone of the buffer storage tank and can be reheated there. We have now achieved this and we are proud of it," says Josef Bock, summing up the result of the efforts. What he finds particularly advantageous about Hans-Georg Baunach's system is that it adapts to the conditions on site: The customer does not have to reinstall the entire system, but the rendeMIX mixers are individually adapted to the system. Also, the training sessions on the heaters do not have to be interrupted now because the storage tank can absorb the generated heat (up to 200 kW) from the exercise rooms without any problems. This energy does not need to be destroyed, but is put to good use. Naturally, Josef Bock has included the rendeMIX system in his training courses. He sees it as a duty that his master craftsmen not only know the system, but also know how to use it. "rendeMIX is the state of the art for us!"
Download the technical article as PDF