Well thought-out planning for low operating costs
Small investments open up great savings potential at Lebenshilfe Wohnwelten in Altdorf
When not only low construction costs, but also low operating costs are the focus of object planning, architects and planners must reveal their skills. This was the objective of the "Inclusive Housing Worlds" of the Lebenshilfe in the Nuremberg Region to fulfil.
With customised planning and "off-the-shelf" technology, the provision of heat and the generation of electricity could be optimised here - the core components of the combined heat and power unit and the heat storage system work together excellently for this purpose.
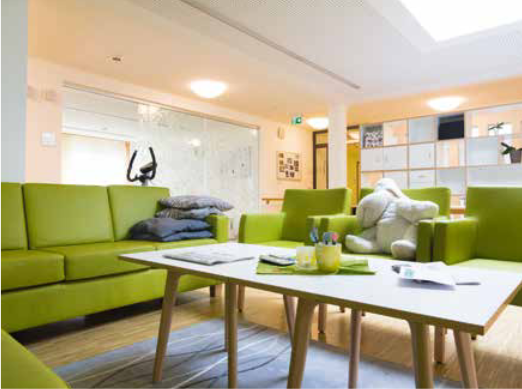
Fig. 1: Some areas, such as the interior communal zones (picture), the foyer, the corridors or meeting rooms of the inclusive living environments are supplied by decentralised ventilation systems.
Lebenshilfe im Nürnberger Land e. V. operates more than 20 properties where people with developmental delays or disabilities find a home and are cared for. The residents are usually assisted by permanent Lebenshilfe employees. However, a new approach is being taken in the young "Inclusive Living Worlds" in Altdorf. The Lebenshilfe property, which was occupied for the first time in spring 2016, offers living space for people with handicaps and for people without disabilities. The latter can contribute to the care, for example cooking or organising the leisure time of the working people with disabilities, and receive a flat-rate honorary allowance for this, which in turn reduces the rental costs. For the concept of inclusive living, Lebenshilfe constructed a building with 26 flats for people with disabilities and five more for tenants without disabilities. The building has three floors, each with approximately 2500 m² of gross floor space.
On the ground floor, there is a lounge and a conference room, a café with its own large kitchen and various utility and technical rooms. On the first and first floors are the residents' flats - each with its own bathroom and anteroom - as well as two communal kitchens and large communal areas per floor. In addition, there is a nursing bathroom and e.g. household rooms in the core area.
"Common sense reigned in planning and construction".
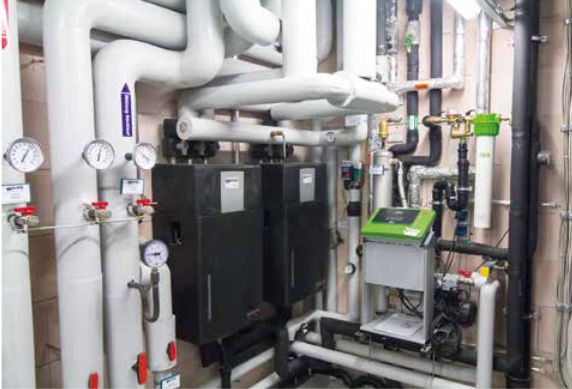
Fig. 2: An exergy-optimised cascade of fresh water stations plays its part in maximising the temperature spread - and thus the thermal efficiency - of the entire system.
Around 6 million euros went into the construction of the "Inclusive Living Worlds". Two thirds of this was financed by grants, the rest was contributed by Lebenshilfe. Since the Altdorfer Wohnwelten were financed from public and own funds and the rents should be affordable for the residents, the property was planned by Prof. Dipl.-Ing. Hans Peter Haid (Managing Director of Haid+Partner GmbH Architekten+Ingenieure, Nuremberg) with the objective of "high efficiency". The architect, who specialises in health and social buildings, had spoken to prospective residents before the designs were drawn up and incorporated their wishes and ideas into the concept. The result is a building with a highly insulated outer shell and a good floor plan that does without large glass fronts and thus ensures low heating costs. The focus of the planning for the technical building equipment was on the tasks and the residents of the facility. "For this purpose, well thought-out and easy-to-use equipment makes life easier for the residents, explains expert planner Roland Goetz from Altdorf, a project requirement.
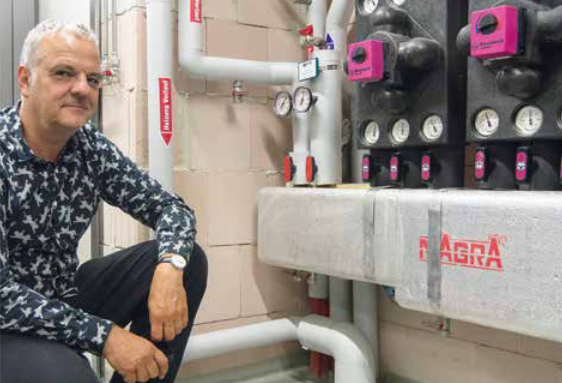
Fig. 3: Specialist planner Roland Goetz in front of the multi-value distributors. They make the return of a high-temperature heat circuit usable for the flow of a low-temperature circuit. This maximises the temperature spread and thus the thermal efficiency.
For example, the barrier-free bathrooms can be extended with additional grab bars and all washbasins in the building can be accessed by wheelchairs. Even features that are not directly visible, such as the mixers with anti-scald protection installed everywhere, reveal that the focus was not on saving money at the wrong end, but on safety and durability.
Classic heating and ventilation in the flats
Conventional radiators with thermostatic valves mounted under the windows are used to heat the flats. In the bathrooms of the flats, stale or humid air is extracted. The resulting suction effect ensures a constant supply of outside air via outside air vents, which are installed behind the radiators under the windows. In addition, all windows can be opened if necessary.
Only the communal zones and rooms are completely mechanically ventilated. For them, ventilation units with heat recovery (via plate heat exchangers) are installed in kitchen wall units or wall cabinets. The units supply the respective ventilation zones via short duct routes, so that pressure losses are minimised. Low fan speeds and careful carpentry ensure that the ventilation technology is not only visually but also acoustically unobtrusive.
CHP covers basic heat demand
In addition to the concealed, decentralised ventilation units, specialist planner Goetz also designed the complete other technical infrastructure. For heat generation, he chose a natural gas-powered small CHP (combined heat and power) unit from Viessmann with 6 kW electrical and 15 kW thermal output. It is supplemented by an 80 kW peak-load condensing boiler. Both feed the heat to a buffer storage tank from varmeco with a capacity of about 3 m³ of water. "All the heat consumers in the house are served from the storage tank," Goetz explains. "The CHP is sufficiently large to cover more than half of the total heat demand, so that the requirements of the Renewable Energies Heat Act are met. On the other hand, the output is again small enough to run a base load operation - i.e. high running times with few starts and stops, which is made possible by the use of the storage tank," says Goetz.
The operation of the CHP unit is temperature-controlled. If the sensor on the upper part of the storage tank detects a temperature below 65 °C, the CHP control unit switches on the motor. How warm the water is in the lower part of the storage tank, which is pumped to the CHP unit for heating, is irrelevant for its operation: A speed-controlled charging pump ensures that the CHP unit always operates constantly. If the water is cool, the pump regulates the flow rate so that the dwell time is sufficient for the water to heat up to more than 80 °C. "This is the only way to implement condensing operation that exploits the CHP's output. It should be noted that not all CHP units are suitable for utilising the exhaust gas heat with condensing technology," adds the planner, "but the installed system enables the exhaust gas to be cooled down considerably and is also a perfect fit for this property in terms of size." With up to 75 kW, most of the heat output is available for the radiators in the rooms outside. Another heating circuit serves the heating requirements of the nursing baths in the central areas of the floors with a maximum output of 3.5 kW at 70/50 °C flow/return temperature. Up to 13.4 kW at 40/25 °C is available for the heat exchangers of the ventilation systems. The industrial laundry dryer may draw a further 10 kW: the industrial washing machine also usually manages without electrical heating energy, because the building services provide up to 16 l/min of rainwater at a temperature of 60 °C for it. Only for the final rinse of the laundry is potable hot water used. For higher washing temperatures (boiling laundry), the electric heating of the washing machine quickly brings the water up to temperature with 18 kW.
Three-chamber manifold for optimum temperature spread
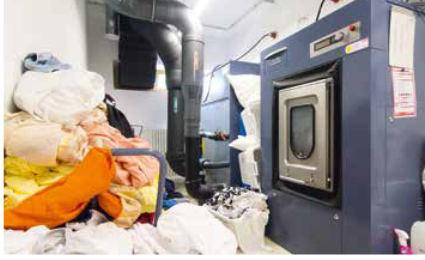
Fig. 4: The industrial washing machine (front) and the tumble dryer. Both work with the heat from the CHP unit; only in the cooking wash programme does the washing machine reheat electrically.
"To ensure that the temperature spread in the heat storage tank is as wide as possible, three-chamber distributors provide thermal optimisation," Goetz explains. "With these systems it is possible to make the high return temperature of a circuit of, for example, 50 °C usable for the flow of a low-temperature system of, for example, 40 °C - in this project the ventilation systems," he says. "In sum, this hydraulic optimisation leads to lower return temperatures at the storage tank and thus increases the overall efficiency of the system. "The hot water supply is also designed for minimum return temperatures. The hot water is provided by varmeco instantaneous water heaters, so-called fresh water heaters. This means that the hot water in the entire house is only heated when required using the continuous flow principle. "This minimises the risk of legionella multiplication and thus ensures maximum hygiene," Goetz emphasises. It is an exergy-optimised cascade of two that supplies up to 5 m³/h of water at a maximum of 75 °C in the flow.
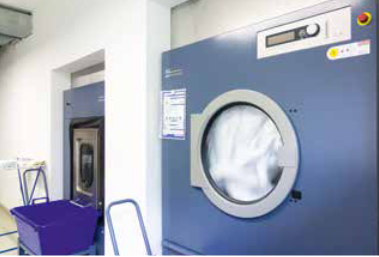
Fig. 5: The back of the washing machine protrudes into the neighbouring room. Here the clean laundry is taken out of the washing machine and put into the dryer.
The cascade also draws its thermal energy from the varmeco storage tank, whereby the heat is provided as needed with the help of a speed-controlled pump.
Low return temperature for hot water preparation
In the exergy-optimised circuit, the heating tasks are separated: "The two-person cascade contains a fresh water heater only for DHW heating and a second one that covers peak demands and tempers the circulation water". Separate pipe routing results in a low return temperature with this system; in this case, the water ideally flows back to the storage tank at 35 °C. Due to the heat loads in the building, which are independent of the weather, such as the frequently running washing machine and tumble dryer, the CHP unit is well utilised all year round. It runs for about 6,500 hours a year. In summer, when only hot water is needed for showering, washing and dishwashing or heat for the laundry room, it runs for about eight hours a day. "Thanks to the generous volume of the heat storage tank and the wide temperature spread, the CHP unit works efficiently and with low cycling," reports the planner. Around 200 starts per year minimise wear.
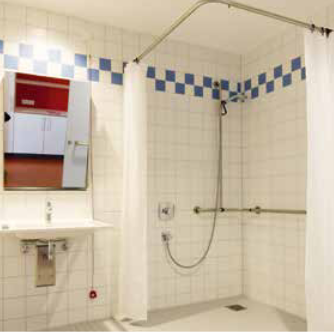
Fig. 6: Barrier-free bathrooms are part of the basic equipment of all flats in the "Inclusive Living Worlds" in Altdorf.
Central heat control with remote access
Heat management is handled by the central varmeco control system "VarCon 380 Pro", which enables parameterisation and display of operating data on the unit or - via a secure, password-protected internet connection - remotely. For example, the control system requests boiler operation if the CHP unit's output is not sufficient to cover the heat demand. The CHP is therefore always given priority. The control system also manages the heating circuits and the hot water preparation, including all pumps. Since the pump drives are speed-controllable, they allow demand-oriented and at the same time energy-saving operation.
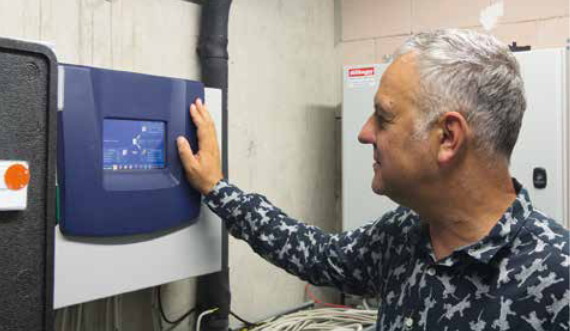
Fig. 7: The heat sources can be prioritised at the varmeco control. This gives the CHP priority over the condensing boiler and it runs for about 6000 hours per year.
CHP covers half the electricity demand
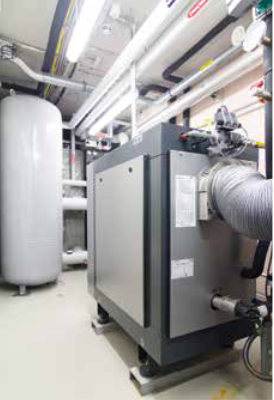
Fig. 9: A Viessmann CHP unit (front) and a 3 m³ varmeco heat storage tank (rear left) supply the "Inclusive Living Worlds" with heat. The system is supplemented by an 80 kW peak-load condensing boiler.
How well heat supply and electricity production harmonise in the small CHP plant is due not least to the precise sizing. The summer base load and the heating demand in the transitional seasons can be covered by the CHP alone; only on relatively cold days is the use of the condensing boiler required. "The simultaneous generation of electricity, which accounts for about 30 % of the CHP's total output, is an excellent fit for providing electrical energy for cooking, refrigerators and freezers, the ventilation systems or auxiliary heating for the washing machine. As a result, only one tenth of the CHP electricity has to be fed into the grid and 90 % is consumed immediately in the house. This in turn covers about half of the total electricity demand," Goetz concludes.
Considering the low remuneration for the CHP electricity - compared to the electricity purchase price - the simultaneity of generation and consumption of electrical energy means additional savings. It is possible not least thanks to the fact that heat supply and consumption are decoupled by the 3 m³ storage tank.